“Show me the success story for FAA’s Aviation Safety Action Program and other such safety initiatives.” I receive that request from senior management of both the commercial and government sectors. I recently made the promise to find the examples and document the “big stories” that demonstrate the value of ASAP. That search opened my eyes!
For review, ASAP is a formalized voluntary reporting process that permits an employee to report an observed safety hazard or a personal action/possible error. ASAP is primarily used at large maintenance organizations or airlines. However, ASAP could be implemented into a smaller maintenance organization or flight department. For most reports the employee is protected from punitive action from the company and from the FAA. Using a pre-agreed upon process the voluntary report is reviewed by a committee of three, including a representative from company management, the work force, and the FAA.
ASAP has provided companies and FAA an expanded awareness of safety hazards that otherwise would have gone unreported. For those involved with ASAP, they don’t need the big story to see the value. To get the “big story” I went to the ideal information sources; companies and workers using ASAP and to the FAA parties responsible for the program.
Ask FAA about ASAP
I started my information quest at FAA. I work there and knew it had the big picture and a lot of data. FAA’s Voluntary Safety Programs Branch (AFS 230), headed by Inspector Chris MacWhorter is responsible for the program. There are more than 250 active ASAP programs in the U.S. The participants include pilots (oldest and largest group), maintenance and engineering, cabin, and dispatch. In only four years, since October 2008, the total number of ASAP reports is about 220,000, and has been increasing by 20 percent annually. There is also a relatively new ASAP derivative used by controllers in FAA's Air Traffic Organization. By numbers alone ASAP is a success. It is obvious that the FAA numbers are important but more information was needed to show the big ASAP success story. My information search continued.
Ask industry about ASAP
There are 74 active maintenance and engineering (M&E) ASAP programs. I asked a group of M&E ASAP participants to help me tell the “big success stories.” One large air-carrier ASAP leader was slow to offer the big stories. Instead, he invited me to their bi-weekly ASAP event review committee (ERC) so that I can choose a “big story.” I said yes, expecting a meeting of one or two hours. Instead, I received a very formal information packet and a formal agenda for a five-hour meeting, with a 30-minute lunch break.
The meeting participants included the required ERC group of three people representing management, work force, and FAA. There were also representatives from corporate safety, government affairs, and quality. There were telephone participants from key hubs. The Director of Safety reinforced corporate commitment to ASAP by attending some of the meeting. The ASAP ERC meeting was a significant financial and intellectual investment in safety.
Each event was presented by a worker or management representative. All presenters had the professional demeanor and fact-based precision of a trial lawyer. There were questions and enlightened discussion from everyone in the room and on the phone. Everyone involved had maintenance credentials and experience. The group members voiced opinion about the possible intentions or actions of the employee.
In every case, there was an equal focus on the employee and on what the company could have done to prevent the event. Most importantly the group documented actions to prevent a repeat of the event. In some cases, where an employee violated company procedures and FAA regulations, there was carefully deliberated action taken. In most cases the event was “accepted” as a legitimate ASAP reportable event. In all cases, the company and the employee remediation was documented, with a deadline. Everything was recorded in a well-designed data base projected on two large screens in the room.
It became obvious to me that ASAP is not necessarily about the process or even about the “big success story.” ASAP is about well-intentioned maintenance employees, in 70 plus companies, voluntarily reporting hundreds of hazards that contribute to risk every day. ASAP is about the corporate and regulatory commitment to collect and analyze the reports and then deliberate to improve maintenance practices accordingly. ASAP is about a work culture that takes the time to report hazards, to justly consider a worker error and remediation, to improve every appropriate process, and then do it over and over again. That “big success story” turned out to be a four-letter word; ASAP. OK, it is an acronym.
The big success story is ASAP. In order to claim such a title ASAP must be comprised of hundreds-thousands of small stories. These stories show that ASAP reports helped to not only highlight a potential safety hazard but also offer high value corrective actions. Every story does not have to be a big one. Safety, after all, is insured by a long list of small actions.
An example success story
When one needs a specific success story, it is easy to find one in the databases of voluntary report systems. Nearly every ASAP report has value.
One company tells of experiences associated with installation of a tang axle washer on a particular Boeing aircraft. The washer is required on some, but not all aircraft. This situation contributes to possible confusion and installation error. It is located between the outer wheel bearing and the axle nut as shown in Figure 1. These washers come in various sizes, the most common being approximately .25-inch wide.
The washer is necessary to ensure that there are sufficient axle threads to properly tighten and torque the axle nut. Without the washer the axle runs out of threads before the wheel is properly tightened. This result is a loose wheel assembly that eventually vibrates and then wears the axle shrouds, the bearing, and the wheel. The error is discovered from either a pilot report of vibration or when a wheel shop employee finds the washer stuck to the grease of the old wheel assembly. Aside from parts, logistics, and labor there is sometimes a flight delay because of this flight line wheel assembly replacement.
Workers used ASAP to report the failure to replace the tang axle washer. The initial ASAP corrective actions centered on increased employee training and warning posters in the flight line break rooms. The posters showed the picture and explained the issue. The problem diminished but did not go away. Finally, an ASAP report suggested placing a large warning sticker on every wheel assembly destined for aircraft requiring washers. The sticker is large and obvious saying “Tang Axle Spacer Installed?”
In the eight-month period following the stickers there were no incidents of missing spacers. The problem appears to be solved. Let’s try the FAA’s return on investment process and software to calculate the return on investment. (See March 2012 Ground Support Worldwide or go to www.mxfatigue.com for more on ROI).
In the one year prior to the application of stickers the company had about 15 ASAP reports related to the washer. There were other washer events but the company chose to base the ROI on only the 15 events reported to ASAP. That is a conservative number. The estimated cost of the missing tang axle washer averaged an estimated $14,000 per event. That average includes events ranging from a quick inspection to situations requiring an axle replacement at an outstation resulting in a substitution aircraft or lengthy delay; a wide range of consequences.
Example Parts/Labor/Logistics |
$ Cost (Rounded) |
B767 Delay/hour |
$15,000.00 |
Wheel and Axle Inspection Time (2 labor hours) |
$125.00 |
Wheel Assembly Cost (exchange) |
$8,500.00 |
Axle Replacement Labor (24 labor hours) |
$1,500.00 |
Outstation repair requiring field trip with parts |
$18,500,00 |
Table 1: Example Range of Possible Costs
That includes the price of damage to wheels, bearings, axle shrouds, premature tire and wheel rework, and related logistics costs. It also estimated about $10,000 parts and labor for line replacement of the axle and wheel assembly if at a maintenance hub. For this issue the company estimated approximately four hours of flight delay during the year at an estimated $15,000/hour on a wide body aircraft ($60,000).
The cost of creating, testing, and installing stickers was about $18,000. In the eight-month post sticker period approximately there were no occurrences of the event. The annualized estimate in reduction is 15 events at an estimated savings of about $210,000. The ROI is about 10 to 1. Yes, that is a 1,000 percent return in the first year alone.
The savings attributable to ASAP reporting and the corrective action (tire sticker). This is an example of one of many success stories. Usually M&E departments do not take the time to calculate ROI and brag about every successful intervention. They are too busy tackling the next challenge. In many cases the ROI is so obvious that calculation is unnecessary as evidenced here. The company management must remain mindful that each of these small interventions results in large savings thus improvement to profits.
Success story conclusion
This big success story, therefore, is a lot of small stories. Most are documented in the corporate ASAP files. Many are released to large shared data bases like the FAA Aviation Safety Information Analysis and Sharing (ISIAS) system. Most importantly, no matter where the data ultimately resides, it is a way to find hazards that may otherwise go without proper corporate attention. Like the tang wheel washer above, ASAP and other voluntary reports are key components to ensure good data for the corporate Safety Management System, profitability to the share holders, and continuing on-time safety to the passenger.
A detailed description of ASAP is available at faa.gov/about/initiatives/asap/.
Dr. William Johnson has spent more than 30 years as senior executive and scientist for engineering companies specializing in technical training and human factors before joining FAA in 2004. He is also an aviation maintenance technician and has been a pilot for more than 45 years.
About the Author
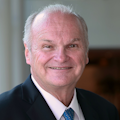
Dr. Bill Johnson
Chief Scientific and Technical Advisor Human Factors in Aviation Maintenance, FAA
““Dr. Bill” Johnson is a familiar name and face to many industry and government aviation audiences. Johnson has been an aviator for over 50 years. He is a pilot, mechanic, scientist/engineer, college professor, and senior executive during his career. That includes 16+ years as the FAA Chief Scientific and Technical Advisor for Human Factors.
Dr. Bill has delivered more than 400 Human Factors speeches and classes in over 50 countries. He has 500 + publications, videos, and other media that serve as the basis for human factors training throughout the world.
Recent significant awards include: The FAA “Charles E. Taylor Master Mechanic” (2020); The Flight Safety Foundation - Airbus “Human Factors in Aviation Safety Award” (2018), and the International Federation of Airworthiness “Sir Francis Whittle Award” (2017).
Starting in 2021 Johnson formed Drbillj.com LLC. In this new venture he continues to bring decades of human factors experience to aviators, worldwide.