Avionics Technology: GWhiz
The future of supporting a Next Gen compliant, fly-by-wire aircraft, just became a reality for me. My company will soon be operating a Gulfstream G650 and I had the opportunity to occupy the jump seat in the green aircraft during the relocation flight from the factory to a completion facility. What an eye-opening experience!
Relatively early in my career among other machines, I worked on the Lockheed JetStar (also a product of Georgia) and became very loyal to the program. Back then, the Gulfstream II was known to us unceremoniously as a “GWhiz.”
As we were preparing to get the latest version Gulfstream airborne, flashbacks from the '70s wafted through my brain. I remembered the awe-inspiring moment when first entering the JetStar flight deck and the feeling of wonder accompanying the how and why of the switch clusters and then over the years becoming proficient in the use of the cadre of strategically arranged switches, lights, and instruments.
In fact just powering up the old Lockheed was like plugging in a well ornamented Christmas tree. Now being somewhat seasoned in the profession, I honestly believed the thrill was gone and had been contemplating the headaches associated with putting a new model, low serial number aircraft into service. Even the thought of a four and a half hour flight in an interiorless machine and possibly having to use an empty paint can as a means of relief for bodily functions was adding to my skepticism and when the factory provided flight crew arrived, it did my heart good to see they each had some gray hair.
Smart probes
The exterior preflight check revealed numerous points of interest including the four “Smart Probes” that sample air data. I came to learn these devices observe both ram and static pressure and can even deduce angle of attack based on pressure changes at different points of the probe. One notable difference between this Gulfstream and my JetStar is the lack of pneumatic hoses within the pitot and static systems. These probes have integral pressure transducers transmitting digital signals to a processor circuit where all necessary air data computations are made.
Total Air Temperature (TAT) probes on each side of the nose area had some familiarity and provide the on board processors with an input voltage that corresponds to air temperature. These probes are designed to compensate for the compressibility of air and provide a chamber where a thermistor can sample a static temperature regardless of aircraft speed.
The nose houses weather radar capable of alerting the flight crew to a potential windshear condition. In the predictive wind shear detection mode, the weather radar processor detects the presence of a microburst, a type of vertical wind shear condition by detecting the Doppler frequency shift of the microwave pulses caused by the microburst ahead of the aircraft and displays the area where it is present to the crew through one of the flight deck display units (DU) and is accompanied by an audible alert.
Enhanced vision system
The top of the nose cone is home to an Enhanced Vision System sensor. It has been said that the revolutionary Gulfstream Enhanced Vision System (EVS) is one of the greatest strides forward in aviation safety since the introduction of the instrument landing system in 1929. EVS, combined with the heads-up display (HUD), delivers a level of situational awareness that pilots in the JetStar days could only dream of.
Inspired by the Forward-Looking Infrared (FLIR) technology developed and manufactured through a Kollsman/Gulfstream partnership where Kollsman pushed infrared technology to develop a camera that operates in the shortwave infrared (SWIR) spectrum. This SWIR sensor is specially tuned to the frequency of runway lights, and is sensitive to the lumens inherent in this environment. The nose mounted sensor sends an image to the HUD as well as being selectable on an appropriate DU enabling the pilots to have an accurate and incisive look in low visibility. Even at night, the Gulfstream’s EVS renders visible runway markings, taxiways, adjacent highways, and the surrounding landscape, drastically reducing the margin for error and for controlled flight into terrain (CFIT) which is the No. 1 danger in aviation today.
LED taxi lights and more
Examining the nose landing gear wheel well revealed that each of the taxi lights have evolved into multi element high intensity white LED segments. Another variant is the use of proximity sensors instead of mechanical switches to control landing gear sequencing. Each nose wheel includes a pressure transducer providing internal tire pressure to the onboard central maintenance computer (CMC) enabling tire pressure monitoring from the flight deck thereby limiting the need for carrying a mechanical pressure gauge on a pre-departure walk-around.
The external fuselage is adorned with an array of strategically located antennae, most of which were easily recognizable. An additional maintenance feature was brought to my attention. I was informed that the onboard Health and Trend Monitoring system has the ability to communicate using a local Wi-Fi or Global System for Mobil-communication (GSM) network providing aircraft system status and fault conditions to a flight tracking group.
As we walked along the right side of the great machine the external Ram Air Turbine (RAT) door was visible. This backup device has the ability to convert airspeed into electrical energy using a propeller driving a generator. It does have the ability to energize flight critical systems in the event primary power sources were unusable.
The wing is a new design for Gulfstream and incorporates a significant sweep to better handle the higher speeds of the G650 and they too have LED navigation lights. The twist with the new LED is they now incorporate a dual capability and can advise via a crew alert system (CAS) message if light has degraded but is still safe for flight or must be repaired.
Digital flight deck
The flight control system is fly-by-wire and no, I don’t mean the cable and pulley version found in the JetStar. The technology incorporates all the features and redundancy that can be expected in modern aircraft. Dual flight computers feed an array of, mostly interchangeable, servo actuators that prompt deflection of primary control surfaces and even spoilers. Like most digitally controlled systems, the fly-by-wire can be monitored from the flight deck and even control surface rigging is simplified by the well-thought-out synoptic pages that can be displayed on the DUs. Monitoring is an inherent feature of the flight deck and dispatch is allowed even with less than full system functionality.
Once the external checks were complete, it did not take long to start the auxiliary power unit (APU), and run through the flight deck configuration using the integrated, customizable electronic checklist. Having spent significant hours occupying the jump seat in the JetStar, I was not really looking forward to the flight across the North American continent in the interior less Gulfstream.
Power and control
Once the engines were online and we taxied onto the runway, there was no doubt in my mind “This was not your long time Georgia-built aircraft.” Even with no interior, it was difficult to tell audibly when the engines reached take off and the G650 leapt into the air after a very short roll. The auto throttles regulated the thrust of the Rolls-Royce engines and required very little attention from the crew.
Once airborne, the flight displays portrayed any bit of information requested by the crew and all selectively displayed on the well-thought-out format on the four DUs. I recollected all the wiring needed by the JetStar to run the servo and synchro driven gauges and displays and how prone the analog signals were to cable shielding problems and how a pilot with a nylon paint brush, dusting instruments would build up an electro magnetic field strong enough to throw off a radio magnetic indicator (RMI).
I recall looking at the wire bundles in the new Gulfstream and noting the electrical wiring interface system (EWIS) precautions that had been taken to prevent digital anomalies and electro magnetic induction (EMI). After a short climb to 40,000 feet, I walked back through the cabin and took note of the various Ethernet and fiber-optic devices that would all be part of the cabin management system (CMS).
I did eventually get back to the jump seat and noticed the Mach indication revealed we were cruising at almost .92 Mach. After four and a half hours aloft, we landed on the West Coast of the United States with zero squawks. My education with this remarkable machine is just beginning and the thrill is back. It is also a fact that the line separating avionics from airframe and engines has been completely erased.
About the only thing I could say was “Gee Whiz, what an aircraft!”
Jim Sparks has been in aviation for 30 years and is a licensed A&P. He is the manager of aviation maintenance for a private company with a fleet including light single engine aircraft, helicopters, and several types of business jets. He can be reached at [email protected].
About the Author
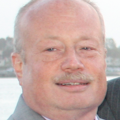
Jim Sparks
Jim Sparks has been maintaining aircraft for almost 40 years with the majority of the time involving Business Aviation activities. Jim’s endeavors have placed him on six of the seven continents contending with numerous situations from routine flight dispatch to critical AOGs. His career includes maintainer, avionics/electrician, educator, tech rep, and director of aircraft maintenance. In addition to other activities he is engaged with ASTM assisting in the global development of criteria defining the Next Tech for NEXTGEN. You can reach him at [email protected].