How does Robinson Helicopter Company (RHC) ensure its helicopters are maintained "the Robinson Way?" Provide a school, of course at the Torrance, CA, airport (KTOA). I attended the RHC maintenance course last November.
The week-long course covers maintenance on all three RHC airframes — the piston-powered two-place R-22 and four-place R-44, and the turbine-powered five-place R-66. Classes started each day at 8 a.m. sharp and run past 5 p.m. most days, so don't plan on catching a Friday afternoon flight home.
A one-day R-66 course is also available. These classes fill quickly so plan ahead.
Each day students spent about half their time in the classroom and the other half twisting wrenches, torquing nuts, measuring bolt stretch, and learning how to work their way though RHC specific tasks. These included adjusting coning friction and teeter (flapping) friction; checking and adjusting drive belt tension; learning the methods and using tools used to check the clutch shaft angle and upper and lower sheave V-belt alignment; and adjusting track and balance of the main and tail rotors and balance the fan wheel.
The class was not dry; it was chock-full of real life maintenance shorts cuts and tips. Each of the 11 attendees was handed a class study book. Every morning they were given a test with questions based on their homework reading and class notes.
For instance, what part number lubricant does the free wheeling unit (sprag clutch) use? That question, as many other on the tests were designed to familiarize both new and experienced RHC techs with the RHC maintenance manual and illustrated parts breakdown (IPB). The sound of turning pages rippled through the classroom during these tests.
Instructor Efrain Vargas led the classes. He is an experienced Robinson technician and teacher. He started at RHC in 1986 and worked alongside RHC founder Frank Robinson during R&D for the R-44, the company's second airframe. In addition to his years working at RHC, Vargas owns a Robinson dealership in Mexico and has directed maintenance on RHC helos operating off shore in the tuna fishing fleet. Besides his RHC duties, Vargas travels the world teaching Robinson airframe maintenance classes.
Day one
RHC unlocks the classroom door at 7:45 each day. International attendees included an Army sergeant from Estonia, a civil aviation maintenance inspector from Bangladesh, an experienced helicopter technician from the Philippine Islands, and a (female) aviation maintenance apprentice from an air tour company in China. Other attendees included experienced airframe and powerplant (A&P) helicopter technicians; one who said he was "from Tennessee but temporarily transplanted in Florida;" two from Texas; one from Alaska, one from Oregon, and one who got an early retirement after working on Apaches and Black Hawk helos in the Army.
This one, Eric Norman, worked in the Titusville, FL, training base for Bristow Academy. He was being prepped to take over maintenance management of Bristow's growing fleet of Robinson helos. Lawrence Hromek, a Texan, was attending to fulfill one of the requirements to become a RHC Service Center. That required that he also attend the Lycoming piston engine maintenance and the Rolls-Royce turbine powerplant schools.
After introductions we went on a factory tour. Throughout the course Vargas dispensed tips and hints for RHC helo maintenance such as, "Wash your helo on a daily basis." He defined clean by saying, "If you don't dare lick it, it ain't clean enough." Other tips included, "Rebalance after all maintenance," and "If there's no instruction for a repair in the manual, call the factory."
Vargas also advised the class to always get a component return authorization (CRA) before sending anything to the factory, and then said, "If you want credit for the returned parts, clean them up and treat surface corrosion before shipping."
The tour passed a section of the factory where V-belts were being worn in — each set of belts is run for five hours in the factory before being shipped. That's why it's critical to replace belts in sets and then only in the correct rotation direction. This kind of attention to detail was also demonstrated when Vargas showed us where the drag of every elastomeric bearing was tested — and if necessary run in — to ensure that there was less than 2 ½ inch-pounds of drag on each bearing. If the drag is above 2 ½ inch-pounds it results in vibration.
Here's another one: shake the tail skid to check for loose bolts and elongated bolt holes at the forward inboard leg of the R-22 welded frame. It's a common gripe.
The manuals
Vargas told the class that just because a part is not shown in the part book does not mean you can't buy it. For instance, the complete fuselage is not listed but RHC will sell one as long as it can verify who is buying it and that there's a legitimate reason for the purchase.
The message that was often repeated was to always read instructions completely before beginning a task. And always call the factory customer support people when unsure of the procedural steps or at any other time there's a question.
We were also told that the RHC IPB was not a maintenance reference book; and to always refer to the maintenance manual.
The blades
Main rotor blades were also discussed in some depth. Vargas said it's possible to install a R-44 blade on a R-66 so make sure that both main rotor blades are the correct (and same) part number.
Older blades had a stainless-steel spar/leading edge; newer parts are aluminum. The bond between the skin and the spar is critical. Airworthiness directive (AD) 2011-12-10 requires a daily preflight inspection for exposed (bare metal) of the spar-to-skin joint area on the lower surface of some main rotor blades. This inspection can be signed off by the pilot. RHC provided each class member with a maintenance record appendix for the AD. The kit to aid technicians outline the area required by this inspection is available from RHC.
We were shown how to detect hard landings by measuring the distance from the floor to the tailskid on each model.
Shop time
Beginning the second day of class we met in the shop area after lunch. There, each team — the class was divided into three teams — worked its way through the following tasks on the main rotor assembly: removal and replacement of the hub bearings; swashplate tilting friction adjustment; and teeter friction and coning friction adjustments. Each team had a MR assembly to work on.
After that the following tasks on the drive train were worked through: upper and lower V-belt sheave alignment — there are four possible adjustments on the R-22 and three on the R-44. Others tasks included engine height adjustment; clutch shaft angle adjustment; and V-belt actuator adjustment time.
Through the week
Powerplant service information such as Lycoming engine service bulletin SB388C "Procedure to Determine Exhaust Valve and Guide Condition" was briefly discussed. Each class study book included reprints of applicable service information on engines and accessories. Lycoming and Rolls-Royce service class information is listed on the RHC web site under the "Courses" tab.
Other hands-on shop tasks included the tail rotor drive shaft run out check, a check of the tail rotor static balance; fan wheel remove and replace (R&R) and lubrication of the lower bearing; blade boot R&R including servicing; and a throttle correlation check. Even though the class stayed busy, shop talk pokes such as, "If you got time to lean, you got time to clean," were heard from time to time.
Costs of education
Robinson classes are already full into the second half of 2013. Vargas and CEO Kurt Robinson say there's been talk of adding additional courses in 2013. RHC classes are a bargain at $450; the one day R66 refresher costs $250.
Every month in 2013, Lycoming offers its four-day Engine Service School in Williamsport, PA; cost $725. Lycoming also has a three-day disassembly/assembly class — scheduled immediately following the service school — priced at $700.
The Rolls-Royce powerplant maintenance schools for the RR300 are conducted in Indianapolis, IN. The five-day course costs $2,000. Shops that opt to become Rolls-Royce service centers must attend an additional seven-day course costing $2,800. These classes are only offered on three dates in 2013.
RHC lists a variety of nearby accommodations on its web site; the Ramada Torrance has a special rate for RHC attendees that includes a (carbo-rich) breakfast. There are a wide variety of restaurants within walking distance.
The Torrance airport is located 11 miles south of Los Angeles International (LAX).
Eric Norman, who came to the civil helo world from the U.S. Army, told me that he used to hate Robinson helicopters when he first started working on them.
"Everything was small and some things were hard to get to," he said. "Now I love them because once you know one you know them all."
Norman attended the RHC class because his employer — Bristow Academy — was increasing the size of its Robinson fleet.
RHC has produced more than 10,000 helicopters since that first R-22 was approved on March 16, 1979. Production numbers were quoted at nine per week in November 2012. There are more than 300 back orders for the R66. Two-thirds of RHC helicopters are shipped overseas.
For less than $1,000 for lodging, meals, and tuition, the RHC education is a bargain. Not only do attendees learn "The Robinson Way," they graduate with the assurance that Robinson-proficient technicians are needed throughout the world.
Steven Ells began his aviation career in the 1960s maintaining E-1Bs for the U.S. Navy. Steve holds his airframe and powerplant (A&P) certificate, a commercial pilot certificate, and he also holds his Inspection Authorization (IA) endorsement. He worked as a line mechanic and director of maintenance for several DC-3 freight operators, and owned a small maintenance shop in Alaska. Steve has been a tech rep/editor for the Cessna Pilots Association, associate editor for the Aircraft Owners and Pilots Association (AOPA), and now keeps busy as a freelance aviation writer, maintaining and flying his 1960 Piper Comanche, and helping a neighbor restore a 1939 Piper J-3. He lives on the Central Coast of California. Steve can be reached by visiting www.EllsAviation.com.
About the Author
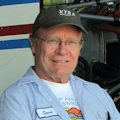
Steven Ells
Steven Ells began his aviation career in the 1960s maintaining E-1Bs for the U.S. Navy. Steve holds his airframe and powerplant (A&P) certificate, a commercial pilot certificate, and he also holds his Inspection Authorization (IA) endorsement. He worked as a line mechanic and director of maintenance for several DC-3 freight operators, and owned a small maintenance shop in Alaska. Steve has been a tech rep/editor for the Cessna Pilots Association, associate editor for the Aircraft Owners and Pilots Association (AOPA), and now keeps busy as a free-lance aviation writer, maintaining and flying his 1960 Piper Comanche, and helping a neighbor restore a 1939 Piper J-3. He lives on the Central Coast of California. Steve can be reached by visiting www.EllsAviation.com.