WX system will transmit microwave energy
By Jim Sparks
Microwave energy is a term that often instills fear in the mind of aviation personnel. After all many of us have seen the result of placing a bratwurst in the microwave oven. The effects of these unseen forces can be startling as you watch what you thought was lunch proceed to explode. When working around weather radar I often contemplate the ill fate of my brat prior to approaching the energy emitting area.
Even though radar systems manufactured in recent years use only a fraction of the power of their predecessors caution is warranted. U.S. Federal Aviation Administration Advisory Circular 20-68B addresses radiation safety precautions for ground operation of weather radar systems.
The prime mission of airborne weather radar is the detection, processing, and display of weather phenomena with the objective of generating advance warning of potentially threatening weather. A typical state-of-the-art Doppler radar is capable of providing real-time surveillance and advance warning of potentially severe weather systems and definitely contributes to the safety and well-being of all people who fly.
"Radar" is an abbreviated term for "radio detecting and ranging" and the principle involves the transmission of a burst of
energy followed by monitoring for a reflection.
This echo occurs when something such as precipitation is in the direct
path of the transmitted signal. The velocity of the transmission is known so the time lapse until the echo is detected will directly relate to the distance the signal traveled. This calculation is used to interpret the distance to the target. By using a narrow beam width coupled with an antenna capable of sweeping an arc in front of the aircraft an accurate location of hazardous conditions can be portrayed to the flight crew. It was in the 1950s that commercial aircraft began to depend on onboard weather detecting systems and the system has been evolving ever since.
Radar systems are widely used throughout aviation and can detect various types of precipitation, turbulence, and even wind shear. Some units can detect other aircraft. This can all be accomplished using a Doppler X-Band (9,300-9,500 MHz) transmitter with a nominal output of microwave power. There are five frequency ranges that have been used for radar and they include "L band" 1,000-2,000 MHz, "S band" 2,000-4,000 MHz, "C band" 4,000-8,000 MHz, "X band" 8,000-12,500 MHz, and "K band" 18-26.5 GHz.
Radar may also be used as a stand-alone navigation system and can map the terrain below the aircraft. System components may include a flight
deck display that may be dedicated to weather information or can even be part of the electronic flight instrument system (EFIS), a receiver transmitter (R/T), and an antenna. In many modern systems the R/T and antenna are included in one device. In systems where the R/T and antenna are separated, a device called a Wave-Guide provides the connection between the two units. A weather controller is also either part of the radar display or can be separate and in many cases there may be a controller for each pilot.
Since the introduction of weather radar in aviation two designs have been used and in either case energy pulses are generated and then radiated by an antenna. The presence of an obstacle such as precipitation will reflect some of this energy back to the antenna and receiver. In addition to the time and direction calculation the receiver will assess the amount of return energy to evaluate the magnitude of the target. Analog systems would accomplish this by generating output of 5,000 watts or more. The sensitivity on these devices was relatively low so the only way to ensure
penetration of storm cells was to use a strong radiated signal. Newer systems using digital technology can achieve very high sensitivity in the receiver requiring power output in the 24-watt range. Capability and range are predicated on more than just a sensitive receiver.
Safety concerns
Radiated energy is only one concern when it comes to working around radar. The various electronic equipment may include sealed components containing such things as beryllium oxide, acid, lithium radioactive matter, and even mercury. It is always advisable to take precautions to ensure protection against inhalation or contact. Electrostatic discharge (ESD) is always a concern around any electronic device and awareness here can prevent possible catastrophic or latent equipment failures.
Many systems still in use contain a Magnetron; which is the main power output device. As the name implies this unit uses magnetic principles and in fact it is so critical that in some installations if the magnetron is installed improperly it may affect the aircraft compass systems. Also a magnetron is subject to degradation as a result of aging and it is the recommendation of several manufacturers that routine testing including power output, frequency, and sensitivity be accomplished at least once a year.
Handling, storage, and shipment of a magnetron also requires special attention. Interaction with any ferrous materials can be detrimental. Collins, for example, recommends a minimum 4-inch space between the magnetic components
and any ferrous matter. Even storage on metal shelving can be risky. It is desirable to ensure proper separation using wood or plastics but always be aware of the ESD potential. Much of this equipment is also susceptible to damage caused by mechanical shocks. In some cases dropping a receiver transmitter 3/4 of an inch can have devastating effects.
Flight deck displays
Flight deck displays take on many forms. Some employ the cathode ray tube principle while others use phosphorescence. Many EFIS systems even use liquid crystal displays (LCD). The type display may impact proper interpretation. Displays using phosphorescence are more prone to interference from sunlight and usually include some type of glare shield.
Selector panels in the flight deck control weather radar systems. In many
commercial aircraft both pilots have independent control panels and depending on the installation system operation may be aircraft specific. A "mode" selector is the means of setting the different functions of the device. "Off" is not an acronym for "on full force," but instead deactivates the system. A "test" feature is often included and while the system including the transmitter receives power the emission of microwave energy is inhibited. This function can allow visual inspection of the antenna to verify proper mechanical operation without concern for a radiation hazard. "STBY" is a feature that will allow the system to be powered but once again transmission in inhibited. Aircraft with dual control panels may allow radar operation if only one panel is in STBY while the other is selected to some operating condition. It is always advisable when planning maintenance to make sure both controls when applicable are appropriately set.
Some systems have a target alert (TGT) mode and when selected the pilots may not have control on the range or the antenna degree of tilt. The ability of the system to automatically control the antenna is only possible by
enabling the radar to determine the aircraft height above ground level. This is accomplished by allowing the radar beam to scan the ground every third sweep. This dipping of the beam should not affect the weather display. With TGT selected the system will evaluate a specific window in front of the aircraft in some cases up to 200 nautical miles. In the event of significant weather the flight deck display will provide the crew with a target alert as well as highlight the danger zone.
Selecting the "MAP" mode places the system in a terrain-mapping situation. This will allow prominent geographic features to be identified. This is most effective in the shorter ranges with the antenna tilted down.
Weather factors and performance
The "WX" or "weather" enables the radar to perform its primary function. Now the reflected energy is analyzed and based on rate and type of precipitation the flight deck display will depict as directed by the RT unit.
"Gain" is another feature where improper use can invalidate weather information. This adjustment will lengthen the transmitted pulse width plus impact the sensitivity of the receiver in newer systems. In fact with color displays, improper selection can alter the display by as much as one color level. Many systems have a "gain calibrate" feature. The pilot should always actuate this when one of the negative settings has been used.
A "tilt" function will allow for pitch adjustments of the antenna. This will allow the flight crew to map the ground or even determine the tops of storm cells.
"Range" control decides how far the radar will look in front of the aircraft. The greater the distance the arc of the transmitted signal is concentrated, close proximity storms may go undetected as it moves into the aircraft path from either side. In some systems with the radar operating with a range of 300 nautical miles, an area of 37 miles may
be blanked on either side of the aircraft.
Wave-Guides have been used as a device to carry the microwave energy between the receiver transmitter and the antenna. This hollow tube is designed with a specific shape and should be kept free of distortion and damage. Contamination is another concern. In the event moisture should get into the tube it can disturb the signal and have an impact similar to the aircraft having an encounter with weather. To prevent this, pressurizing the Wave-Guide is often accomplished and in other cases a desiccant is used to draw moisture from the device.
Antenna and radome development
Antenna concepts have changed significantly over the years. They have gone from the parabolic dish to the flat panel. Parabolic antennas had a tendency to emit side lobes which detract from the overall power output. Most radar antennas have the ability to pitch up and down as well as sweep side to side. The antenna can be automatically stabilized by the inertial system to keep the beam focused on the aircraft path during roll and pitch conditions.
The antenna is protected from the elements by a component called a radome. Certain physical and electrical properties have to be engineered into this covering so they are strong enough to withstand air loads and contoured to minimize drag. Physical properties vary with the shape, size, and performance of the aircraft on which it is installed.
Electrically, it should permit the transmitted signals and return echoes to pass freely. This should be accomplished with minimum distortion and absorption. This is accomplished by construction techniques including materials, thickness, and even shape. A very small variation in physical thickness may cause a sizable variation in electrical thickness. Radar efficiency, definition, and accuracy depend upon a clear, nondistorted,
reflection-free antenna view through the radome. Consequently, they should be precisely built for optimum performance.
Top: Radar antenna and RT unit combined. Bottom: Transmit inhibit switch installed on RT unit. Always make sure the transmitter is deactive around
antenna.
There are two general types of radar covering, the "thin wall" and "sandwich" types. Thin wall radomes are considered to be thin relative to the wavelength of the radar. They are generally useful when the radar frequency is low enough to permit a skin thickness that will satisfy the structural requirements. Sandwich radomes consist of two or more plastic skins separated by a dielectric core. The core may consist of honeycomb plastic sections, hollow flutes, or foam plastic. The dielectric and separation of the skins will depend upon the wavelength of the radar frequency.
Probably the most frequent damage to radomes is holes in the structure caused by static discharges. These can be large holes that are readily apparent or small pinholes that are almost imperceptible. Any hole, regardless of size, can cause major damage. Moisture can enter the wall and cause internal delamination. If freezing occurs, more serious damage results and when enough moisture collects, the radiation pattern will be distorted and the transmitted signals along with the return echoes will be invalid. Other types of damage include dents and scratches, but most types of damage
can be found through detailed inspections.
A radome having undergone major repairs should be tested to verify that its electrical properties have not been impaired. Testing requires specialized equipment. Improper repair may cause loss of signal, distortion, and displacement of targets, plus clutter the display to obscure possible storm cells. Some examples of improper repair include the use of inappropriate materials, patches of varying thickness, overlapping repairs, and excessive paint thickness or metal based paint.
U.S. FAA Advisory Circular 43-14 provides a guide for radome inspection and maintenance. However, specific aircraft documentation should always be consulted prior to any repairs.
Well now it's time to get back to my bratwurst, but this time I think I'll put it on the grill.
About the Author
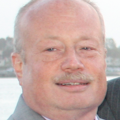
Jim Sparks
Jim Sparks has been maintaining aircraft for almost 40 years with the majority of the time involving Business Aviation activities. Jim’s endeavors have placed him on six of the seven continents contending with numerous situations from routine flight dispatch to critical AOGs. His career includes maintainer, avionics/electrician, educator, tech rep, and director of aircraft maintenance. In addition to other activities he is engaged with ASTM assisting in the global development of criteria defining the Next Tech for NEXTGEN. You can reach him at [email protected].