Located at the Virginia Beach Airport in the Pungo section of Virginia Beach, VA, an aircraft facility sits quietly among the grass landing strip and farm land maintaining and working on some of the most unique aircraft in the world. The Fighter Factory is the restoration and maintenance facility of the Military Aviation Museum, more on this later. The Fighter Factory maintains and restores WWI, WWII, and some aircraft from the Korean War.
Some of the aircraft the Fighter Factory maintains in flying status are, Spitfire, Hurricane, Mustang, Corsair, Curtiss, Wildcat, Hawker, Fury, Peashooter, Yak,
four Polikarpovs, B-17 Flying Fortress, B-25J, Skyraider, Avenger, Sopwith, Fokker, Catalina, Dragon Rapide, and many more. With over 50 flying vintage aircraft to maintain the Fighter Factory is a very busy place!
When I visited the Fighter Factory recently one of the projects in work, was the removal and replacement of a large radial engine from one of the most successful German aircraft of WWII: the Focke-Wulf Fw190. This aircraft along with the BF109 was the backbone of the Jadwaffe. The nickname for this aircraft was the “Butcher Bird” and it had much success especially against Soviet ground troops.
The Shvetsov Asch-82t engine change
The Fw190m at the Fighter Factory was slated to get a newly overhauled Shvetsov Asch-82t powerplant from Vintage Radial located in Tehachapi, CA. This shop is an FAA certified repair station that specializes in overhaul of radial engines. The Asch-82t is a beast of an engine with 14 cylinders in a double radial construction. It is an air-cooled four-stroke aircraft engine with a blower and mechanical fuel injection system.
The ignition system has two independent ignition magnetos with one spark plug per magneto per cylinder. High voltage is accomplished by these two magnetos, attached to the front casing and they are driven by cogwheels from the propeller shaft. Electrical power is fed from the cap of the ignition timer of the magnetos to the spark plugs, shielded against humidity and mechanical damage protecting the ignition cables. The left magneto is connected to the rear spark plugs and the right magneto is connected to the front spark plugs of both rows of cylinders.
If there was an ignition problem it would not likely lead to a complete failure of the engine, since both magnetos work independently. The fuel supply to the injection pump is performed by a fuel pump located on the right side of the blower casing. The fuel injection pump is located on the rear cover of the engine which uses high pressure tubes and fuel nozzles to deliver fuel into the cylinders. This radial has 1,900 horsepower at 2,600 rpm.
Removing the old powerplant and replacing it with this newly overhauled motor takes time and educating yourself before wrenches are ever used. The point man for this project was Jeffrey May and he explained to me how he attacks a task like this.
His first step was to read all the required information he can but he also takes tons of digital pictures of the original radial installed on the aircraft. By doing this he always has points of references for this task and future jobs, he says.
Since this aircraft is a taildragger a three point sling with one point using the motor shaft for a pivot point was very helpful in keeping the engine at the correct angle for proper removal and installation. After the old radial was removed and before the new radial was installed some maintenance was performed. The oil system was purged, oil tank steamed, cleaned and flushed with solvent. Some baffling was fabricated along with a bracket to replace the overspeed governor not on the new engine.
While this maintenance was being performed another, A&P was busy prepping the new radial with spark plugs, accessories, and doing a quality inspection. After the final inspection on both the airframe and powerplant the installation process began.
Installation went smooth and once secured to the mount some additional work needed to be accomplished. The angle of the fuel pump was slightly different with this radial which led to some fuel lines being rerouted and new ones fabricated. Working on vintage aircraft and powerplants such as these takes special people, A&Ps who are willing to keep learning, not afraid of taking on new challenges, and to do the job right the first time are always needed. Removal and replacement of this radial took two technicians, three weeks, from the start to the check-out engine run.
Supporting the NextGen of A&Ps
Fighter Factory has many talented A&Ps accomplishing tasks that are very different in nature compared to most aviation jobs. They are always looking for talented people. To do their part helping upcoming A&Ps Fighter Factory in partnership with the local Part 147 technician school, the Aviation Institute of Maintenance, is starting an apprenticeship program. This program is meant to help future A&Ps get some hands on experience working in an aviation maintenance shop under the guidance of an A&P.
Staying true to the period
As mentioned before the Fighter Factory keeps one of the largest private collection of WWI, WWII and some Korean era aircraft maintained in flying status for the Military Aviation Museum also located on the Virginia Beach Airport in the Pungo section of Virginia Beach, VA.
This museum is not an ordinary static display of aircraft; it is what you would call a fully operational living aircraft museum. The aircraft are truly special but also the Military Aviation Museum stays true to the time period by building hangars and buildings that represent the architecture of the times of the aircraft.
For instance, the Fighter Factory maintenance hangar is an original design from a hangar in Waukesha County, WI, at the Waukesha County Airport in 1937. This original stone hangar was redrawn by an architect and those plans were used to build the Fighter Factory facility.
The main museum’s hangar is 60,000 square feet of art deco style that houses much of the aircraft. Other buildings being constructed are a German Luftwaffe Hangar (1936 era) from Cottbus, Germany, being reassembled on site, and a RAF Goxhill Control Tower from the Northeast coast of England was disassembled in sections and transported to the museum to also be erected at the airfield.
Throughout the year events are held at the museum such as the Flying Proms, Hangar Talk Series, Warbirds Over the Beach, SummerCamp, Biplanes and Triplanes, Proptoberfest, Trains and Planes, and many more events.
It was good to visit and learn about the Fighter Factory and the Military Aviation Museum and seeing the professionalism and dedication given to these vintage aircraft to keep them in flying condition for all to see and hear the distinctive sound of radial engines and props in the skies overhead.
More information on the Fighter Factory and the Military Aviation Museum can be found by visiting the following websites: www.fighterfactory.com and www.militaryaviationmuseum.org.
Brad Groom currently is the Director Foreign AMT Training for the Aviation Institute of Maintenance in Virginia Beach, VA. He holds an Airframe and Powerplant certificate and a Bachelor degree in technical education. He can be contacted at [email protected].
About the Author
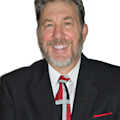
Brad Groom
Director of Education, Aviation Institute of Maintenance, Cheseapeake, VA
Brad Groom, - The Director of Education for the campus of the Aviation Institute of Maintenance (AIM) Chesapeake, Virginia. Mr. Groom has been employed with Aviation Institute of Maintenance since May, 2001. Mr. Groom has had multiple positions within the company including Instructor, Academic Coordinator, Program Coordinator, Director of Foreign AMT Training and currently, Director of Education. Groom has a Bachelor’s Degree in Education and is a FAA certified Airframe and Powerplant Mechanic. He started his aviation career in 1977 while serving in the United States Air Force as a Crew Chief, after the service, he worked depot maintenance, taught foreign nationals aviation maintenance on Peace Gate, Peace Vector, and Peace Delta programs. Other positions held were Quality Assurance for the Navy Adversary Program and Senior Instructor for Depot Management Training.