We hear it every day: "They did not follow procedures."
As a result, an aircraft is damaged ... someone is injured ... the baggage is lost ... the flight is delayed. The outcome is varied and infinite, but the overriding cause is that a procedure was not followed. The challenge is as old as aviation and the solutions seem to be elusive. Or are they?
A panel of aviation industry and government officials recently spent two days trying to get their hands and heads around the issue of following procedures. Much of the first meeting was on maintenance procedures, but it could have just as easily been on in-flight, ground service or flight deck procedures.
The invited group was composed of OEMs (such as Boeing, Airbus, Gulfstream, and General Electric), airline and independent maintenance organizations, FAA inspectors, CEOs and organized labor leaders. Industry professionals from airlines, general aviation, rotorcraft, corporate and regulatory all agreed that we have a problem. Or make that problems.
Today, safety management approaches these problems not by merely looking for who or what to blame. Instead, proper safety management identifies and corrects the hazards that contributed to the risk. When it comes to following procedures, however, that may be easier said than done.
The workshop participants decided that the word "documentation" is too limiting. The focus must be on "information." It can range from traditional written text to graphics to animations and more.
Carol Daniels, CEO of Aircraft Technical Publishers and chairman of the General Aviation Manufacturers Association emphasized that "information must be delivered in a useable format, at the right time, on the appropriate device."
According to Daniels: "Users should specify their information requirements. What works for an airline on the Atlanta ramp may not be suitable for a helicopter operator in Alaska. If we do our job right, mechanics are more likely to access the information."
John Goglia, former National Safety Transportation Board member and long-time airline mechanic talked about the culture that heralds safety as "No.1," but then drives decisions, actions and rewards with on-time performance.
According to Goglia: "When a crew is rewarded for meeting the schedule rather than for reading the instructions, the technical information availability and access lose priority."
Many of the FAA inspectors lamented the fact that they are forced to take administrative action against individual mechanics who fail to use the technical documentation. Theses inspectors were once mechanics themselves so they know that the individual is faced with inadequate documentation systems in a "hurry-up" culture. The mechanics are often victims of documentation, corporate culture and uncompromising FAA regulations.
The workshop broke into five working groups that focused on quantifying the challenges and possible solutions in particular areas. From a straightforward view these groups looked at the user, the documents and the event data.
A quick look at the top challenges and summary solutions from each of the five groups reveals a number of actionable items.
Human Issues
The group identified a lack of involvement by mechanics to create and validate written procedures. The members suggested the OEMs and the airline engineers who write work cards must do more field-testing of the written procedures. The OEMs and airline engineers must also streamline the process to modify poor procedures identified by on-the-job users. Either this must improve or mechanics will continue to bypass or ignore procedures.
Information Quality
With representation by OEMs, airlines and government, this group said the greatest challenge was the government's inconsistency and nonstandardized requirements. The members called for new federal aviation regulations and internal training that is matched to current technologies and user requirements. Government acknowledged that they are traditionally understaffed in the offices that oversee technical documentation.
Industry Responsibility and Measurement
While Industry Responsibility and Measurement are two separate groups, the members were like-minded in their conclusion. According to both groups, there is not a sufficient business case to improve the technical information. In the trade-offs among production, quality, and compliance, the technical information is seldom top priority. The solution is to provide additional detailed error data when "failure to follow instructions" is the cause of a loss. Additional information-related root cause analysis is necessary.
Regulatory
The group said the top issue is the inconsistent communication of expectations regarding technical information. The solution must emerge with new regulations and guidance materials. Such materials must be created in concert with industry groups. The members believed there must be increasing reliance on industry toward a process of internal validation and acceptance of information systems.
Perhaps the best finding of the workshop was the unanimous agreement that current technical information must evolve to today's working environment. There are many modern solutions to ensure that proper application of technical information can contribute to ongoing safety, increased work efficiency and enhanced job satisfaction.
Stay tuned for upcoming articles that will examine proposed solutions and show you how to be a big part of the technical information solution.
Dr. William Johnson has spent more than 30 years as senior executive and scientist for engineering companies specializing in technical training and human factors before joining FAA in 2004. He is also an aviation maintenance technician and has been a pilot for more than 45 years.
About the Author
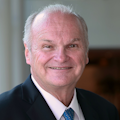
Dr. Bill Johnson
Chief Scientific and Technical Advisor Human Factors in Aviation Maintenance, FAA
““Dr. Bill” Johnson is a familiar name and face to many industry and government aviation audiences. Johnson has been an aviator for over 50 years. He is a pilot, mechanic, scientist/engineer, college professor, and senior executive during his career. That includes 16+ years as the FAA Chief Scientific and Technical Advisor for Human Factors.
Dr. Bill has delivered more than 400 Human Factors speeches and classes in over 50 countries. He has 500 + publications, videos, and other media that serve as the basis for human factors training throughout the world.
Recent significant awards include: The FAA “Charles E. Taylor Master Mechanic” (2020); The Flight Safety Foundation - Airbus “Human Factors in Aviation Safety Award” (2018), and the International Federation of Airworthiness “Sir Francis Whittle Award” (2017).
Starting in 2021 Johnson formed Drbillj.com LLC. In this new venture he continues to bring decades of human factors experience to aviators, worldwide.