Quality Management Systems: What they can mean to your company and to you
Management has announced a new quality initiative. So what does it mean? Is it this month's theory for success or is there long-term management support behind it? Let's take a look at several quality management systems and what they can mean for a company and its employees.
The philosophy behind quality systems takes many turns but the emphasis is on the customer. A satisfied customer is a returning customer and companies profit from satisfied customers.
The Japanese are credited with introducing quality systems such as just in time and kaizen to manufacturing companies. And Japanese companies like Toyota are still seen as leaders in continuous improvement programs. Many programs and associations were created during the 1940s to make North American companies competitive in the marketplace. And with the condition of today's economy, the advantages of implementing a quality program could save jobs if not companies as a whole.
Here are descriptions of some of the most common quality initiatives.
Just-in-time (JIT)
Just-in-time is an inventory control program. Working closely with suppliers, manufacturers indicate how many and how often they need components or parts to keep up with the manufacturing or assembly line. This system requires communication and trust that quality parts will be delivered when needed. This system frees up space that previously was stacked with components, allowing streamlining of the actual manufacturing lines and plants, and reducing the costs of storing inventory as companies only pay for components as they need them. The relationship with suppliers is an important one as your livelihood is dependent on an outside source. In developing JIT systems, there is often an evaluation or certification process to ensure suppliers are able to meet a company's needs in terms of quality, price, and delivery.
Kanban
Kanban is a quality system that depends on visual flags, typically cards or containers, to move parts from one workstation to another. While the basis is JIT, it goes further by changing the system from a push to a pull process. New parts are only introduced into the system when a flag indicates that more are needed. Advantages of kanban include lowering costs, quick response, minimizing waste, avoiding overproduction, and delegating responsibility to line workers.
Besides inventory control, kanban also incorporates re-engineering. It creates a modular/cell production flow. Layout of processes and machines are streamlined to reduce duplication and encourage the best flow of employees and materials. So, for example, you don't have to walk across the plant to get a part or a tool, it'll be right next to you when you need it. A U-shaped processing flow-line instead of one that is in the form of a straight line allows for minimal travel time through the various processes, increases supply accessibility, and often minimizes the overall space requirements opening up space for other processes or projects.
Kanban also places emphasis on the team and the individuals that make up the team. Team members have input through concepts like quality circles where problems are discussed and solved within the team's boundaries. This framework puts more emphasis on the team, the level that usually is closest to the problem, instead of relying on supervisors and quality control inspectors. Quality is seen as part of the process instead of an afterthought or as being removed from the process.
Continuous improvement
Kaizen is the Japanese term for continuous improvement. It is a scientific method and a framework of values and beliefs that keep the focus on quality. The kaizen cycle includes a plan to change whatever needs to be improved, carrying out changes on a small scale, observing the results, and then evaluating the results and the process to determine what has been learned so it can be used or improved for the next cycle.
These theories and practices have been modified and expanded into various quality improvement systems such as lean manufacturing, Six Sigma, the Malcolm Baldrige National Quality Award, and ISO 9000 certification standards.
Lean manufacturing focuses on speed, elimination of waste, standardization, and responsiveness. This can lead to getting products to market faster (planes delivered sooner) or redesigning a product to meet market needs and satisfying the customer.
Six Sigma is a data-driven methodology developed by Motorola that strives for perfection. It examines variations and root causes of current performance with a focus on all business processes. There is a logical progression for making improvements to a company's product or internal processes.
Goodrich has been implementing lean practices since 1996, but is gearing up for a program that will marry lean and Six Sigma practices together. According to Sam Lee, training coordinator, it will start with a training program for management and then eight hours of training will be given to each employee at all Goodrich facilities.
Currently Goodrich conducts kaizen events that look at processes by documenting reality, what you're doing today, either by written descriptions or by videotaping a work process. Then according to Lee, "the team meets to look at the whole process, and asks where can we remove waste. They'll go through every single process and ask how can we improve the amount of time it takes to accomplish a task. When the team agrees on the changes, they'll write up a standard as a process and it'll be put on a standard work combination sheet. This shows the process, the time, and the travel of the operator. Then that becomes the new work process that goes out on the floor for everyone to follow. People come up with ideas, then they'll look at it again and rewrite the work process. Anyone on the team can make a suggestion on how to remove waste and improve the process."
Awards and associations
Besides companies adopting quality practices, associations and government programs have been created to foster quality programs. The Malcolm Baldrige Award was created by law in 1987 to stimulate American companies to improve quality and productivity, recognizing companies' achievements, providing an example to others, and establishing guidelines for companies and organizations to follow to achieve higher quality.
The International Organization for Standardization (ISO) was created in 1947 to facilitate the international coordination and unification of industrial standards. The standards provide worldwide compatibility and assurances of quality, safety, and reliability.
Other societies and associations focused on quality include the American Society for Quality (ASQ) and the Association for Manufacturing Excellence (AME). Both offer training and seminars that emphasize quality management systems and philosophies often showcasing what different companies have accomplished after implementing quality programs.
Company achievements
So what have companies accomplished after incorporating quality systems? One example is Cirrus Design, a company based in Duluth, Minnesota, that manufactures airplanes. It was able to reduce the time it takes to design, manufacture, and test an airplane design from years to months with the introduction of its Centennial SR22. Incorporating the 100 years of aviation, the new model was introduced at EAA this year. The speed and flexibility that result from following quality practices can create new market niches and increase companies' bottom lines, a necessity in today's climate.
For programs to become more than just the flavor of the month there needs to be support from management to sustain the program, training so that goals and tools are known throughout the company, and communication so that successes (and failures) can be incorporated (or avoided) into future plans.
Such is the case with Pratt & Whitney Canada's Achieving Competitive Excellence (ACE) methodology. The ACE™ system was developed by United Technologies Corp., parent company of Pratt & Whitney, Sikorsky Helicopter, Hamilton Sundstrand, and other companies outside of the aviation field. ACE incorporates lean manufacturing and Six Sigma tools into a sustainable continuous improvement system.
The ACE philosophy is designed to identify and solve problems, improve processes, make strategic decisions through repeated applications of the program's tools, and create positive change.
According to Dominique Dallaire, director of ACE, "ACE, which stands for Achieving Competitive Excellence, was launched in 1996. It's three pillars: one, a philosophy of continuous improvement in a competitive market; two, a day-to-day operating system with a toolbox including various continuous improvement operating tools; and the third pillar is having competent, efficient people using ACE tools and methodology to achieve better business metrics.
"There is the ACE protocol," Dallaire says, "which guides every work group into a logical progression and implementation of the ACE continuous improvement tools. It's a journey where you start with a work group whether in the office or the plant and progressively apply the ACE tools to that group's activities. One of the main problems companies have today is there are many tools on the market, but there is nothing that brings all the tools together in a logical sequence. The protocol removes the flavor of the month effect of most programs. With the ACE process, tools will come in and out of the process and help it move from one level to the next."
The ACE protocol features four levels, Qualifying, Bronze, Silver, and Gold. Each level is more demanding than the previous one and is a mixture of short-term and long-term improvements or achievements. The Qualifying level is the baseline for becoming aware of the program and the tools that are available. Bronze involves more advanced training, requires 60 percent involvement of the cell or team, and full application of ACE tools to some key processes. Tools include such items as 5S (see sidebar), total productive maintenance, setup reduction, root cause corrective action, mistake proofing, market feedback analysis, and leadtime reduction. The Silver level requires actual customer satisfaction and business performance improvement, documentation and streamlining of all key processes, definition of employee satisfaction, and 80 percent organizational involvement. Gold represents best in class performance and requires 100 percent team/cell involvement.
Besides achieving company goals in the areas of equipment downtime, quality products, cost reductions, and growth, P&WC has also been able to develop a new product through the ACE program. It has made ACE available to other companies through licensing agreements and training and coaching support.
ACE tools
Among the tools available in the ACE program are the 5S. They are:
Sort: Eliminate what is not needed
Straighten: Organize what remains
Shine: Clean work area
Standardize: Keep simple, standardize
Sustain: Make 5S a culture
Benchmarking
An important part of quality management systems is to see what somebody else has done. Comparing your systems to someone else's gives you a new perspective. You can determine areas where you need improvement or where you are doing OK. This was the case at Pratt & Whitney Canada. Companies were visiting the company to see how P&WC was achieving its goals, and that led to sharing ACE concepts with others. Companies observed P&WC's methodology, and tried to return to their own companies to implement it. They discovered they couldn't do it by themselves; they needed the experience and support of P&WC.
As a result, P&WC has increased its marketing efforts in regard to the ACE program. Companies licensing the program include Alcan Aluminum, Bell Helicopter Textron, Ethiopia Airlines, and Camoplast Inc. While the idea is to make companies autonomous in how they conduct their own ACE program, P&WC's door is always open if additional training is needed.
Goodrich also conducts benchmarking, and has gone to other facilities to see what others are doing. "And it's a requirement for management within Goodrich," Lee says, "to travel to another Goodrich facility for one week each year to participate in kaizen events and to see the different kaizen practices." As a result, new ideas can be shared across the company as a whole.
Team focus
For quality initiatives to be successful, there needs to be employee buy-in. The establishment of cells or teams allows this to happen. As Jim Wilson, manager of external ACE activities for P&WC, explains, "ACE is a bottoms up approach." In moving the implementation to the cell level, employees can see the influence they have on what gets changed, and are more receptive to more and more demanding changes. If change comes from the top there is usually more resistance as there is less input from the individual or cell level.
Team involvement also means team rewards. Some companies reward teams monetarily with a bonus for meeting goals or with a share of the company's profits, some provide flexibility by allowing teams to chose their own hours. The ACE program uses personal involvement by senior management along with plaques located by each cell and polo shirts for the entire cell with the ACE level achieved for recognition throughout the company. By year end P&WC will have about 20 cells at the Gold level out of 300 cells, according to Dallaire.
Some programs like ACE also rely on pride and peer pressure to meet goals. The pressure to move to the next level is high and no one wants to be responsible for not getting there. This can positively influence turnover rates and attendance statistics.
What it can mean to you
If you're part of a company that successfully implements quality management systems, there are many positive aspects. The first is the change in the company culture, you feel part of the team and you can take pride in contributing to the success of your team and your company. Your work day is more satisfying as there is less rework, as systems have been put in place to ensure it is done right the first time, so you can get more accomplished. And it's also reassuring to know that improvements can ensure the profitability of your company so you have a place to work.
Association for Manufacturing Excellence (AME)
www.ame.org
Cirrus Design
www.cirrusdesign.com
Goodrich
www.goodrich.com
International Organization for Standardzation (ISO)
www.iso.ch
Pratt & Whitney Canada
Achieving Competitive Excellence (ACE)
http://ace.pwc.ca
About the Author
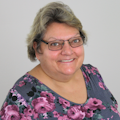