“Aviation, while not inherently unsafe is unforgiving.” This is a statement of life in our world with the aircraft of today designed to improve the man/machine interface while reducing the impact of potential hazards. The majority of reported mishaps involves weather as either the stand-alone factor or compounded with other issues.
One of the most notorious weather phenomenons is the micro-bust or wind shear. While a noted adversary to flight crews in all aspects of flight, it causes catastrophic results during critical phases such as takeoff and landing. A sudden updraft or downdraft routinely results in a rapid pitch change combined with a variation in airspeed. Strong outflow from thunderstorms causes rapid changes in the three-dimensional wind velocity just above ground level.
Initially, this outflow causes a headwind that increases airspeed, which normally causes a pilot to reduce engine power if they are unaware of the wind shear. As the aircraft passes into the region of the downdraft, the localized headwind diminishes, reducing the aircraft's airspeed, and increasing its sink rate. Then, when the aircraft passes through the other side of the downdraft, the headwind becomes a tailwind, reducing lift generated by the wings, and leaving the aircraft in a low-power, low-speed descent. This can lead to an accident if the aircraft is too low to recover before ground contact.
The frequency of scheduled airline flights provides greater opportunity for wind shear encounters. Commercial flight data illustrates pilots are faced with wind shears on average of once every 2,200 flights, and that certain wind shear “hot spots” exist.
Columbia, SC: 1 every 150 landings
Denver, CO: 1 every 2,300 landings
Dallas, TX: 1 every 7,100 landings
The question of defense against this force of nature has taken several routes. Terms such as predictive and reactive describe the different approaches to the dilemma.
As the result of the accidents in the 1970s and 1980s, most notably following the crash of Delta Air Lines Flight 191, the Federal Aviation Administration mandated that all commercial aircraft have onboard wind shear detection systems by 1993. Between 1964 and 1985, wind shear directly caused or contributed to 26 major civil transport aircraft accidents in the U.S. that led to 620 deaths and 200 injuries.
Since 1995, the number of major civil aircraft accidents caused by wind shear has dropped to approximately one every 10 years, due to the mandated onboard detection as well as the addition of Next Generation Doppler weather radar units on the ground (NEXRAD).
Predictive solutions
Predictive wind shear has taken on several forms. NEXRAD (Next-Generation Radar) is a network of 159 high-resolution Doppler weather radars operated by the National Oceanic and Atmospheric Administration (NOAA). Its technical name is WSR-88D, which stands for Weather Surveillance Radar, 1988, Doppler. The technology detects precipitation and atmospheric movement or wind. The principle uses a phase shift in transmitted versus returned signal.
This is like standing by the side of a road and when a car approaches, the sound waves compress the closer the vehicle comes and start to expand once it passes by. The returned data when processed is displayed in a mosaic map which shows patterns and movement. The radar system operates in two basic modes, selectable by the operator. The slow-scanning clear-air mode is for analyzing air movements when there is little or no activity in the area, and a precipitation mode, with a faster scan is utilized when tracking active weather.
NEXRAD has an increased emphasis on automation, including the use of algorithms and automated volume scans to enhance the accuracy of predictions. It has incorporated a number of improvements over systems previously used. The new Doppler velocity technology improves rapid air movement detection. It provides improved resolution and sensitivity, allowing detection of cold fronts, thunderstorm gust fronts, and micro-bursts. These characteristics had never been visible on previous radars. The NEXRAD also provides volumetric scans of the atmosphere allowing operators to interrogate the vertical structure of storms and provide detailed wind profiles above the radar site. The radars also had a much increased range allowing detection of weather features at much greater distances from the radar site.
Reactive systems
Pilots need 10 to 40 seconds of warning to avoid wind shear. Fewer than 10 seconds is not enough time to react, while more than 40 seconds can be too long. Atmospheric conditions can change in that time. Three technologies are currently in use to provide flight crews a one-half to five-mile advance warning of wind shear.
NEXTGEN onboard Doppler radar sends a burst of energy ahead of the aircraft to seek targets such as moisture particles. The returning signal represents the movement which is translated into wind speed. Doppler radar works better than other systems in rain but less well in dry conditions. When the transmitted signal is directed toward the ground it does return ground reflection or "clutter." However, researchers are progressing in efforts to eliminate this interference. NASA's Langley Research Center has developed signal-processing algorithms and hardware for enhancing the wind shear application.
Honeywell has introduced IntuVue which is a general weather detection system based on flight path data with constant updates of the latest hazard assessments provided on the display screen. The system also improves cockpit efficiency by virtually eliminating ground clutter via an internal terrain database which also automatically corrects for the earth’s curvature, to ensure the clearest, most accurate view of the weather ahead.
As the first system certified to the FAA’s Minimum Operational Performance Standard (MOPS) for enhanced turbulence detection, pilots will be informed of air turbulence and have the ability to make safer, more informed route decisions. This advanced protection has demonstrated a more than 45 percent reduction in turbulence related incidents.
Wind shear detection and alerting systems compare inertial accelerations with air data information to provide a wind shear encountered warning. By utilizing angle of attack and flight path angle instead of pitch angle in the calculation, the system will be responsive to vertical as well as horizontal shear conditions. An enhanced version of the system is also compensated for roll with the angle being derived from the rate of change of heading. The alerting system is capable of providing visual and aural warnings for a variety of wind shear conditions, such as, head shear, tail shear, head shear followed by tail shear and wind shear trend. The warning system is also capable of providing a wind shear warning which is a function of the radio altitude of the aircraft.
Enhanced ground proximity warning systems (EGPWS) frequently have the ability to sense and alert flight crews to a wind shear event. Knowing local terrain information coupled with radio altitude and vertical navigation enabled rapid and accurate recognition of vertical micro-bursts. Like most systems incorporating digital technology, built-in diagnostics will alert flight crews and maintenance personnel in the event of system degradation or failure.
Advisory Circular 120-41 is available at the FAA.gov web site and provides criteria for the design of wind shear detection systems which includes wind tables and relative elevations.
In short, the one major difference between reactive and predictive wind shear systems: the normal procedure for a reactive alert is an execution of an escape maneuver while an advance warning will enable the crew to initiate an orderly change of the flight path.
Technology does provide several means for contending with microburst but the most basic rule for wind shear avoidance is “Takeoffs are optional. Landings are mandatory.”
Jim Sparks has been in aviation for 30 years and is a licensed A&P. He is the manager of aviation maintenance for a private company. He can be reached at [email protected].
About the Author
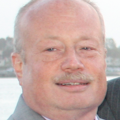
Jim Sparks
Jim Sparks has been maintaining aircraft for almost 40 years with the majority of the time involving Business Aviation activities. Jim’s endeavors have placed him on six of the seven continents contending with numerous situations from routine flight dispatch to critical AOGs. His career includes maintainer, avionics/electrician, educator, tech rep, and director of aircraft maintenance. In addition to other activities he is engaged with ASTM assisting in the global development of criteria defining the Next Tech for NEXTGEN. You can reach him at [email protected].