SMA’s Compression-Ignition Engine
callout:
"It's not the most modern technology in some aspects, but it's the most efficient and most reliable technology for aircraft applications."
Thierry Saint Loup, VP SMA Engines
In July 2012 at AirVenture, Cessna announced that it would be installing a SMA SR305-230E-C1 Jet A fuel piston engine in its Cessna Skylane airframe. The SMA engine is a turbocharged four-cylinder air and oil-cooled diesel-cycle engine that produces 227 take off horsepower at 12.2 gallons per hour. If you want an idea of the motive behind Cessna's move, get this; it's certified to burn Jet A, Jet A1, JP8, TS1 (Russian) and #3 (Chinese) fuels.
Cessna's announcement cited the environmental advantages of this switch in this sentence, "The fuel technology used in this engine eliminates concerns about carbon monoxide emissions, fuel mixtures, propeller control, and exhaust gas." It also cited zero lead emissions and zero CO emissions as well as 30 to 40 percent greater fuel efficiency over the avgas-fuel engine it replaces. It's the Turbo Skylane JT-A.
The displacement of the four-cylinder SMA engine is 305 cubic inches (5 liters), the compression ratio is 15:1, the take-off manifold pressure is 90 inches Hg (3 bar), and the installed weight is 460 pounds (209 KG). The time between overhaul (TBO) is now rated at 2,400 hours and that TBO was determined at 90 percent power settings. Cessna warrantees the JT-A for three years or 1,200 hours, whichever comes first.
SMA is predicting that this simple compression-ignition engine will not be hard to maintain for a couple of reasons. According to SMA, there has never been a major mechanical failure with the "E" (for enhanced) version or the earlier version of the engine. No cylinder failures or no valve failures. Second, this SMA engine is simple and it was designed as an aero engine. There's no propeller speed reduction unit (PSRU) or clutch nor does the 15:1 compression ratio put it at the cutting edge of compression-ignition engine development.
The checklist of required maintenance items is small and the maintenance intervals are long. The lack of an magneto-based ignition system — with its ongoing 500-hour magneto inspections and 100-hour spark plug cleaning and rotating chores — will save hundreds of maintenance man-hours over the TBO period of this powerplant.
Development log
SMA flew the first iteration of its SR 305-230 in 1998. That version was flown and tested extensively and was installed in nearly 50 Cessna 182s worldwide under a STC. Based on this operational data and requests from airframe OEMs, the engine was upgraded to the SR305-230E (enhanced) version in 2009. One upgrade was a larger turbo charger; the critical altitude is now 10,000 feet. 175 hp is available at the 20,000-foot certification ceiling.
SMA took a very long view of Jet-A fueled piston aircraft engine development and elected to keep these simplest of engines, the compression-ignition cycle engine, simple. This is shown in the use of a Bosch high-pressure direct-delivery fuel pump instead of electrically pulsed injectors and a common rail fuel manifold; it's also shown in the direct-drive design. There's no engine rpm reduction gearing installed between the engine and the prop. The propeller rpm is governed by a standard hydro-mechanical governor to 2,200 rpm — a speed that marries propeller efficiency with a relatively low noise signature.
ECU control
Thierry Saint Loup is the vice president of SMA engines. SMA is a division of SAFRAN. According to Saint Loup, the SMA engine will require 50 percent less trips to the maintenance shop than an avgas engine. For example, recommended oil change intervals are 100 hours and the SMA maintenance manual (MM) requires compression checks every 600 hours. [Editor's Note: FAR Part 43 Appendix D mandates that these checks be done at every 100-hour or annual inspection.]
Saint Loup says the SMA engine is a "fly-by-wire" engine since the engine control unit (ECU), which controls the rack position on the Bosch fuel injection pump(s), is electrically connected to the pilot's primary power lever. Two potentiometers — for redundancy — on the power quadrant feed the ECU with the pilot's desired power. The ECU combines that signal with several signals from two variables: 1. altitude and air temperature data at the inlet of the turbocharger compressor from the P1/T1 sensor, and 2. fuel temperature ([Tfuel] for fuel density) to arrive at an adjusted fuel flow. The ECU then powers a servo motor that controls the fuel pump rack position which results in injecting the right amount of fuel directly into the combustion chamber to deliver the desired power. In addition, rpm sensor data is used by the ECU during starting and low speed (800- to 1,200-rpm) operations.
The fuel flow/power output curve in the SR305-230E-C1 engine is linear, just like a turbine engine. The ECU, unlike carburetors or fuel injection systems on avgas engines, does not richen the mixture at transition from idle to power up or at high power settings for detonation protection. Compression ignition engines run lean by design with a permanent excess of air (the battle about rich or lean of peak is over!)
The ECU does not monitor EGT, CHT, TIT, or oil pressure or oil temperature since they are not necessary for the fuel flow management. All those parameters are displayed on the G1000, except for EGT, for the pilot to monitor and ensure operating limitations are not exceeded. After an SMA maintenance software download to a laptop computer, data from the engine control unit (ECU) can be displayed live or downloaded through a cable through an aircraft RS-232 port during inspections. Downloaded data includes faults (if any), sensor's data, and engine operating time. This data can then be entered into a spreadsheet type program to chart engine change parameters. It can also be sent to Lycoming or Cessna tech experts to aid in troubleshooting if needed. Lycoming has contracted with Cessna to support the SMA engine. This includes spare parts distribution, warranty administration, and field support.
In addition to the RS-232 data download cabling, a second specialized cable permits ECU map updates. The ECU and the continuously governed propeller results in a pilot workload that is greatly reduced — there's no mixture to adjust and no prop control knob to push and pull. Unlike avgas turbocharged engines, there is no waste gate so erosion and adjustment maintenance is nonexistent. All the exhaust gas goes through the turbine at all power settings.
However, on the far left side of the pilot's switch sub panel, there's a glow plug switch. It's used to activate an automated preheat sequence before starting the engine and provides the most significant benefit when starting in cold conditions.
ECU/engine fault modes and manual mode
All the engine sensor wiring is shielded. Engine control redundancy is provided with primary and secondary sources or sensors. If the ECU diagnostic system detects a fault in either the primary or secondary inputs, the pilot is alerted by a fault annunciation on the instrument panel.
If one sensor or component in any data leg fails for any reason, a "minor fault" light is illuminated. This lets the pilot know that there's a minor problem but that the ECU is still controlling the engine. The airplane can continue to be flown in the normal mode. After completion of the flight an A&P needs to find the fault and fix it. If the "major fault" annunciator is "on" it signals the pilot that the failure has compromised the ability of the ECU to control the engine. The pilot must switch to the manual mode of controlling the engine when the major fault annunciator comes on.
The engine control console has two levers. The left one is the power lever and has a T-configuration. The right one is smaller, is red, and is the mode change lever. The switchover to manual control requires the pilot to pull the power lever back to a clearly marked spot in lever travel. The mode change lever is then moved aft to the manual backup position which disengages the electronic control from the pump, providing the pilot with direct control of the fuel flow through a cable connection between the power lever and the fuel pump. A power chart must be referred to to adjust the manual lever to the correct manifold pressure. There's no requirement to land immediately if a fault light is illuminated.
Economy and ease of operation
According to Saint Loup, a fuel consumption rule-of-thumb for this engine is approximately 5 gallons per 100 horsepower. "The maximum full power fuel consumption at sea level on an ISA standard day is 12.2 gallons per hour which is approximately half the fuel flow of the turbocharged engine it replaces," says Saint Loup. This translates into big advances in range. Saint Loup cites figures showing that the SMA engine will beat the avgas engine in the T182T by 65 percent in range if both engines are flown at extremely high power (90 percent power setting). At more normal cruise power settings the number is around 40 percent.
Cessna should be applauded for bringing the Skylane JT-A to market. Small airplanes have always been vital in the growth of commerce. A "kerosene" burning airplane such as the Skylane JT-A will be the seed that sprouts small commercial aircraft service in countries that lack the avgas distribution and availability enjoyed by U.S. owners and operators.
Required maintenance plan
The SMA SR305-230E-C1 engine in the Cessna Skylane JT-A does present new maintenance challenges to A & P technicians. The Type Certificate Data Sheet (TCDS) is under Societe de Motorisation Aeronautiques.
100 hours:
1. Run up engine with laptop computer connected and record ECU data.
2. Change engine oil and filter.
3. Pull magnetic plug in sump check for metal -- pictures in maintenance manual illustrate maximum allowable metal
4. Inspect oil filter — it's not a spin on; it can't cut it apart but the folds of the screen material can be spread for inspection; and it can be back flushed into a coffee filter or paper towel.
5. Visual inspection every 100 hours to check for:
a. corrosion — the engine is not painted and,
b. integrity of wiring and electric plugs. Unlike much of the non-ignition system wiring on avgas engines that is for information gathering for engine monitors and does not affect engine operation, every wire and plug on the SMA engine must be absolutely airworthy for proper engine operation.
6. Check turbo charger blades and housing for damage; when turbo time in service reaches 600 or 1,800 hours check shaft for axial play every 100 hours until TBO
7. Check and clean or replace inlet air filter
200 hours or at first 50 hours for new or overhauled engines:
Everything in 100 hour inspection and:
R and R spin-on engine fuel filter (Hand Tight Only)
Clean turbocharger oil return check valve
600 hours
Everything in 100-hour and everything in 200-hour services and:
Compression Check
R and R injectors (Exchange program; or can be tested at service centers with proper equipment)
If turbocharger axial play is out of limits, replace bearing pin
1,200 hours
Everything in 100-, 200-, and 600-hour servicing and inspections and:
R & R Turbocharger (overhaul)
Inspect electrical fuel control motor; replace if out of limits
Every 6-8 years
--Replace battery in ECU by exchange (can't replace in field)
2,400 hours/12 years
-R & R Engine (field overhauls are not approved)
Cessna has suspended production of the T182T, the turbo-charged 6-cylinder 235 horsepower Lycoming TIO-540 AK1A powered 182.
Tools, manuals and lubricants
Special tools are required for some maintenance operations. One kit includes data download and ECU update cables. Kits are also available for tools needed during cylinder removals, and tools for fuel pump control unit and turbo-charger maintenance.
Engine parts, tools and supplies can be obtained through Lycoming and Cessna service centers. Maintenance, parts and tools manuals are available from ATP (www.atp.com) and are listed under SMA. Engine oil is Aeroshell Diesel Ultra 5W-40 synthetic. It comes in one liter bottles; to match the engine dipstick that is also marked in liters.
Additional tips:
1. Every wire and connector on this engine is critical for flight safety. Do not ignore routing, clamping and connections
2. Do not clamp or tie wrap anything to the fuel delivery tubing between the fuel pumps and the individual injectors. Fuel pressures in these tubes can reach as high at 16,000 psi; no wear, abrasion or cracking is permitted.
For more information visit http://www.smaengines.com.
Steven Ells began his aviation career in the 1960s maintaining E-1Bs for the U.S. Navy. Steve holds his airframe and powerplant (A&P) certificate, a commercial pilot certificate, and he also holds his Inspection Authorization (IA) endorsement. He worked as a line mechanic and director of maintenance for several DC-3 freight operators, and owned a small maintenance shop in Alaska. Steve has been a tech rep/editor for the Cessna Pilots Association, associate editor for the Aircraft Owners and Pilots Association (AOPA), and now keeps busy as a free-lance aviation writer, maintaining and flying his 1960 Piper Comanche, and helping a neighbor restore a 1939 Piper J-3. He lives on the Central Coast of California. Steve can be reached by visiting www.EllsAviation.com.
About the Author
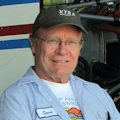
Steven Ells
Steven Ells began his aviation career in the 1960s maintaining E-1Bs for the U.S. Navy. Steve holds his airframe and powerplant (A&P) certificate, a commercial pilot certificate, and he also holds his Inspection Authorization (IA) endorsement. He worked as a line mechanic and director of maintenance for several DC-3 freight operators, and owned a small maintenance shop in Alaska. Steve has been a tech rep/editor for the Cessna Pilots Association, associate editor for the Aircraft Owners and Pilots Association (AOPA), and now keeps busy as a free-lance aviation writer, maintaining and flying his 1960 Piper Comanche, and helping a neighbor restore a 1939 Piper J-3. He lives on the Central Coast of California. Steve can be reached by visiting www.EllsAviation.com.