Airports and businesses based at the airport setting have been working hard at 'going green' for some time now. Operating and building with sustainability in mind has become an industry mainstay, and with more buisnesses accepting the need to be environmentally responsible in all aspects of operation, some very good best practices and lessons learned are becoming apparant.
The LEED (Leadership in Energy and Environmental Design) certification program was developed by the U.S. Green Building Council and is used by many organizations as a way to benchmark specific goals realted to sustainability.
At the Chattanooga Metropolitan Airport (CHA), a LEED Platinum-certified corporate flight center is now online, as well as a Leed Gold-certified hangar facility. The FBO terminal, managed by Wilson Air Center, is the first facility of its kind in the world to recieve platinum certification.
Comments airport authority president, Terry Hart, "Over the past 40 years, Chattanooga has transformed itself from one of the most polluted cities in the nation to one of the cleanest.
"As a cornerstone of the community, the Chattanooga Metropolitan Airport Authority (CMAA) shares the city's vision for sustainability. Five years ago, the airport pledged to reduce its environmental footprint and started small by initiating sustainable practices both on the airfield and within the commercial terminal.
"Over time, the airport has incorporated this green philosophy into larger projects including a solar farm and LEED-designed facilities."
But going LEED isn't the only way to go green. Mercer Dye of Dye Aviation Facilities says there’s a two-step method to figuring out whether to go LEED or not. Dye has more than 35 years of experience in the development of commercial and industrial projects, and in the last 30 years he has been concentrated on the development of aviation support facilities.
"Once you have the parameters of the building conceptionalized, you can hire LEED-Certified engineers, and they will perform an analysis of the project — they will show you where the low-hanging fruit is, and they will show how to become LEED-Certified, and demonstrate the cost of that," explains Dye.
"But, becoming LEED-Certified can be an expensive endeavor, and the paybacks are subject to discussion. A lot of my customers get the front-end work done, and then have a nice list of low-hanging fruit to go after, and will then not worry about the LEED-Certification."
Low-Hanging Fruit
Dye Aviation Facilities develops projects on greenfield sites as well as works with rennovations and expansions. Some 60-70 percent of Dye's business is in new construction. "What we do, whether it’s an FBO client or a corporate client, is begin our design work really understanding what the core goals are," explains Dye.
"There are some companies who are invested in green technology, not for the pure economics of it. Some companies have become committed to building green and they don’t have to demonstrate a return on investment.
"My companies have to demonstrate that return on investment to stockholders. The first thing we do is take advantage of all the low-hanging fruit in the design. There are cheap things to do.
"We use energy-efficient materials; lots of insulation; orient the buildings where they absorb as little heat as possible during certain times of the year — we try to take advantage of every type of passive trick we can use in the basic design of the building.
"And we really address the building envelope — using a lot of insulation and making sure it’s nice and tight."
The next step is in looking at the various systems — electrical, heating, and lighting, for example. "Lighting is a big component here; we are using more and more intelligent lighting systems in combination with skylights and sidelights in the buildings," says Dye.
Heating/Cooling
Heating and cooling the facility is also a big energy-user resulting in high operational costs.
"For years, we have been sold on these very large-diameter ceiling fans in hangars," relates Dye. "Big-Ass Fans has an amazing product when used in combination with a well-designed heating and ventilation system. In the winter time, it takes naturally warmer air at the top of the hangar and pushes it down to the floor at very little cost.
"In the summer, it creates air movement, which with the evaporative effect of the wind blowing around, gives a cooling sensation."
For pure economy and safety with regard to heating systems, Dye prefers low-intensity infrared heating systems. "The technology heats the concrete slab, which in-turn heats the environment," says Dye. "That provides very good comfort at a low operating cost.
"When we can’t use the infrared technology, we use a forced-air unit heater system," he adds.
The company is beginning to look at geo-thermal heating sources in certain climate areas. Geo-thermal can be a cost-effective and very efficient way to go for heating and air conditioning," relates Dye.
"It’s becoming very popular in residential projects; it is not real popular in many industrial and commercial applications right now, but the technology is getting better and more economical for larger systems."
Sustainability At CHA
Chattanooga Metropolitan Airport Authority (CMAA) president Terry Hart began his career as a travel agent, and joined the Britt Airways airline in 1981. After more than 25 years in the airline industry, Hart made the move to Chattanooga and served on the airport managment team. In June of this year, he was named president and CEO after serving as VP of airport operations for four years.
Hart explains that lighting was one of the first initiatives the airport tackled with regard to sustainability. Old, incandescent lights on the airfield were systematically replaced with more energy efficient LEDs as part of each taxiway construction project.
Lighting on the exterior of the terminal building was upgraded from metal-halide to compact florescent lights. On the interior of the terminal, lighting was changed to compact florescent lights, and time, motion, and light detectors were installed to ensure that lights were only used when needed.
"With these simple changes, the airport reduced its electric consumption by one full megawatt each year over the past five years, and we continue to replace less efficient lights and equipment with more sustainable products," comments Hart.
"Sometimes the smallest changes can have big impacts in our efforts to conserve the earth's resources. The CMAA has evaluated day-to-day operations and made conscious decisions to focus on sustainability in areas like green cleaning products, green pest control, green landscaping practices, and recycling programs."
With regard to recycling, all asphalt removed during reconstruction projects is recycled and reused to produce aggregate for new asphalt at the airport, adds Hart. Last year, the airport began restoring pavement with an environmentally safe product instead of traditional coal tar.
Solar Solutions
The CMAA has developed a solar vision that includes a three megawatt solar farm on the airfield. The first step in fulfilling that vision was to establish a one megawatt solar farm on the southwest corner of the airfield.
The location was unusable for aviation purposes due to its close proximity to the runway. "However, it was the perfect site to develop a one megawatt fixed ground mount solar farm," remarks Hart. "The solar farm construction started in October 2011 and was completed in December 2011; the power produced from this farm will provide the energy to offset the entire West Side Corporate Aviation Campus.
"Once the full vision of three megawatts is realized, the Chattanooga Airport will be effectively energy self-sufficient and carbon neutral," he adds.
The solar farm was funded through the FAA Voluntary Airport Low Emission (VALE) Grant. VALE Grants are air quality grants issued to airports that are in non-attainment or maintenance areas.
Says Dye, "We do a great deal of research on solar technology. When all is said and done, we are not able to show a return on investment that’s within the scope of what some are willing to spend on that effort right now.
"Most of the solutions are very high-tech … how long do those systems last, and for how long are they efficient? Those are the big questions regarding life cycle and efficiency related to some solar technology solutions.
"I think people need to study them very carefully. If you are paying for these systems by yourself, without some form of accelerated tax depreciation or government rebate, it’s very hard to calculate a return on investment."
Future Of Sustainability
Comments Hart, "While some of the airport's green efforts have been small, common-sense, and methodical, a few have been game changers.
"Working toward LEED certification for all new construction projects is a game changer. The West Side Corporate Aviation Development at CHA was completed in July 2011 and has been awarded the highest level of LEED certification. The development was built with environmental sustainability, occupant health, comfort, and cost savings in mind."
Explains Dye, "I think we are going to get into ‘smart’ building materials … where building side-walls are not just providing the skin of a building, but are also a solar water-heating panel, for example.
"Sustainable solutions will be architecturally integrated into the skin of the building. Certainly there are people out there making wall panels that provide heat or ventilation right now; much of this will come on slowly and in increments."
CHA LEED Snapshot
The Wilson Air terminal facility at the Chattanooga Metropolitan Airport (CHA) was awarded platinum certification from the U.S. Green Building Council’s (USGBC) Leadership in Energy and Environmental Design (LEED) green building certification program.
The 12,000 square foot aircraft hangar which is co-located on the West Side Aviation Campus was certified as a LEED Gold facility.
LEED certification of the FBO terminal and hangar facility was based on a number of green design and construction features.
At the terminal:
- More than 3,000 solar panels were installed just south of the terminal, generating more than one megawatt of clean power every year.
- 95 percent of all construction waste was recycled.
- Furniture throughout the facility was sourced from regional providers, limiting the pollution required to transport materials.
- Alternative transportation is encouraged and easily accessible for both employees and clients, with direct access to CARTA, bike storage and changing rooms, and reserved parking for low emissions and fuel efficient vehicles.
- Landscaping throughout the campus is comprised of indigenous plants requiring very little water for hydration.
- All steel beams in the structure and the sheeting contain recycled materials.
- 95 percent of all construction waste was recycled.
- Contains a high energy efficiency infrared system.
- Unique day lighting functionality with windows in the hangar facility.
About the Author
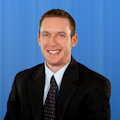