You look at the work order and sigh … change aileron control cables. You envision eye strain and poked fingers, reaching into nearly impossible places, past wiring and through inspection holes.
“Oh, just get it over with,” you think. You’ve done it before and know the tricks of the trade. You look at the cable end points, check the routing, and determine what you’ll need to do to pull the new cable through using the old cable. Conceptually simple; in practice, considerably harder. Especially with longer runs through several pulleys and long stretches of wingspan.
The technical data and maintenance manuals aren’t a lot of help. They seem to almost always say, “Cable Replacement: Change cable.” Sometimes they’ll do a little more than that and sometimes they say nothing at all. In some table of the flight control chapter or at the back of the book, you’ll find cable tension data. You’ll likely find cable inspection criteria and maybe a word or two on rigging. But cable changes are so “obvious” they don’t really seem to matter to the OEM.
Check routing before proceeding
This isn’t meant to be a lengthy discussion on cable changes. It is a warning against being lackadaisical about cable changes … especially in hidden areas where it’s hard to verify the routing. In being lackadaisical, a person assumes everything went well without the verification step.
An excellent example appeared lately on one of our Lear 35s. The aileron interconnect cable, between the pilot and co-pilot control wheels, was due a time change and the mechanic detached the old cable at one end and attached it to the new cable for the pull from one side to the other. About halfway through the exercise, the cables became jammed. They would pull backwards and forwards until the joint between the two reached about halfway.
Using a flexible borescope, the mechanic followed the cable routing between the two control columns and learned two things. 1) He figured out what was causing the problem and 2) he learned there is an almost-impossible-to-see-without-a-borescope pass-through hole drilled in a web within the control column assembly frame.
This should adequately illustrate the importance of checking the cable routing during control cable changes. Subsequent inspections have been conducted on a number of Lears and this condition was found in about 25 percent of those inspected.
About the Author
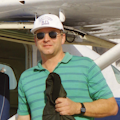
Clint Lowe
Clint Lowe holds an FAA Airframe and Powerplant certificate with Inspection Authorization and a Commercial Pilot certificate with instrument and multi engine ratings. Clint has spent most of his aviation career with the United States Air Force and Air National Guard in a variety of roles including maintenance, safety, training, oversight, and accident investigation. He has owned and maintained several aircraft and had a Part 135 air freight business for several years running bank checks. In 2007 he received the Maintenance Group Senior NCO of the Year Award. He currently is a Quality Assurance Inspector/Quality Assurance Representative with the North Dakota Air National Guard in Fargo, ND.