One Helicopter Accident, Many Maintenance Lessons
Reading a recent NTSB accident report of a helicopter crash outside Las Vegas, NV, it struck me that all the maintenance issues raised by the Board in this report were issues that show up repeatedly in maintenance accidents, especially helicopter ones. In this case, a Eurocopter AS350 on a sightseeing tour crashed and killed five people, four passengers and the pilot. The Board determined that the helicopter crashed because improper maintenance the day before the accident resulted in the input rod separating from the linkage. Without the input rod connected, the aircraft was, of course, unflyable.
The Board identified four main issues related to maintenance and maintenance practices:
1. Improper reuse of degraded self-locking nuts. The Board found that notwithstanding specific guidance by the FAA and the manufacturer regarding reuse of these parts, the helicopter operator’s maintenance personnel were reusing parts on critical flight controls that did not meet FAA and Eurocopter guidance. The reuse of parts that are worn or degraded is a continuing problem in maintenance and an area that mechanics need to be aware of – especially when the parts are being used in critical flight controls.
2. Maintenance personnel fatigue. The Board found that both the mechanic and inspector were likely fatigued by a change to an earlier shift on the day before the accident when the maintenance was performed. The Board further found that fatigue contributed to the mistakes made by both men, including the “improper securing of the fore/aft servo connection hardware, the improper installation of the hydraulic belt and the inadequate postmaintenance inspection.”
Fatigue continues to contribute to accidents and incidents. Unfortunately, without an adequate rule, maintenance personnel and their supervisors need to be vigilant for signs of fatigue. Changes in shift, and working rotating or midnight shifts, are leading causes of fatigue.
3. Need for workcards with detailed steps. The Board found that the inspection steps were not adequately detailed and therefore were more vulnerable to human error. Again, paperwork issues – whether they be work cards, maintenance manuals or other maintenance procedures - need to be accurate, complete and up-to-date. This area continues to be a leading problem area for all maintenance providers.
4. Fatigue recognition training. The Board further noted that training for mechanics on how to recognize their own fatigue would help eliminate human errors in maintenance and reduce accidents. While the FAA has put out a lot of information on this subject, and a number of operators have begun training on fatigue recognition, it is still not generally provided to mechanics. It is up to each mechanic to familiarize him or herself with the warning signs of fatigue and mitigation measures. The FAA’s maintenance human factors web site is a great starting point: https://hfskyway.faa.gov/HFSkyway/FatigueHome.aspx.
So while the helicopter accident rate is trending in the right direction, the numbers are still disturbingly higher than for other aviation segments. The NTSB findings in this one accident are applicable to many other accidents and incidents involving maintenance failures and are well worth reviewing.
About the Author
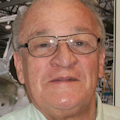
John Goglia
John Goglia has 40+ years experience in the aviation industry. He was the first NTSB member to hold an FAA aircraft mechanic's certificate. He can be reached at [email protected].
John Goglia is an independent aviation safety consultant and Adjunct Professor at Vaughn College of Aeronautics and Technology and regular monthly columnist for four aviation trade publications. He was an airline mechanic for more than 30 years. He has co-authored two text books (Safety Management Systems in Aviation, Ashgate Publishing 2009 and Implementation of Safety Management Systems in Aviation, Ashgate Publishing 2011).