One thing for certain; if it weren’t for air, none of us would be employed (much less alive). The “air” in aircraft is, for the most part, what makes it all work. Without just the right concentration of various gases making up our atmosphere, engines would not run and there would most probably be no wind beneath our wings. In recent times there has been some publicity regarding devices used to monitor the air surrounding the aircraft.
A 2009 crash of Air France Flight 447 involving an Airbus over the Atlantic Ocean has cast some skepticism on what we all considered to be a reliable means of operating aircraft.
Overreliance on computers
A representative of the Flight Safety Foundation said “the crash highlights a creeping overreliance on computers to fly today's jetliners. Crews blindly follow the computers, but they're still supposed to be able to look through the data and see what their plane is doing.”
The crew of the Air France Airbus never realized that the plane had stalled, was the conclusion of the investigating team and the report's conclusions were more pointed in their criticism of pilot missteps and confusion than preliminary findings.
The causes of the accident were well-documented in a previous report by the French Bureau d'Enquêtes et d'Analyse a year ago, after recovery of the aircraft's flight recorders from the ocean bed following a two-year long search. The crash already has prompted sweeping changes in pilot training.
So just what kind of information should flight crews of today be concerned with regarding air data? Quite frankly, the “need to know” regarding air data is still very relative to the basic theory of flight. An airfoil will produce lift when a differential pressure occurs between the upper and lower surfaces. Most often this is achieved by the aircraft reaching a specific forward velocity and applying a nose up attitude. The factors include static pressure, ram air pressure, and angle of attack (AOA). Temperature is another key player as it will impact air density.
Back to basics
Even with all the sophistication of today’s fly-by-wire aircraft, the basic factors are as important now as they were in Kitty Hawk back on that fateful day in 1903. Unfortunately, as is evident in the demise of AF447, the basic parameters are perhaps not as pronounced in modern aircraft where automation controls are based on inputs from electronic sensors. Just within the last few months directives have been issued by several airworthiness agencies pertaining to air data gathering devices.
Pitot tubes are externally fit on aircraft to sense ram pressure and proper positioning is critical. Although an inherently simple design, the tube is a precision device. Any deformation or blockage in the air inlet will produce some degree of error. Should the angle of the device be varied from the calculated position, a variance in airspeed will be perceived and often minor alignment anomolies are difficult to detect at least visually. The symptom most often spotted is on aircraft with multiple pitot pressure systems experiencing a split in airspeeds where the amount of the split will vary as speed changes. An effective test is to run all pressure-sensing systems with a common test box and if there is no perceivable deviations on the ground, suspect an airflow issue.
Several aircraft manufacturers do provide criteria to verify pitot tube alignment as part of their continued airworthiness programs.
Insect debris
Air inlet blockage is another common occurrence. It is advantageous to remove any protective cover (frequently addressed in pre-flight checklists) prior to attempting flight but the most common culprit is bug infestation. These insects often deposit debris including mud well inside the tube making discovery and removal prior to flight very challenging.
Most operators in regions of known bug populations will allow protective covers to remain on the aircraft until just prior to departure and/or will routinely and carefully clean the inside of the tube. A campaign to verify the free passage of air may also be implemented and can include utilizing a borescope.
It has been confirmed that plating material coming loose at the air inlet can have a significant impact on displayed airspeed. One recent Airworthiness Directive issued by Transport Canada covering the Challenger 600 addresses drain bottles within the pitot system. Under heavy rain conditions the existing bottles can overfill which might result in partial or total blockage. Deficiencies in anti ice elements have caused problems with ram pressure reporting systems as high wattage heaters do provide protection not only from freezing but also rain ingress. Care should always be taken when handling an air data probe when the heating system is energized.
Some newer generation aircraft utilize air data probes that incorporate an electronic module complete with a pressure transducer and a digital output. Typically the functionality of the electronics can be validated anytime the aircraft avionics are powered. These units do allow for a reduction in plumbing but are still subject to deterioration and damage similar to their mechanical counterparts.
Static ports share in some of the anomalies that interfere with pitot systems. Surface defects on or near a sensing port can cause a disruption to airflow resulting in pressure-sensing errors. Even airframe skin deformities and ridges on paint stripes can cause a static defect.
Leaks
Leaks are another common occurrence in a pneumatic air data system. United States Federal Aviation Regulations (FAR) provide direction for testing and return to service. FAR 91.411 stipulates altitude indicating systems be certified every 24 months and uses criteria found in FAR Part 43 Appendix E. It is important to understand the criteria found within are considered the maximum allowed and often time specific manufacturer’s tolerances are tighter. This can be true not only for the primary altimeters but also the standby devices when required.
Moisture drains are one of the most common culprits when it comes to leaks and per Appendix E; leak testing should be accomplished on air data systems anytime the system is open with the exception of moisture drains. Once again, airframe manufacturers' recommendations may require a leak test anytime system integrity is breached.
Transponder testing will generally tie into altimeter testing and shares the 24-month certification requirement per FAR 91.413. Certification of ATC reporting equipment is a bit more involved than the altimetry system and is defined in FAR Part 43 Appendix F and Advisory Circular (AC) 43-6C was issued recently to clarify those capable of returning systems to service.
Freedom of movement
Angle of attack (AOA) has been transformed over the past decade from a system that is a nice to have indication into a prime input to flying the aircraft. Some fly-by-wire or automatic flight control systems (AFCS) use this information as primary drivers for determining flight path and detecting wind shear.
The sensors used to detect airflow relative to the aircraft fuselage most frequently appear as a small moveable airfoil or a cone protruding in the airstream. Freedom of movement should be verified on a daily basis as any binding or rough spots may have serious consequences. European Aviation Safety Agency (EASA) has recently issued an Airworthiness Directive against the AOA probes on several Airbus models.
During Airbus final assembly line flight tests, AOA data from two different aircraft were found to be inaccurate which was confirmed by flight data analysis. The results of the investigation conducted by Airbus and their vendor on the removed sensors revealed oil residue between the housing and the moveable part of the AOA vane. This was the result of incorrect removal of machining oil during the manufacturing process and at low temperatures the oil becomes viscous causing delayed and/or reduced vane movement. Multiple sensors could be simultaneously affected, providing incorrect indications of the pitch angle of the aircraft. This condition, if not corrected, could lead to erroneous AOA information and consequent delayed activation or nonactivation of the protection systems.
In short, air is essential to life and characteristics of airflow relative to an aircraft are critical to ensuring safe and reliable transportation. After all, it’s all about AIRworthiness.
Currently when not writing for AMT, Jim Sparks is the manager of aviation maintenance for a private company with a fleet including light single engine aircraft, helicopters, and several types of business jets. You can reach him at [email protected].
About the Author
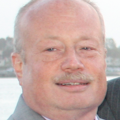
Jim Sparks
Jim Sparks has been maintaining aircraft for almost 40 years with the majority of the time involving Business Aviation activities. Jim’s endeavors have placed him on six of the seven continents contending with numerous situations from routine flight dispatch to critical AOGs. His career includes maintainer, avionics/electrician, educator, tech rep, and director of aircraft maintenance. In addition to other activities he is engaged with ASTM assisting in the global development of criteria defining the Next Tech for NEXTGEN. You can reach him at [email protected].