Airline maintenance organizations, of all sizes, have many programs to help manage human error. Organizations with European Aviation Safety Agency (EASA) repair station certificates have mandatory human factors requirements. Other airlines and MROs, without such regulations, choose to implement human factors programs to reduce human error, ensure continuing safety, and control cost. Addressing human performance is simply, good business. This article looks at eight maintenance human factors challenges and solutions that are working in general aviation and airline maintenance organizations.
Airline maintenance/MRO organizations and regulations
One might envision airline maintenance organizations (14 CFR Part 121 or 135) or maintenance and repair organizations (MROs) (14 CFR Part 145) as large factories with hundreds, if not thousands, of maintenance workers. Well, that vision is not correct. Aviation maintenance is comprised of a lot of small businesses. Here are some interesting facts:
- Thirty of the 4,100 repair stations that hold a U.S. Part 145 certificate have more than 2,000 employees.
- Fifty percent of the repair stations have less than 10 employees.
- More than 80 percent have less than 50 employees.
- Thirty percent of U.S. repair stations hold EASA certificates.
- Since the larger repair stations have the EASA certificates, one can estimate that more than half of U.S. airline and airline MRO mechanics work both EASA rules and FAA rules.
General aviation maintenance organizations
Some may have an inaccurate vision of general aviation maintenance organizations. They are seldom merely small hangars working at a slow pace. Like airlines and MROs, GA shops are mostly small businesses. They are geographically dispersed and serve considerably more owner-customers than the big guys. GA shops service diverse aircraft types and have more individuals/owners telling them not only to hurry up but also to keep the cost low. These small shops do not have the economy-of-scale, like airlines and MROs, when it comes to investing in equipment, documentation systems, and other business processes.
Similar challenges
Although we have highlighted the differences, when you compare GA to air carrier maintenance there are likely more similarities than differences. Both groups have the challenge of finding, training, and keeping qualified personnel. Both struggle with the challenge of maintaining aging aircraft while staying abreast with the evolving aircraft, systems, avionics, and test equipment technology. Both groups feel the pinch of providing fair wages and benefits while trying to control the cost of every person-hour involved in maintenance. Both struggle to minimize the cost of mistakes and maximize the continuing aircraft and worker safety. Finally, both groups cope with the human factors that affect nearly every challenge listed above.
Shared human factors challenges
In 2010 FAA sponsored a small invited workshop to identify the critical human factors challenges in maintenance. All segments of aviation maintenance personnel assembled to create a list of the “top eight” human factors challenges (See Table 1). By the way, a European group also created a list of maintenance human factors challenges with considerable overlap with the U.S. list. Let’s look at airline and general aviation maintenance approaches to these U.S. challenges.
Use of Technical Pubs |
Fatigue/Alertness |
Safety Culture |
Event Reporting Data (MEDA, LOSA, ASAP) |
Return-on-Investment |
Establish HF as Priority |
Professionalism (Gen Gaps, etc.) |
Required Inspection Items |
Table 1. Top eight maintenance human factors challenges
1. Documentation and procedures
Technical documentation and procedures are a big challenge for everyone! It is the No. 1 reason that FAA takes actions against aviation maintenance technicians, that mechanics complete the NASA Aviation Safety Reports, and that MROs run into errors and reworks. Airlines and MROs work from a combination of manufacturers’ publications and company work cards. The challenge is to keep things up to date and to continuously ensure that instructions are compatible. For the MROs it is especially tough because they must use the work cards for each airline customer. There are as many ways to complete a specific task as there are customers.
GA maintenance organizations work on hundreds of aircraft types and models. Each aircraft often has a 30+ year collection of modifications and supplemental type certificates that may need checking. A sign-off for an annual inspection essentially certifies the aircraft and its component documentation for all work since the aircraft was new. One saving grace for GA paperwork is companies like ATP. Such technical publishers assemble the documents from government and manufacturers to streamline the search for proper requirements and procedures. However such companies can only provide the documents. Companies and AMTs must make the commitment to follow the procedures.
Airlines, MROs, and GA maintenance service suppliers must ensure logistical access to readable/usable documents. Availability of documents must be matched with a culture that values following procedures. Individual managers and AMTs can make a difference by always identifying procedures that are difficult or incorrect. Organizations and manufacturers must amend procedures as soon as possible. That action can help ensure that technical documentation is not only high value but also perceived as high value by the maintenance workers that use them.
2. Fatigued workers
The workshop delegates ranked fatigue as the second largest risk to safe work. The fatigue challenge may be larger at MROs and airlines but GA is not immune. An FAA study in 1999-2000 collected more than 50,000 hours of data from airline maintenance and MRO workers and found that the average sleep was just over five hours/day. A 2006 study of the general American population showed that men get about six hours. Both numbers are well below the recommended eight hours of sleep per day.
The airline maintenance occupation, especially airlines, conducts a lot of night and early morning work. The combination of insufficient rest, long working hours, and middle of the night maintenance activity has a significant impact on worker performance. Since airliners must be maintained during the night the solution can be found in increased sleep duration and science-based scheduling. Other interventions, like napping, strategic use of caffeine, adjusting lighting, and matching rested workers to critical tasks are all partial solutions.
Both airlines and general aviation mechanics have been using the FAA’s computer-based fatigue countermeasure training. The two-hour course, available at www.faasafety.gov, has been used by more than 25,000 mechanics. There a number of U.S. and international MROs and airlines that have made the fatigue training mandatory for all workers. The FAA also provides additional support for fatigue awareness at www.mxfatigue.com.
3. Safety culture
The two words, safety culture, are easy to say but represent attitudes and programs that require significant corporate and individual worker commitment. It is characterized by a shared value in the importance of safety and the ability of every worker to articulate, understand, and perform their individual actions to ensure safety. A five-person GA shop or a 5,000-employee MRO can have a safety culture.
Whether you are maintaining airliners or small aircraft, the safety culture must be communicated from the senior executive level. A safety culture has ways for all personnel to report safety threats, errors, or even violations that may impact safety. The industrywide push for the application of safety management systems (SMS) will eventually have a positive impact on GA.
4. Event reporting data
It is difficult to discuss safety culture and SMS without talking about event reporting.
Safety management is a formalization of the safety process. It relies on the process of keeping excellent records, observing, and recording company performance. SMS uses appropriate key indicators to understand why something may have gone wrong, or to predict trends of impending issues. SMS can help companies to look at emerging threats using current data. This helps ensure continuing safety.
Airlines and MROs rely on key performance indicators (KPIs) to impact safety and financial decisions. Flight deck technology makes it possible to record every action of the pilot or aircraft. Airlines know the quality of nearly every take-off, approach, and landing. This can help with decision making about procedures, training, crew pairing, and more. Of course, the airlines can also watch engine and aircraft system performance to know temperatures, vibration, fuel flow, and hundreds of other data points. MROs and airline maintenance organizations can count maintenance-caused delays or returns, rework, warranty issues, and more. Even with all of this data, it is difficult to fully identify and understand the contributing factors of a maintenance discrepancy. For maintenance performance, human generated event reports are better than automated data collection.
Airline/MROs use initiatives like the Aviation Safety Action Program (ASAP) to help learn about threats and also about ways to reduce them. These safety initiatives can be scaled to GA maintenance organizations. Boeing has created a process to record a maintenance error and to help find “corrective actions.” The Boeing Maintenance Error Decision Aid (MEDA) has been around since the mid-'90s and is used by more than 700 airlines worldwide. Mid- and larger-sized GA maintenance organizations are using MEDA to help support SMS. Other programs, like the new FAA-A4A Maintenance and Ramp Line Operations Safety Assessment (MRLOSA) apply peer-to-peer reviews of normal performance. Scaled to GA, MRLOSA can collect data about threats before they become errors or injuries. Systems like MEDA and MRLOSA are not only a foundation for SMS but also a means to foster a safety culture.
5. Return on investment
Senior executives typically invest in materials or services that will improve the bottom line. To help make safety a priority, we must demonstrate that safety interventions not only improve quality and safety but also lower costs. If human factors programs show return on investment (ROI) then they will not be an easy target in lean times. AMT (July 2012) discussed ASAP and ROI as an example of how programs can combine to show the impact of HF initiatives.
General aviation and airline maintenance organizations can apply the same solutions. First, make it a priority to identify a few events that warrant corrective actions. Second, determine the cost of the events, the cost of the intervention, and how many events will likely be reduced by the intervention. Third, input the data into the FAA’s maintenance ROI software that is available at www.mxfatigue.com. The software is a well-documented easy-to-use set of linked Excel spreadsheets. This author has witnessed numerous maintenance organizations express amazement regarding how easy it is to use. Of course, the hard part is assigning values and event counts to the challenge, the solutions, and the eventual outcome.
6. Establish HF as a priority
There is a wide range of attitudes about human factors programs for maintenance. There are CEOs and managing directors of large and small maintenance organizations that can deliver a speech that promotes the importance of corporate attention to human factors. The same is true about regulators from all ranks. Some deliver heartfelt messages as if they were the instructors of a human factors course. When leadership has the knowledge and commitment it is reflected throughout the organization. That is true for any size company, fixing any size aircraft.
Recently, an international safety consultant commented that, initially, the quality of human factors programs, in the United States, went down after repair stations began following the EASA HF training requirements. He said that he saw many organizations were driven only by the need to check off the regulatory requirement rather than to find value in the HF program. Organizations are now realizing that human factors programs are an important piece of a safety management system.
There is an across-the-board effort to raise the priority of HF programs. The programs must be applied/practical and based on identified company deficiencies and examples. HF practitioners must demonstrate the safety and business case of the programs. The HF programs must become an integral part of the SMS.
7. Professionalism
Workers must be internally as well as externally motivated to “do the right thing.” That includes attitudes and behaviors on topics like: uncompromised compliance with company procedures and technical documentation; understanding and adherence to fitness for duty requirements with particular regard for fatigue issues; sensitivity to culture and the importance of workplace communication among diverse ages and nationalities; and other nontechnical and technical behavior and performance. Again, like safety culture, professionalism is contagious. There are no notable differences in the requirement for professionalism between GA and airline maintenance personnel.
8. Required inspection items
The topic of “required inspection items” made No. 8 on the important challenges in maintenance human factors. The reason is that many events in airlines and in general aviation are a result of incomplete inspection. On a risk assessment matrix, a missed inspection is not always ranked as “catastrophic” but it is ranked as a frequent occurrence. The term “required inspection” means just that. The workshop delegates felt that the tasks that require a double inspection are often treated as a normal and routine maintenance task. There is another risk that a mechanic may be lax, knowing that the work would have another inspection. The inspector, on the other hand, may expect that the mechanic was especially diligent due to the importance of the task and because it would get “an extra set of eyes” before flight. The result could be inspector complacency.
What do you need to do?
The solution to the “required inspection items” tasks falls into all of the solutions described in challenges 1-8. The solutions work in GA and airline maintenance environments. And the solutions make a good ending to this article. That includes:
1) Adhere to procedures/documentation;
2) Get proper rest and pay attention to schedules and to time of day/night;
3) Establish and nurture a safety culture that
4) Reports and analyzes data and
5) Demonstrates return on investment;
6) Make human factors a priority;
7) Apply professional behavior to delivery of safe and efficient aircraft maintenance
8) Pay attention to work that requires double inspection.
About the Author
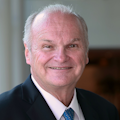
Dr. Bill Johnson
Chief Scientific and Technical Advisor Human Factors in Aviation Maintenance, FAA
““Dr. Bill” Johnson is a familiar name and face to many industry and government aviation audiences. Johnson has been an aviator for over 50 years. He is a pilot, mechanic, scientist/engineer, college professor, and senior executive during his career. That includes 16+ years as the FAA Chief Scientific and Technical Advisor for Human Factors.
Dr. Bill has delivered more than 400 Human Factors speeches and classes in over 50 countries. He has 500 + publications, videos, and other media that serve as the basis for human factors training throughout the world.
Recent significant awards include: The FAA “Charles E. Taylor Master Mechanic” (2020); The Flight Safety Foundation - Airbus “Human Factors in Aviation Safety Award” (2018), and the International Federation of Airworthiness “Sir Francis Whittle Award” (2017).
Starting in 2021 Johnson formed Drbillj.com LLC. In this new venture he continues to bring decades of human factors experience to aviators, worldwide.