Elastomeric Components in Helicopter Ops
Vibration isolation in helicopter operation is necessary not only for the comfort of the pilot and passengers, but also for the fatigue life of aircraft components. Excessive vibration creates dynamic loads that affect every part of the helicopter; minimizing and controlling these vibrations has been one of the most significant improvements in helicopter design. New developments in elastomeric technology for passive components - bearings, dampers and isolators - have improved reliability and maintainability while reducing noise and vibration during helicopter operation.
The right design
Maintaining elastomeric components is crucial to the safe operation of the aircraft and for prolonging component life. Understanding the maintainability of these components begins right at the design process. Component manufacturers work very closely with helicopter designers to determine the correct size and life cycle needed for the aircraft.
The goal is to not only design the best performing components but to also assure that the components are maintainable. To achieve this, maintenance personnel are consulted for their opinion on a component’s design and maintainability. This helps to ensure that everyone understands how to operate the helicopter in the most cost-effective manner.
It is important to design the aircraft and its components so that they can be easily taken apart, inspected, and serviced. During maintenance procedures, mechanics will follow the design instructions written by the design team. They closely follow the original guidelines to assess what needs to be corrected during maintenance service.
Elastomeric components
Elastomeric components are comprised of bonded-rubber elastomeric elements that are specially designed to eliminate certain types of vibration. Compared to coiled metal springs, elastomeric elements allow components to be easily configured in different sizes and shapes, and can be readily integrated into various helicopter designs. Elastomeric parts are multi-directional, simple, lightweight, reliable, and can be designed into a system at a moderate cost compared to more complex methods. They also offer the advantage of an extremely long operating life. The service life of some isolators can be from 5,000 to 10,000 flight hours.
These components are generally maintained through visual inspection, and it is essential for the mechanic to understand how these parts operate, the causes and effects of degradation, and the best maintenance practices. A typical helicopter will have several elastomeric components including a pitch-restraint spring, main rotor lead lag damper, main rotor spindle bearing, main rotor CF bearing, tail rotor bearing, corner Pylon isolator, instrument panel isolator, main rotor hub Frahm damper, rotor head assembly, and tail-light isolator. All of these parts must be periodically inspected and maintained to guarantee a safe, vibration-free ride.
The elastomeric parts found on a helicopter include bearings, isolators and dampers.
Elastomeric bearings are composed of natural or synthetic rubber bonded to metal devices that accommodate dynamic motions. They are limited to oscillatory motions from 10 to 90 degrees or up to within 1 inch.
Elastomeric dampers attenuate dynamic motions, most often in the rotor, and can be used with or without special fluids. They offer additional force for a given dynamic motion and provide consistent performance with a wide range of temperatures and dynamic motions.
Elastomeric isolators are installed in a load path to minimize the transmission of dynamic loads or motions. They provide optimal isolation of vibration at important vibration frequencies.
Elastomer degradation
Elastomeric components will degrade due to conditions such as fatigue, overload or tension loading, fluid contamination, and environmental attack from heat and ozone. Typically a combination of these degradation conditions will occur, accelerating the component damage. By thoroughly inspecting the parts, a knowledgeable mechanic will be able to assess when an elastomeric part needs to be overhauled or replaced.
Some of the causes and effects of elastomeric component degradation are:
Fatigue – Elastomer fatigue is the normal degradation mode of a bearing in an oscillatory (dynamic) loading application. A part can experience a considerable amount of crumbing, cracking, and rubber loss before there is noticeable performance impact. Signs of fatigue include “eraser” crumbs, elastomer dust, fuzzy flex cracks, and extrusion of small elastomer segments.
Overload or tension loading – Typically, elastomeric parts are designed to operate in compression and/or shear modes. The main rotor bearings normally carry loads in compression and accommodate motion in shear. Problems can develop due to extreme or inappropriate loading of a healthy bearing or normal loading of a weakened bearing (from oil contamination or fatigue). Damage can also be caused by foreign objects such as tools, fasteners, clamps, and other devices. To determine overload or tension loading fatigue, mechanics should look for the bulk extrusion of elastomer between shims; large, clean cracks in the elastomer; bent or cracked shims; and bent, cracked or gouged major metals.
Fluid contamination – Although elastomeric materials have been developed to improve resistance to various aircraft fluids, solvents, and detergents, there are still some fluids that can cause degradation problems. Petroleum-based oils, fuels, hydraulic fluids, cleaning solvents, and greases can have a devastating effect on the elastomer, and can very quickly cause weakening, swelling, and extrusion. Prolonged fluid attack will degrade the rubber-to-metal bond. Signs of fluid degradation include slick, swollen elastomer; wavy edges; and clean debonding. Parts that have been detrimentally exposed to oils, greases, and fluids should be washed in mild detergent and water or denatured alcohol to prevent further damage. If the parts have been exposed to more volatile fluids such as fuel, solvents, or cleaning fluids, the parts should be dried and the fluid allowed to evaporate.
Environmental degradation – Daily exposure to sunlight, heat, and ozone can cause surface cracking, often appearing perpendicular to the elastomer load. These surface cracks are usually small and do not require the part to be removed. As the part is cycled, the cracks may become sites for initiation of the expected fatigue cracks, so they should be periodically inspected. Most elastomers contain waxes that offer ozone protection. The waxes are designed to reach the surface of the part over time and provide a protective layer, called a “wax bloom.” The wax bloom is gray or brown in appearance, and may flake or crumb as the part is used. Excessive heat will cause most bearings and isolators to become brittle on the exposed surfaces, although heat will not usually cause the elastomer to soften. The rubber-to-metal adhesives are also sensitive to heat, and performance of the part can be degraded as a result of prolonged exposure to high temperatures (above 125 F).
Elastomeric care
All three types of elastomeric components (bearings, isolators, and dampers) have similar inspection and care guidelines. Keep the surfaces clean and clear of dirt, sand, turbine soot, or dust from condensation (soot, dirt, or dust mixing with water vapor). Keep the components free of grease, oil, fuel, hydraulic fluid, or any petroleum contamination.
To avoid prolonged exposure to hostile fluids, cover the elastomeric surface area if cleaning fluids are being used in an adjacent area. To avoid excessive heat, use heat shields on elastomeric components. If cracks or separations in the elastomeric surface area are more than 0.125-inch deep, the part should be removed from service and overhauled.
Follow the maintenance manual at all times to ensure that the correct procedures are utilized during service operations. If there are no specific criteria, the following general guidelines can be followed:
- Remove the elastomeric device if it allows excessive motion or vibration
- Remove the elastomeric device if any of the rubber-to-metal layers are touching each other or are cracked
- Remove the elastomeric device if more than 25 percent of the bonded area has separated
- Superficial cracks due to ozone, heat, or sunlight do not warrant removal of the part
- Any slight oil contamination may be cleaned and the component returned to service
- Severe oil contamination is always cause for removal of the device
- Any unusual damage condition should be evaluated by OEM product support
Keeping up with maintenance
To keep up with changes in maintenance techniques, mechanics should seek out continuing education courses given by aircraft manufacturers, OEMs, and component suppliers. Many organizations offer maintenance conferences where mechanics can receive certification to maintain their FAA Inspection Authorization (IA) accreditation.
The key to properly maintaining elastomeric components is periodic visual inspection. Elastomeric parts are basically “maintenance-free” – the only requirement is visual inspection for degraded elements and then a determination to have the part overhauled or replaced. These periodic checks will assure that the aircraft is kept in safe working condition, while providing a vibration-free ride for the pilot and passengers.
Each elastomeric part will degrade differently over time in different environments, so it is important to know the difference in appearance between a properly working part and one that is starting to degrade. Establishing a time frame for inspections will ensure that all parts are kept in good working order. Unscheduled maintenance events cost time and money, but can be avoided with proper inspection of elastomeric components. For more information visit www.LORD.com.
Douglas F. LeRoy is market and business development manager – Aerospace and Defense for LORD Corporation. Doug leads market and OEM business development in support of LORD Active Vibration Control products and advanced rotor head system technologies within the Americas region, and responsible for the development, coordination, and execution of commercial market and business segment strategies related to these electromechanical value lines.
About the Author
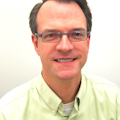
Douglas LeRoy
Douglas F. LeRoy, Market and Business Development Manager LORD Corporation. Doug leads market and OEM business development in support of LORD Active Vibration Control products and advanced rotor head system technologies within the Americas region, and responsible for the development, coordination, and execution of commercial market and business segment strategies related to these electromechanical value lines.