Recip Technology: What About Those Diesels? Part 1
Diesels were there first
Diesels (compression-ignition piston engines) are among the earliest players in internal combustion, yet they win at LeMans, the premier 24-hour auto race. They are effective in sizes from tiny car use – maybe 30 cubic inches – to the oceangoing container ships that boast bores and strokes of one by 1.5 meters. They power about half of Europe’s cars, most trains, virtually all the world’s heavy long-haul trucking and ocean freight shipping, and … hardly any airplanes. What’s up with that?
Rudolph Diesel’s first practical engine was built in 1897 and weighed 9,000 pounds; it produced 18 reliable horsepower. By 2008, the South Koreans built diesels that make 115,000 horsepower -- at 88 rpm. (All the supergiant oceangoing diesel engines are today built in South Korea, by Hyundai or MAN.)
Diesels deliver horses
Efficiency, too, is a trademark, and comes with high reliability. Without spark ignition, entire systems of spark generation and management are eliminated, but diesels can be hard to start, typically requiring “glow plugs” until the engine runs on its own.
Boosted intake air and fuel injection are required; a carburetor can’t force the fuel/air mix into a pressurized cylinder. Sturdy components are required: pistons, cylinders, heads, connecting rods, and their crankshafts – all must be larger, heavier, and stronger than gasoline engines require.
High pressures generate a lot of heat. In today’s high-efficiency diesels, which operate near 50 percent efficiency (two-stroke diesels are a couple points higher; four-strokers are a couple points lower), the exhaust gas carries off about 54 percent of the wasted energy; the cooling system (air or water) takes care of nearly 40 percent; the oil cooler handles about 6 percent. This screams for exhaust-powered performance-enhancers, otherwise known as turbochargers.
Allan Lockheed, who consults on high-performance engine designs, notes, “It did not take too long before [piston-engine] designers realized that turbochargers were the real power-makers, so they developed better and better ways to drive the turbochargers, until they finally got rid of the piston engine altogether, and made the turboprop, which is basically a sophisticated, self-powered turbocharger with a gearbox.”
Still, diesel operation is intrinsically simpler than spark-ignition operation. Diesels need no controls, sensors, and circuits for making sparks, and there is no requirement for ignition electric power when running. A glow plug circuit for starting is not a big engineering challenge. A diesel’s power is controlled, not by a throttle on its air supply, but by the amount of fuel it receives. Therefore, a diesel with a functioning fuel-delivery system will not over-rev, a welcome “safety valve” in the case of, say, a runaway prop. The “fuel injection vs. carburetion” debate will not be resolved here, but the general advantage of fuel injection is well-accepted, and all diesels are fuel-injected.
Diesels, relying as they do on compression for ignition, necessarily run high compression ratios. The stronger components needed to run 20:1 and up all day long weigh more than their typical gasoline/spark-engine counterparts. Heavier crankshafts, rods, and pistons are expected. Not always anticipated are heavier valves and seats, valve springs, cylinders, heads, and engine cases. Also because the compression is higher and efficiency is greater, diesel power pulses are sharper and more powerful. These nastier pulses have fragged many an unsuspecting propeller and cracked unspecialized motor mounts, exhaust systems, and anything else that attaches to the engine, including starters, alternators, and intake components. The easiest response to all this destruction has been to add weight; but aero-designers at least are aware of the reduced usefulness added weight brings to an aircraft, and many novel approaches have been brought about to obviate the snappiness of diesel pulses.
Adding weight surely does that, but represents the least elegant solution. More-typical expediencies include incorporation of clutches or slipper washers in the drive system (sometimes in conjunction with a gearbox, which can also be tuned), experimentation with firing order, and more-sophisticated control of ignition and burn rates within the combustion chamber.
Additional work has been done with materials – some are quite good at changing the harmonics, but cost a bundle. (Anyone seen titanium engine cases lately?) Lower-cost manufacturing sometimes involves higher-cost materials or processes and smaller or less-complicated parts.
As engine designers work through this calculus, we sit on the sidelines and ask,
“When can I have one?”
Several attempts have been made, and some have met a degree of success.
There are a lot of factors behind this: necessity is one. For almost as long as I can remember, we have heard of the imminent demise of avgas. Like the preacher who predicted the end of the world six times already, the doomsayers shout even louder: “This time, we really mean it!” And this time, they’re probably right, at least about leaded avgas.
Unleaded gas, the readily-available alternative, is commonplace in cars, but cars don’t need 100 percent power settings for every takeoff, or 75 percent power settings for most of their lives. Worse for mogas in aviation is the ever-changing blending of different auto fuels and the inclusion of hygroscopic (water-seeking) Ethanol in the mix. Auto gas, because of its inconsistency, changing formulations (usually dictated by unpredictable bureaucracies), uncertain storage and transportation, and lowered power content, does not offer a promising alternative to avgas. Additionally, the lack of lead in unleaded gasoline may pose problems for some engines’ internals.
Aviation diesel fuel, commonly known as Jet-A, is regulated, relatively consistent, and of high power content. (Jet fuel contains more Btus per pound – more available energy – than even the best gasoline.) An engine built to use Jet-A will deliver more-consistent results, crucial in aviation. Further, jet fuel, because of the enormous demand, will be around for decades.
Not long ago, Jet-A was considerably less-expensive than avgas in the U.S., and that difference fueled a lot of interest in the black-smokers; but the relative prices have recently closed or inverted. Relative fuel costs are no longer significant.
Diesel engines are more-efficient than gasoline engines: they convert more of the available energy into useful energy; and they use a more-powerful fuel. It stands to reason that diesels should be better at power production. As a byproduct of their thermal efficiency, they also emit less of many undesirable compounds into the air. Although we all are familiar with diesel smoke, “aroma,” and soot (as accumulates in exhaust pipes), these byproducts are considered less-harmful than many of the invisible pollutants produced by gasoline engines.
Still, it is the power to weight ratio of the full system that matters in aviation. Diesel advocates often talk about fuel burn in “gallons per hour,” knowing that diesel fuel is roughly 19 percent heavier than avgas. (This has implications for the airframer, too: what are the overall weight impacts on structure and payload? Are there possible CG effects in adding weight to fuel tanks?) Note, too, that there are significant differences in thermal expansion between gasoline and diesel. So, to get a more-valid comparison, think “pounds per hour” on fuel burn, but accommodate the weight difference and temperature/volume effects.
Where’s the progress to be made?
Diesel technology in aviation is still in its infancy, while gasoline aero-engines are well-developed. There is simply more progress yet to be made in innovating with aero-diesels. Past achievements in gasoline engine technology actually work against innovation and further development in gas engines. Since improvements in gas engines will likely be small, there is less incentive to pursue them. Diesels face the opposite prospect: innovations will be rewarded by their use on large numbers of engines.
In the concluding episode, we’ll look at current and near-future aero-diesel technology.
Tim Kern is an aviation writer, aircraft builder, and private pilot. He is based in Anderson, IN, and can be reached at [email protected]
About the Author
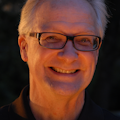
Tim Kern
Tim Kern is an aviation writer, aircraft builder, and private pilot. He is based in Anderson, IN, and can be reached at [email protected].
Tim Kern, CAM, MBA, has written for over 50 aviation publications, and is a consultant for a variety of companies; www.timkern.com.