What if There Was a Maintenance Fatigue Rule?
While the author does not see U.S. maintenance fatigue rule anytime soon he is always answering the question, what would the rule look like?
My first answer to the question of a maintenance fatigue rule is that “it is not on the immediate horizon.” In June 2009, the FAA chartered the Flight and Duty Time Limitations and Rest Requirements Aviation Rulemaking Committee (ARC). On Sept. 9, 2009, the ARC delivered its final report to the FAA in the form of a draft Notice of Proposed Rulemaking (NPRM). Associated with a heightened sensitivity to the effects of fatigue on pilots, on “… Aug. 1, 2010, the President signed Public Law (PL) 111-216, Airline Safety and Federal Aviation Administration Extension Act of 2010, which focused on improving aviation safety.
The official release of the NPRM in the Federal Registry was made on Sept. 14, 2010. Following the resolution of more than 8,000 public and industry comments, the 14 CFR Parts 117, 119, and 121 Flight crew member duty and rest requirements were published on Jan. 4, 2012 with an effective date of Jan. 4, 2014. That is pretty fast by rule making standards. That speed was triggered mostly from a very public accident that publicized the lack of adequate rest by both flight crew members (Colgan, Flight 3407 in February 2009). While the NTSB (AAR-10-01) did not attribute fatigue as a primary or contributory cause of the accident, the topic of fatigue-related hazards among flight crews was addressed in the NTSB final report.
Unlike the contributing factors to the Colgan accident there is seldom sufficient root cause analysis to attribute mechanic fatigue to a serious accident. It is more likely that fatigue-related maintenance error would contribute to costly aircraft ground damage, maintenance rework costing time and money, or unfortunate personnel injury. A recent exception is the Sundance Helicopter accident in December 2011. The NTSB (AAR-13-1) reported that mechanic fatigue was a contributing factor.
The paragraphs above do not tell the entire story about attention to maintenance fatigue. Every mechanic has tales about events that were caused by apparent fatigue. Stories about three or four continuous around-the-clock work days are not uncommon. The stories often involve trips to fix a grounded aircraft or big repairs to engines, landing gears, or aircraft damage situations.
While such stories do not violate current U.S. regulations they sure are triggering workers and their management to ask the important questions. “Why would we work such hours with full knowledge of the hazards to aircraft damage, personal injury, or flight safety? We know better and should not allow ourselves to get into such situations.” However, knowledge of fatigue hazards can become clouded by the necessity of meeting deadlines, fulfilling delivery promises, or pocketing some extra overtime wages.
The FAA has not yet drafted or enacted rules to address the hazards associated with fatigue in maintenance. However, the FAA has made significant strides to help industry to address fatigue. Many of the fatigue-related safety interventions have been reported in Aircraft Maintenance Technology magazine. All of the FAA maintenance fatigue safety interventions can be found at the FAA web site www.mxfatigue.com (see Figure 1). Such interventions include:
- A two-hour web-based fatigue awareness course;
- An award-winning 20-minute video (Grounded);
- A real-time fatigue assessment tool; and
- A process and software to show the value of fatigue interventions;
- Multiple plain-language reports and quarterly newsletters about fatigue, and more.
Aviation safety inspectors from the FAA Safety Team; scientists from the Civil Aerospace Medical Institute; and others have spoken at industry forums, delivering practical facts about fatigue in maintenance. FAA leadership with return-on-investment tools has helped to show that there is financial and safety payback in managing maintenance fatigue.
But what would a rule say?
The best way to predict what a maintenance fatigue regulation would look like is to consider the new FAA fatigue rules for pilots and the proposed European Aviation Safety Agency (EASA) rules for maintenance organizations. Both are the result of hundreds of suggestions made by the International Civil Aviation Organization (ICAO), other national aviation authorities, fatigue experts, aviation alphabet groups, organized labor, pilots, mechanics, and others. This is the information that FAA would review to issue a Notice for Proposed Rule Making (NPRM) on human fatigue in maintenance.
FAA flight and duty limitations and rest requirements (14 CFR Part 117):
Part 117 is written for flight crew members operating under Part 121 certificate holders (mostly the scheduled carriers). It is clearly a fatigue rule that mentions fatigue risk management. As you will see, in the EASA section below, the EASA rule is a safety management rule that mentions fatigue. The end result is the same. Part 117 requires that each flight crew member assigned to a flight duty period (FDP) to be fit for duty prior to commencing a flight. Section 117.3 defines “fit for duty” as being physiologically and mentally prepared and capable of performing assigned duties at the highest degree of safety. A worker must attest to the fitness for duty, in writing, at the start of a shift. This fatigue-centered “fit for duty” definition would certainly apply to a maintenance regulation. The regulation also makes the fitness for duty a responsibility of the worker as well as the company. That means that companies must operate on a schedule that ensures that each worker is scheduled with sufficient time for adequate rest. Generally such rest must be in the neighborhood of eight plus hours of uninterrupted rest. Eating, family and social activity, and commuting are not counted as uninterrupted rest.
Part 117 discusses “dead heading,” as a time when the employee is transported from one location to another to perform work. The rule says that dead heading time is duty time. It cannot be counted as rest or sleep. This section of the rule could have impact on mechanics that travel with the aircraft and then commence work while the flight crews head to the hotel for sleep. A maintenance fatigue regulation would likely impact this practice.
The FAA rule is quite explicit about duty times. With a variety of variables like time of operation, number of pilots, acclimation to time zones the rule offers a number of very specific duty times and rest requirements. However, the reasonable rule says that if you operate outside the prescribed times then you must have a fatigue risk management system (FRMS) that offers an “equivalent level of safety” to the prescribed times. The FRMS must include (paraphrased):
- A FRM policy;
- A fatigue training program (required by all operators in all cases);
- A fatigue reporting system;
- A system to monitor flightcrew fatigue;
- An incident reporting process; and
- A performance evaluation.
Let’s be clear. FAA Part 117 says that you strictly follow the prescribed duty times or create a fatigue management system that ensures the equivalent level of safety. That stipulation is also true of the proposed EASA rule for mechanics.
EASA proposed SMS regulations require fatigue risk management
In the May 2013 issue of Aircraft Maintenance Technology magazine, this author talked about an EASA Notice for Proposed Amendment (NPA). The EASA document is titled: "Embodiment of Safety Management System (SMS) requirements into Commission Regulation (EC) No 2042/2003 — Part-14. Unlike FAA’s Part 117, the rule (GM1 145.A.47(b)) is not a fatigue rule but an SMS rule that addresses risk associated with maintenance fatigue. The proposed EASA rule is quite relevant since more than 1,200 repair stations in the United States hold EASA 145 certificates.
EASA provides guidelines in the form of Acceptable Means of Compliance (AMC). The AMC is somewhat comparable to a U.S. Advisory Circular. It is the best place to understand what EASA expects in order to comply with the rule.
Here are a few selected paraphrases from AMC 1 145.A.47(b):
(a) In order to manage fatigue related risk of personnel, as an aviation hazard, the organization should:
(1) Maintain a policy for management of fatigue related risk and define fatigue procedures.
(2) Define and use a work schedule scheme with maximum work hours and minimum rest hours limitations (Refer to EU Directive 2003/88/EC). Define the necessary risk assessment process when the hours are exceeded.
(3) Ensure reporting systems to identify fatigue related hazards.
(4) Assess, manage, and monitor effectiveness or fatigue risk management plan as with other SMS initiatives.
(5) Provide training on the management of fatigue.
The EASA proposed AMC 2 145.A.47(b) provides additional detail saying that the policy and other documentation should be included in the following paraphrased details:
(a) Duty time schedule should address:
(1) Maximum scheduled hours/day;
(2) Maximum allowed hours with overtime;
(3) Maximum hours/month;
(4) Minimum rests between shifts (based on shift length);
(5) Minimum rest hours per week.
All of the above must consider the time of shift:
(b) Hour limits should not be extended for management convenience even if worker agrees. If hours are exceeded then a written plan for fatigue risk management should include:
(1) Additional supervision and independent inspection;
(2) Limitation of task to nonsafety critical;
(3) Use of additional rest breaks; and
(4) Permission to nap in accordance with established guidelines.
The proposed EASA rule comment period is closed and EASA is preparing responses to comments, likely out late summer-early fall. One might expect some push back on the reference to the European Union Work Directive, especially from non-EU holders of the EASA Part 145 certificate. Whether that reference remains in the final rule is immaterial for at least two reasons. First, one of the clauses in the EU Directive is something like: “You don’t have to follow the rule if the worker and the company agrees, as long as you mitigate the risk.” Regardless of that language in the EU Directive, the language of the EASA rule makes a similar caveat on the Directive. If one does not want to create an elaborate plan for extended hours then they can merely follow the directive, included in the AMC.
The bottom line on the proposed EASA FRM regulations and the new FAA Part 117 is that the rules are reasonable. They make sense for safety and for efficient aviation business. They are likely representative of the kind of maintenance fatigue rules that could emerge from FAA sometime in the future. The regulations help ensure that workers are adequately rested and fit for duty. Again, that ensures worker safety, reduction in error when the aircraft is on the ground, and continuing flight safety.
Dr. William Johnson is the FAA Chief Scientific and Technical Advisor for Human Factors in Aircraft Maintenance Systems. Johnson is a member of the Human Factors Advisory Group to the European Aviation Safety Agency (EASA). The Group worked with EASA to define human factors aspects of the proposed Safety Management System regulations.
About the Author
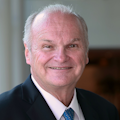
Dr. Bill Johnson
Chief Scientific and Technical Advisor Human Factors in Aviation Maintenance, FAA
““Dr. Bill” Johnson is a familiar name and face to many industry and government aviation audiences. Johnson has been an aviator for over 50 years. He is a pilot, mechanic, scientist/engineer, college professor, and senior executive during his career. That includes 16+ years as the FAA Chief Scientific and Technical Advisor for Human Factors.
Dr. Bill has delivered more than 400 Human Factors speeches and classes in over 50 countries. He has 500 + publications, videos, and other media that serve as the basis for human factors training throughout the world.
Recent significant awards include: The FAA “Charles E. Taylor Master Mechanic” (2020); The Flight Safety Foundation - Airbus “Human Factors in Aviation Safety Award” (2018), and the International Federation of Airworthiness “Sir Francis Whittle Award” (2017).
Starting in 2021 Johnson formed Drbillj.com LLC. In this new venture he continues to bring decades of human factors experience to aviators, worldwide.