Turbine Technology: The Small Turbine Engine Test Cell
Rolls-Royce has a couple new test cells, the result of the determination of such a need in 2007. By 2009, the first had been delivered; both are now on-line and in daily use. The test cells don’t house your standard dynamometers. They’re unusual in several respects, all of them good.
The demand for its small (Rolls-Royce M250 core) engines, many used in helicopter applications, was growing, and Rolls-Royce needed additional new dynos (its legacy equipment is still fully functional and is used regularly) to speed testing and throughput.
The company wanted to cover several bases with the new dynos: disaster recovery was one such consideration; being as “green” as possible was another; and of course the functionality of the test cells was paramount: quick turnaround, minimal maintenance, state-of-the-art telemetry and data logging, engine-configuration flexibility, and accessibility were all important.
Modular construction
Taking these into consideration, Rolls-Royce became the first customer for a new dyno system from a Texas company, Atec. That company’s release (in February 2007) said, “This project marks the launch of Atec’s Phoenix Series modular test facilities, a containerized test cell enclosure which can be fully equipped with all engine support systems – load absorption, fuel, air, oil and fire suppression … Atec has developed an innovative dynamometer system using an electric regenerative dynamometer. This dynamometer is a cleaner alternative than traditional systems, and it offers full range power absorption without the need of a gearbox, in most applications.” The system, says Atec, provided “… all the functionality of a traditional engine test cell with the benefits of [modular construction].”
The system was tailored for use in the Rolls-Royce Indianapolis, IN, facility. Being of modular construction, the Rolls-Royce test cell sits on its own platform, the backbone of which is made up of 24-inch I-beams. This offers some insulation from rare possibilities – earthquakes and most imaginable floods – and maintains the module’s independence – should a need arise to reposition it, the entire building can be moved with relative ease. “We have no plans to do that,” says Paul Bushue, manufacturing and test engineer. “But we have the capability if we ever need it. These modules enhance our manufacturing campus by being lean and flexible.”
Eco-friendly
As for being “green,” well, running turbine engines at high loads for sometimes days on end doesn’t seem all that eco-friendly, even though no one disputes the necessity of running these engines for certification, testing, and routine quality assurance. Standard dynamometers use a water or air brake, where the medium absorbs (and wastes) the power generated by the engine. The new Rolls-Royce dynos use a pair of Schorch 500-hp-rated electric motor/generators controlled by a Parker SSD drive system to provide a precisely measurable load, and the electricity generated by the tests is fed back to the power grid, through an arrangement with the local utility. Rolls-Royce estimates it saves about a thousand dollars a month by selling its generated power back to the utility; and as throughput rises, of course the savings will follow.
Test cell operations
Interesting and important as those qualities are, the daily operational function of the cells is the paramount priority. Accuracy, safety, and throughput are the keywords in production-engine testing, and the new Atec dynos deliver.
Using a Rolls-Royce proprietary data collection system (internally called UMACS – universal monitor and control system), much of the test cycling is automated, although the cells are currently manned; repeatability is assured, and data are more robust. Both hydromechanical control and full authority digital engine control (FADEC) system engines are accommodated on either test cell, and the data collection covers the usual operational parameters – engine and gearbox oil temps and pressures, ambient air temp, inlet and exhaust temperatures – and development and engineering parameters, as well. (For example, various vibration points are monitored, through a highly configurable set of additional sensors.)
Four different engine test cycles that simulate typical light helicopter missions can run automatically: executive transport, standard training, autorotation training, and chase/police/news. Additionally, production/overhaul acceptance certification test cycles can run automatically, all the way to 24/7 “continuous life” tests, with stops for only those maintenance items called for in the manuals.
“The goal is to be able to run all the standard test cycles automatically,” says Nathan Heidegger, assistant chief project engineer. “It’s just that much more repeatable, test to test. Plus, when you’re running extended endurance tests, you really don’t want to tie up an engineer and test stand operator to just sit here and watch the engine run all day.” The data collection is real-time, in the cell’s control room. It is also remotely viewable at engineers’ stations.
Still, the engineer on call can get … a call from the system. When the systems spot an anomaly in an operating parameter, any of several events take place: a minor deviation may simply trigger an alert on screen; a larger deviation may command a reduction in power; or a calamitous event may signal immediate shutdown. (The actual parameters are Rolls-Royce proprietary, but you get the idea.)
Three gimbal-mounted, variable focal length (zoomable) cameras record the operations: two are in the dyno room itself, providing a good look at the overall operation and a close look at the power coupling indoors; the third camera keeps an eye on the exhaust stack outside. Any or all camera views are seen and controlled by the test crew.
Test cell throughput enhancements come from several improvements: the cell itself is easily configurable to fit any of the small R-R engines – M250 and RR300 (and, eventually RR500); turboprop or turboshaft; exhaust up or exhaust down. The test operating rpm range extends from 2,000 to 10,000, covering the small-engine line quite well. Different mounts switch quickly, and most hookups are generic. Additional sensors get added when they’re called for.
Throughput is greatly enhanced by the two-cell setup. With their doors literally across the hall from each other, test mechanics can easily move between cells; tools are common and available. Subject engines roll up a ramp (the cells are elevated, remember?) and are fitted with sensor-equipped intakes and exhausts, plus other goodies that may be required for their particular tests. Then, as soon as a cell opens up, the new engine is wheeled in, picked up by a wall-mounted crane, and positioned in its bed, where the fuel lines, controls, and sensors are attached. Then the exhaust duct is lowered into place by an electric hoist. Push the button, and … power!
Paul Bushue says that the existing stands, in service for decades in the main building, still get plenty of work, but that the new stands, with all their improvements in capacity, precision, real-time reporting, datalogging, and automation “have taught me more about how our engines run. This actually helps me better translate information from the older stands.” In other words, learning from one machine makes the other machines’ data more relevant – a free improvement in old equipment!
Tim Kern is an aviation writer, aircraft builder, and private pilot. He is based in Anderson, IN, and can be reached at [email protected].
Atec Test Cell at Rolls-Royce
In a product as sophisticated as a test cell, there are no off-the-shelf units. The basic design is planned to be as useful and adaptable as possible; then the individual customer’s requirements are added, and the result is a tailored unit that exactly meets the customer’s needs.
Howard Lederer, the chairman and CEO of Atec, notes that, “You’re dealing with many different departments, programs, and people. It’s sometimes difficult to get a consensus. Everyone is not simultaneously available to discuss every question – and some questions never do get answered in the planning, or even the initial design stages. But finally, as you build it, someone fills in the remaining blanks.” Of course, “As new requirements roll in and the design changes, costs go up. That can get a little tough for customers, but professionals understand the process. We learn from every customer; that eventually makes it easier for everyone.”
Atec’s small test cells are making a splash across industry, but it also makes big ones. “Currently, we’re working on a cell to accommodate JT9s and CF6s,” Lederer continues. “We have a design and a process that we’re pretty proud of; it costs about half what a traditional cell of that size would cost.” Perhaps we’ll see more on that, later. Visit: http://www.atec.com/.
About the Author
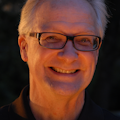
Tim Kern
Tim Kern is an aviation writer, aircraft builder, and private pilot. He is based in Anderson, IN, and can be reached at [email protected].
Tim Kern, CAM, MBA, has written for over 50 aviation publications, and is a consultant for a variety of companies; www.timkern.com.