The European Aviation Safety Agency (EASA) has published proposed amendments for safety management systems (SMS). Johnson, sticks to the facts and sorts out the portions of rule that may impact the 1,200 plus EASA Part 145 repair stations in the United States.
NPA 2013 -1 Safety Management Systems for Maintenance Organizations
The code is simple. EASA published a Notice of Proposed Amendment (NPA) on Jan. 21, 2013 (EASA NPA 2013-1). The comment period closes on May 22, 2013. You will be able to see the comments at http://hub.easa.europa.eu, in the Comment-Response Document (CRD) once it is published.
The three-part document, which addresses all aspects of Maintenance SMS for operators and regulatory authorities, is nearly 500 pages. That is not a problem since Part A contains an excellent 30-page summary (NPA 2013-01 (A). Most of the information presented below is based on NPA 2013-01 (C) ‘Part 145’, which is about 180 pages. The documents are clear, readable, and understandable. You won’t need a lawyer by your side. EASA has done an excellent job to clarify the rational for the proposed SMS rules and the impact of the rules for maintenance organizations. EASA considers not only safety but also costs as exemplified by the following:
… Moreover, the causes and contributing factors of incidents and accidents are very often causing or contributing to production losses or inefficiencies… Effective management systems will, therefore, contribute to a decrease in insurance costs, improved reputation, and commercial success …” pg 24 of Part A.
In the Executive Summary, the document stressed that the primary goal of the proposed changes is to ensure adherence to the international SMS framework established by ICAO (Annex 19). That includes review and modifications to EASA’s current guidance on human factors. EASA says that the proposed changes strive to be flexible and can be proportioned to the size of the organization. It plans to issue another NPA for Part 66 (Personnel Certification) and Part 147 (Training Organizations) in the next stage.
SMS comments
One gets the hint that this NPA has an HF perspective when you read the description of the classic probability-severity matrix. Even before the document addresses human factors they use maintenance fatigue as an example for risk management and include specific accident examples.
“… Maintenance personnel fatigue crystallizes as an area requiring specific attention … Fatigue is an intrinsic aspect of all scheduled or unscheduled maintenance operations … Numerous studies have shown that all of these conditions heighten aircraft maintenance personnel fatigue in their daily tasks. Consequently, the NPA stresses the importance of managing safety hazards stemming from maintenance personnel fatigue and proposes the implementation of a safety risk management scheme…” (Pgs 20-21 of Part A).
In an effort to clarify descriptions EASA did some universal wording changes. For example, the term “quality system” is now “compliance monitoring system.” EASA ensured consistent numbering between the regulation and the Acceptable Means of Compliance AMC. There is also a helpful 25-page table that specifies the “type” of proposed regulation change and a “description.”
Selected human factors changes
In a perfect harmonized world the proposed changes would have no impact on an organization that is structuring their Safety Management Systems to ICAO guidelines. Such guidelines would likely satisfy all National Aviation Authorities (NAA), including FAA. However, in the real world, NAA interpretation of the ICAO framework varies. That is particularly true with respect to human factors (HF) requirements. The interpretation of HF, at EASA, is more prescriptive than the FAA’s. Therefore EASA Part 145 Certificate holders must include HF requirements. As with all EASA rules the Acceptable Means of Compliance (AMC) defines how to implement the regulation. The AMC is in Part C and is used here. Let’s look at a few examples that could affect U.S.-based EASA 145 certificate holders.
Section 145.A.30(b) Personnel Requirement
EASA calls for the explicit identification of someone with the title and responsibility for “Compliance Monitoring” and/or “Safety Manager.” Depending on the size of the organization this can be one person but they must report directly to the accountable manager, who can also serve this responsibility. The responsibilities for this role are described in the AMC.
Section 145.A.30(e) Qualification of HF Training Personnel
There is little change in the familiar HF requirements for maintenance personnel.
“… all maintenance organization personnel should have received an initial and continuation human factors training …” Pg 55, Part C
It includes requirements for initial and continuation HF training. This section also describes who and what shall be included in the training. They recognize that training must be altered to the size of the organization and the type of work completed. That language helps ensure that there is not excessive burden to small organizations.
EASA pays attention to the qualifications of a human factors trainer. It bears repeating:
A competent human factors trainer should meet the following criteria:
1. attended training that is equivalent to the EASA Part 145 HF syllabus … GM1 145.A.30(e)
2. received instruction in training techniques…
3. has worked a minimum of three years within aviation industry, or possesses a suitable academic background
4. has an appropriate level of human factors (knowledge) … in relation to the organization’s HF programme.
The organization must develop and document how each HF trainer is deemed to be qualified, capable, and fully competent as not only a human factors expert but also as a trainer. An evaluation matrix is offered on pg 62-65, Part C.
Section 145.A.47 Production Planning - Fatigue Risk Management
This is a new section that addresses the fatigue related risk in maintenance organization. It is extremely detailed containing about five pages of excellent information. It will be covered in an upcoming AMT article. The document contains all the requirements for documenting a fatigue risk management scheme to include details like: maximum scheduled hours/day and/month, maximum hours with overtime, minimum rest between shifts (based on shift length), and minimum uninterrupted rest hours per week. All of the above must also consider the time of day of the work shift. That section also says: “Reasonable work hour limits should not be exceeded merely for management convenience even when staff is willing to work extended hours…” Pg 78, Part C.
The Fatigue Risk Management must adhere to EU (European Union) Working Time Directive 2003/88/EC, which is contained in the AMC. This is one case where you must consider the exceptions as well as the possible changes. While the EU Directive, at a glance, seems very prescriptive there are a number of cases in which it can be over-ridden when the employer and the employee agree to longer than prescribed hours and shorter than prescribed rest. In such cases a fatigue risk assessment is needed to determine what is safe and reasonable. EASA mentions that the EU Directive is subject to change for aviation workers. Such a change, which could take a long time, could impact U.S. EASA certificate holders.
The AMC also refers FRMS topics to the UK Civil Aviation Publication CAP716 Appendix P.
Section 145.A.62 Reporting Systems
The NPA calls for a beefed up “internal occurrence reporting system.” The system is like the FAA’s Aviation Safety Action Program (ASAP), meaning there will be no changes needed for current U.S. ASAP users. It is likely to encourage additional U.S. companies to adopt the many positive aspects of ASAP. EASA also prescribes training for all who are involved as investigators and participants. Referring to such programs EASA says: “This is important as a strong safety culture is an essential ingredient for effective safety management.” (Pg 11, Part C)
The materials presented in this section of the NPA are nothing short of an excellent tutorial and guidance on an effective error reporting system. It provides the ideal guidance on how to establish an error reporting system and even how to assess the characteristics of your existing system.
Section 145.A.65 (a)(3) Management System
While not HF specific this section provides excellent guidance to build and or assess your current safety risk management programs. It is a “must read” for those involved with SMS, whether you hold an EASA 145 certificate or not.
Implementation schedule
Regulators are always a bit uncertain to specify dates that the proposed amendments will take place. There are a lot of variables, like the amount and natures of the public comments. A reasonable estimate is Fall 2015.
Summary statement
The article has been based solely on the information presented in the NPA, without commentary. However a few words of individual scientific comments are appropriate in closing.
Safety management systems (SMS) are universally supported by all NAAs. SMS is an extension of the many safety systems that have been in place, at most aviation organizations, for a long time. Reasonable standardization of SMS across the world will help all organizations, including business and government, to reinforce the critical responsibility for and commitment to safety that the world’s aviation industry shares.
Aviation authorities foster continuing international safety initiatives by formalizing and requiring a minimum set of safe practices for everyone. Aviation authorities are usually very good at formalizing procedures/practices that can be shared by all. The fact that the authority makes compliance non-negotiable is very important. That ensures that organizations without the wisdom and/or the will are not allowed to be a part of this international industry.
Industry does not have to wait for government to enact practices that promise economic gains, worker satisfaction, personal safety, and the continuing uncompromised safety to travelers. EASA NPA 2013-1, like other authorities, proposes excellent steps to ensure the best possible SMS for those that choose the EASA endorsement. They encourage all organizations to benefit from their guidance.
Dr. William Johnson is the FAA Chief Scientific and Technical Advisor for Human Factors in Aircraft Maintenance Systems. Johnson is a member of the Human Factors Advisory Group to the European Aviation Safety Agency (EASA). The Group worked with EASA to define human factors aspects of the proposed safety management system regulations.
About the Author
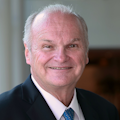
Dr. Bill Johnson
Chief Scientific and Technical Advisor Human Factors in Aviation Maintenance, FAA
““Dr. Bill” Johnson is a familiar name and face to many industry and government aviation audiences. Johnson has been an aviator for over 50 years. He is a pilot, mechanic, scientist/engineer, college professor, and senior executive during his career. That includes 16+ years as the FAA Chief Scientific and Technical Advisor for Human Factors.
Dr. Bill has delivered more than 400 Human Factors speeches and classes in over 50 countries. He has 500 + publications, videos, and other media that serve as the basis for human factors training throughout the world.
Recent significant awards include: The FAA “Charles E. Taylor Master Mechanic” (2020); The Flight Safety Foundation - Airbus “Human Factors in Aviation Safety Award” (2018), and the International Federation of Airworthiness “Sir Francis Whittle Award” (2017).
Starting in 2021 Johnson formed Drbillj.com LLC. In this new venture he continues to bring decades of human factors experience to aviators, worldwide.