APPLETON, WI — The Outagamie County Regional Airport (ATW), the fourth-busiest commercial airport in Wisconsin and located just west of Appleton serving the western Fox Cities, was one of ten airports selected by FAA to participate in a Sustainable Master Plan Program.
On the verge of completing a major repurposing of airport land to accomodate a healthy general aviation environment, the airport has invested heavily in infrastructure planning and development in recent years. Now, ATW has broken ground on a new FBO terminal and hangar development expected to be complete in time for EAA's AirVenture in Oshkosh, WI in late July, 2013.
Comments Marty Lenss, airport director at ATW for five years, "Shortly after I took the role as director, we went through a core value process and identified sustainability as a major component.
"We started by looking at the ‘low-hanging fruit’ at the commercial terminal space. We put up a 50 kW photovoltaic system on the terminal roof, and we installed a 12-panel solar heating system on the terminal that provides almost 100 percent of our domestic hot water supply.
"So we had an early approach into efforts related to sustainability. That’s what spurred us to get involved in FAA’s sustainable master plan pilot program."
As a part of that process, the airport has targeted the commercial terminal to be 70 percent more efficient than it is today by 2013.
"Then we started to take a look at GA," explains Lenss. "We have put $15 million into infrastructure — taxiways, roadways, aprons — to support FBO operations on the south side of the field.
"We asked, can we get to net-zero? Let’s go for it."
Mead & Hunt partnered with the Sustainable Engineering Group (SEG) for the design and energy modeling for the new FBO terminal. Moving ahead, the bulk of the general aviation activities will transition away from the commercial terminal area, where the FBO is currently located, to the southside of the field.
"We want that separation between commercial and GA operations," adds Lenss. "The strategy will help with security and safety issues, and also allow for further growth for both types of operations.
"So this is really long-term land use planning initiative, with environmental sustainability very top-of-mind."
Business Drives Growth
Airport fuel numbers are up over previous years at ATW, and things are good currently, relates Lenss. The Tailwind Flight Center, colacated with the airport-owned Platinum Flight Center FBO is very active.
"Some three-quarters of our business is in the GA private sector — and a big portion of that has to do with Gulfstream’s presence here," remarks Lenss. The Appleton Gulfstream facility is responsible for providing major service and modifications to Gulfstream business jets. The facility specializes in providing custom configurations; Appleton is responsible for the final phase of manufacturing for Gulfstream G450 and G550 business jets.
While the FBO is airport-owned, it is privately managed by a private company, Express Airport Services. "I have had a number of phone calls to talk about the model," says Lenss. "Some airports have done different things regarding their FBOs; different models from traditional and more hands-off to a proprietary exclusive relationship where the airport actually owns and operates the FBO.
"We are kind of a hybrid between the two; it’s not proprietary exclusive — it’s not County employees, it’s a private sector business running it on our behalf.
"For us, it’s a model that has worked very well thus far. It’s definitely not a model for everybody. What it does for us is, we are accountable. We have a vested interest in a much different way to ensure high quality service, reasonable rates and charges, and exceptional safety standards, etc.
"It’s managed by the private sector, but we have a bit more leverage when it comes to fuel pricing. We have taken a different approach, and it gives us tremendous flexibility in a number of areas."
Green Features
The GA development at ATW encompasses the design and construction of a new 8,000-square foot executive FBO terminal and hangar complex at a cost of some $5.5 million. The airport's investment was some 60 percent of that cost; the remainder came from Federal and State funding.
Remarks Lenss, "The terminal was interesting because it’s a greenfield development; so we had a clean sheet to work with. The way the GA terminal was approached in terms of design was from a functionality standpoint first, and form second. So the form was fit around the function, which turns the traditional architectural process completely upside down."
With a net-zero target, there is a bit higher premium per square foot, but considering the life of the building — a 50 to 60-year lifespan — the economics begin to work in the airport's favor over time, he adds.
"We looked at dimensions, site orientation to maximize daylight, opportunities for solar panel systems and geothermal systems … and then it was a lot of heavy insulation — a very tight building envelope. We employed durable and sustainable finishes that was all sourced from the local area."
The heating, ventilation, and air conditioning (HVAC) features were tied heavily with ‘smart’ building automation solutions, so that if a window is open, the air conditioning system will not turn on. Similarly, if there is enough natural daylighting coming into the structure, the lights, which are LED, will not turn on.
The airport is also harvesting rainwater for use on the grounds; employs natural rain gardens to manage some of the runoff.
The design of the terminal incorporates high efficiency systems such as radiant floor heating. "We looked at everything from the colors we used — are they absorbing heat? — to a lot of modeling so we could tweak the design," relates Lenss.
Regarding the human side of sustainability — the receptionist at the terminal station has full command of the primary areas in the facility in order to maximize the visibility for employees. "So they can always meet and greet guests appropriately as they arrive, and it helps us utilize our staff more efficiently," he adds.
A Net-Zero Mentality
When the development is complete, it will be LEED-certified.
"A lot of airports are embracing sustainability, and we certainly did with regard to the master planning," comments Lenss. "We conducted a greenhouse gas emissions inventory so we know where we are at.
"I firmly believe there will be more of those activities coming from a regulatory standpoint. And if you don’t know where you are at today, it’s hard to even respond in the rulemaking process. Without that, you can only provide emotional responses to the regulations, as opposed to a data-drive response.
"That’s one reason we put our toe in it. And, at the end of the day, it’s the right thing to do.
"We fully intend to have a net-zero impact from an environmental standpoint, that is — we will not have a carbon footprint, and any environmental impact we do have will be offset by measures of sustainability present throughout the organization."
ATW has wrapped up its sustainable master plan; the County board has accepted. Now, says Lenss, the airport will start to develop metrics around the sustainability features so it can track the projects, and determine what the return is with regard to energy consumption.
"Then we will start to model that; it will take us a few years to build the data, but then we should really start to see some clear trendlines."
For example, the commercial terminal represents about $350,000 per year in utilities; that cost goes to the rate-base of the carriers and tenants. "So if we can drive that cost down, or even flatline it, we are winning, and saving," he adds.
"We always circle back to, in some shape or fashion, enhancing air service for the community."
The New Economy
Another new development for ATW is coming into fruition as well. The Fox Valley Technical College has agreed to lease airport land and develop a public safety training center (see sidebar).
Lenss relates the airport started working on the proposal some four and a half years ago. The parcel of land owned by the airport was a $5,000 per year agriculture lease; now it will bring in some $150,000 of non-aeronautical revenue.
The lease was negotiated for a total term of 50 years; a 20-year initial term with three ten year options. The goal is to break ground March 1, 2013 with a construction time of some two years; a $34 million development.
"We have had preliminary discussions with the technical college to do some of the continuous commissioning of our HVAC systems, and make sure they are always in that 95 percent efficiency rating," says Lenss.
"So, as a public building, in partnership with the tech college, it would become a living lab … the only net-zero energy use building that I am aware of, on an airport.
"That furthers that community-airport partnership, which drives a a positive perception by the public at large of what we are doing out here. The relationship just really gives us some neat opportunities to explore possible synergies that may exist, and work together for a common benefit.
"That’s the type of thing we want to do. Collaborate with local businesses and organizations in ways we haven’t done before … in my opinion, that is what airports need to do in the new economy.
"In 2008, aeronautical revenue was at 59 percent. In our 2013 budget, airline revenue is now at 43 percent. So in a couple years, we should be below 40 percent of our revenue being derived from airlines.
"The need to grow non-aeronautical revenue at the airport is critical in this new economy."
Coming To ATW: Fox Valley Technical College
Four disciplines Of Public Safety In One Training Site
Thanks to the passage of a $66.5 million public referendum by nearly a 2-1 margin, Fox Valley Technical College (FVTC), Appleton, Wisconsin, recently broke ground on its flagship project as part of the successful vote.
The more than 90,000-square foot Public Safety Training Center (PSTC) at the Outagamie County Regional Airport (ATW) is scheduled to open in late fall of 2014. The $34 million center will be the only facility in the nation to integrate emergency medical services, structural firefighting, law enforcement, and wildland fire training for enhanced responses to virtually any type of public safety call.
“Public safety leaders understand the significance of continuous education in a post 9/11 era,” says Dr. Patricia Robinson, dean of FVTC’s Public Safety Division. “This new center is a model for interdisciplinary training in public safety.”
The PSTC will include technology to simulate almost any emergency situation. Tactical training features include a mock village, an expanded shooting range, an emergency vehicle operation driving pad, trench and water rescue scenarios, and more.
Enrollment in FVTC’s Criminal Justice training programs has increased 60 percent between 2008 and 2011, but growing demands for continuous education for public safety practitioners locally and nationwide serve as the primary impetus behind the effort. The college also estimates that some 500 trainees will use this new facility on a daily basis.
For more info, visit: www.fvtc.edu/pstc.
Facts & Figures
Airport Owner: Outagamie County; the airport organization is an self-sufficient enterprise fund.
Based Aircraft: 60
FBO: Platinum Flight Center (airport-owned, privately managed)
Annual Revenues: Just over $9 million
Fuel Flowage Fee: Five and a half cents
FBO Fuel Sales (Sept. '12): Jet A — 31,961 gallons; 100LL — 3,673 gallons
Annual Operations: 35-40,000; 70 percent are general aviation (jet/piston) — Of the 70 percent, 50 percent are jet/turbine
Commercial Airlines: Some 20 flights per day
Hangarage: Some 50,000 square feet of common hangar space, includes the 12,000-square foot executive hangar that will be constructed adjacent to the new FBO terminal. Hangar spaces is currently full.
Development Details
General Contractor: SMA Construction Services, LLC.
Design (Architectural/Civil/Mechanical/Structural/Plumbing/Fire/Electrical): Mead & Hunt, Inc
Energy Modeling and Commissioning: Sustainable Engineering Group (SEG); Madison, WI
About the Author
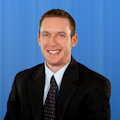