It is not uncommon for maintenance and repair facilities to find themselves plagued with struggles training new employees, failure to deliver expected outcomes on time, or the inability to work with consistent cycle times. I might suggest that these types of challenges could be corrected with the standardization of procedures, training, and documented best practices. Establishing standardized practices involves collecting and recording data, which then forms a baseline for continued improvement.
Tribal knowledge vs. a better way
Many times the responsibility to train others within the organization falls on those who have become “fixtures” in the company or repair facility. They possess what is commonly known as “Tribal Knowledge,” which would disappear with them should they leave, or as the saying goes, get hit by a bus tomorrow. But more importantly this type of training or passing on of ways to accomplish a task fails to guarantee consistency in content or maybe even quality. Many times tasks are done a certain way just because that is how it has always been done. But does anyone ever ask “Why”? And does anyone ever ask what the consequences of doing it that way are? Has anyone ever considered there might be a better way?
Let me share a story. This old country boy’s wife sent him to the store for a ham. After he bought it, she asked him why he didn't have the butcher cut off the end of the ham. "This old boy," asked his wife why she wanted the end cut off. She replied that her mother had always done it that way and that was reason enough for her. Since the wife's mother was visiting, they asked her why she always cut off the end of the ham. Mother replied that this was the way her mother did it; Mother, daughter, and "this old boy" then decided to call grandmother and solve this three-generation mystery. Grandmother promptly replied that she cut the end of the ham because her roaster was too small to cook it in one piece. (Ziglar 1975)
In the early 1960s when practical light twins started becoming popular, there was no such thing as a Multiengine Flight Instructor rating. If you were a CFI for airplanes you could teach in single or multiengine, land, or sea based on your pilot ratings. Many people were killed during training accidents as instructors developed their own methods of teaching in dramatic fashion what they had just so recently learned themselves. Many instructors gave their first multiengine instruction the day after they became a multiengine pilot. Some instructors had several thousand hours of multiengine flying and some had less than 10. (King Povenmire)
Continual improvement
Running a successful repair facility is about how the organization functions at every level. Standards for behavior, procedures, and training go a long way toward promoting a culture of continual improvement. We all know too well of the risks inherent in the aviation world, whether we fly the airplanes or repair the airplanes. Creating standards opens the door to identifying those risks, managing them, and best of all mitigating or eliminating them. Today many organizations are “self-insured” for a significantly high amount of consider this; how would your facility be economically affected by a disastrous incident or accident that could have been prevented by an employee complying with a documented procedure.
With the institution of standards your organization becomes more efficient and saves money. You are likely to notice less re-work, improved completion time for tasks, enhanced quality of work, and more positive employee attitudes as a result of decreased frustration in knowing what is clearly expected.
Henry Ford once said, “Today’s standardization, instead of being a barricade against improvement, it is the necessary foundation on which tomorrow’s improvement will be based.” This is as true today as when Mr. Ford first said it.
As a repair facility we are in the service industry. That means we need to satisfy our customers time after time. Back in the day we could almost get by with minimal damage to our reputation if we failed to satisfy a customer on occasion, because customers did not have the technological ability they have today to instantly share an experience, good or bad with an infinite number of people. Now with blogs, tweets, Facebook, You Tube, and a multitude of other ways to distribute a less than desirable service experience, setting service standards for our employees is paramount to continued success.
Expect and enforce standards
But just setting standards is not enough. There must be an expectation from senior management that noncompliance means the employee may be best off to consider a different place to work whose culture is better suited to that employee. One way to accomplish this is by incorporating standards into the organization’s HR policy manual. Compliance with set service standards then becomes quantifiable and an integral element in employee performance.
One word of caution: don’t set standards you have no intention of enforcing. This will likely destroy management’s credibility and minimize the effect of other directives, as they will not be taken seriously. A simpler way to say this is to inspect what you expect.
As repair facility operators, we are not only dependent on our own employees to deliver quality work and service, but we depend equally on outside vendors for parts and other services. Establishing standards with outside vendors will establish benchmarks for good practices, professionalism, and reduced issues with purchase orders and billings. Such standards may take the form of specifications, guidelines, accounting and billing procedures, delivery methods, insurance requirements, and communication processes, just to name a few.
Words of wisdom
Remember everyone must practice the standards consistently before standardization truly exists. Let me offer some words of wisdom from experts who teach lean efficiency.
- Establish an agreed upon set of work procedures
- Each step in the process should be defined and performed repeatedly in the same manner.
- Remove variability which is an enemy of consistency.
- Maximize performance while minimizing waste, requiring costly re-work or scrap.
Define the task and the details of the task; include how long it should take, where it should take place, and the expected outcome. Identify work processes that need improvement and document customer expectations. Do not fail to solicit customer feedback. This can prove to be an invaluable tool in identifying where your team is weak and where they are strong. Many managers fear customer feedback because it may be negative. All customer feedback is positive as it presents an opportunity for change and improvement. It is a gift to become the observer and look at your operation as others see it.
All of us have our core competencies. Many managers may read this article and realize yes, I see the benefit, and our organization would enhance both efficiency and service levels with the institution of standards, but in reality cannot carve out the time to engage in such an initiative. There are companies such as Aviation Training Academy, Diversified Aviation Consulting, BSI, and a host of others who are experts in this area and can make it a simple and affordable process, that when implemented will not only improve the bottom line, but increase both employee and customer retention.
About the Author
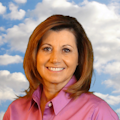
DeborahAnn Cavalcante
DeborahAnn Cavalcante earned her Masters in Aeronautical Science, with a specialization in Safety Management from Embry Riddle Aeronautical University in Daytona, FL, and her Bachelor of Science from VA Tech in Business and Risk Management.
DeborahAnn Cavalcante leads Diversified Aviation Consulting (DAC) and along with her associates has firsthand experience in air carrier operations, private charter aircraft, general aviation operations, military/civilian interface, FBO management, maintenance repair station training, safety training, human factors training, and customer service training. For more information on DAC visit http://www.dac.aero.