Avionics Technology
An Epic Tale
A look at an integrated avionics system
By Jim Sparks
July 2004
An epic is defined as a narrative poem that is majestic in both theme and style. Honeywell has pretty much captured this concept with the now widely used Primus Epic integrated avionics system. Although its introduction came a mere eight years ago it has now found homes in a significant number of business and regional aircraft.
The Primus Epic design challenge was to incorporate the latest avionics technology in a pilot-friendly manner while being smaller, lighter, and more energy efficient; but still meet higher standards for performance, reliability, and dispatchability. In addition a plan was conceived to reduce system size and weight by 40 percent while improving the ability of maintenance technicians to accurately and quickly analyze and isolate faults.
Many current flight decks are constructed based on the federated concept of avionics design. This is where individual components or "black boxes" contain hardware and applicable software to perform specific functions. Early auto pilot systems required an auto pilot computer and separate servo amplifiers that would generate the signals to move the various flight control devices. In more recent years these devices were located together in one box and flight guidance computers were even added resulting in an automatic flight control system (AFCS) computer.
The modular concept of the Epic system has resulted in what is called a "distributed system". In this case avionics functions, electronic circuits, and switching devices are replaced by software allowing data to be carried on high-speed buses to enable multiple tasks to be performed simultaneously.
The modular concept and the network
The heart of
Primus Epic architecture is the "Virtual Backplane Network" a Honeywell trademark, which was developed exclusively
for this system. Architectural concepts blend the cabinet-based modular
capabilities of the Honeywell created Boeing 777 system with the aircraft-wide
network capabilities. The architecture allows an unprecedented degree
of system integration by allowing data generated by functions within
the system to be available to other devices as well. Not only does
this eliminate many dedicated point-to-point wiring requirements,
but also allows seamless integration of functions across the entire
network.
A key component of the Virtual Backplane Network is the open architecture afforded with the bidirectional Avionics Standard Communication Bus (ASCB). For the Primus Epic system, the ASCB continues an evolution of the successful ASCB implementation used in many business and regional aircraft today. The new version of ASCB provides the data transfer equivalent of 100 high-speed ARINC 429 buses. The new bus significantly reduces wire weight, power use, and installation costs, while greatly increasing capacity to support aircraft utility systems control and other future aviation requirements.
The hardware packaging is built upon the modular avionics unit (MAU) which contains most of the functions within the system. The MAU houses field-removable computing, network, database, input/output (I/O) and power supply modules utilizing techniques and concepts developed for the Boeing 777. The flexible MAU architecture is designed to accommodate growth from light turboprop regional aircraft to heavy-class regional jets and business jets by configuring modules to multiple-sized MAU racks.
Computing modules within the MAUs and flat panel displays utilize a digital engine operating system (DEOS), which allows the different aircraft functions to run simultaneously and independently on the same communication bus.
This technology provides aircraft-wide utility system control capability. The displays and modular platforms will integrate aircraft systems including control and monitoring into the avionics system.
Photo 1: Falcon 900 connection for external computer used for diagnostics.
Photo 2: Synoptic displays indicate operating conditions of aircraft systems.
Photo 3: Flight deck displays can be used to view airframe and engine system and component function.
Photo 4: Cursor control device (CCD) is used like a computer mouse to navigate the display system.
Systems integration, design, and display
The first application of Primus Epic integrates the air conditioning, ice and rain protection, APU, hydraulic power, lights, engine starting, fire protection, stall warning, flight data acquisition, nose wheel steering, landing gear control, braking and fuel gauging systems. The resulting reduction of both cockpit controllers and line-replaceable units is intended to improve safety, maintainability, dispatchability, and overall cost of aircraft operation.
Human-centered cockpit design provides operators with an expanded choice of interfaces with the aircraft system. In addition to today’s controllers, various cursor control devices (CCDs), including touch pad, joystick, or track ball, are used to interact with the on-screen "soft key" controls. In the future, voice commands may be used for some functions. Initial applications favor the touch pad display and joystick.
Liquid crystal flat-panel displays (LCD) are available in cockpit configuration from two to six displays. This enables the cursor control to interact with the Windows type environment where information becomes movable including navigation maps, ground-based weather, real-time video, and aircraft utility systems display and control.
These displays include flight situational displays (FSDs) and multifunction displays (MFDs). The flight situational display incorporates all the information to safely operate the aircraft, including traditional primary flight displays, new radio tuning window, abbreviated caution advisory system (CAS) messages, and an engine instrument and crew advisory system (EICAS). The MFD displays navigational charts and weather data, as well as aircraft system pages and selectable video windows.
The EICAS display is an engine instrument format that provides the pilots and maintenance technicians with an enhanced means to control and monitor engine and associated system performance as well as accurately determine faults. EICAS graphically presents information about performance capabilities, current performance and engine component or system operational status, and can show normal conditions or even indicate areas where failure may have occurred.
The modular avionics unit (MAU) is a hardware cabinet containing field-replaceable modules that represent the "building blocks" of the system. The MAU incorporates input/output (I/O), processing, which receive and transmit information to the various airframe devices with which the system interacts. The MAU also contains data base storage modules linked to the ASCB. This is then linked to the aircraft-wide network via a network interface controller (NIC) module. The Virtual Backplane makes the MAU flexible and adaptive to requirements of different airframes allowing manufacturers the ability to reduce the number of control components. In some cases replacement of a circuit card will require a software upload that may be specific to that particular machine anytime the new device is put in place. It is essential to follow manufacturer instructions anytime component replacement is anticipated.
The integration of computer processing into a single unit means that the MAU can be shared to perform multiple tasks previously requiring individual computer processors. This increase in integration results in reduced power consumption, weight, reliability, and maintainability.
As the MAU contains numerous electronic modules one important constraint is it must be located in an environment where it has adequate ventilation. An air management module is part of the standard equipment and controls multiple blower fans to ensure proper cooling. In the event of failure the system can generate fault messages to inform technicians that fans may be at fault.
Maintenance issues
Information enters the MAU through electrical connectors installed on the face of each independent circuit card. A motherboard concept is applied here as the MAU contains the Backplane busing that enables the data transfer between the different modules. The concept of an MAU does in fact lessen the number of components allowing a significant reduction of weight but it also serves as a Faraday cage. This is a device that shields its contents from the adverse effects of static electricity. Another challenge for technicians maintaining this equipment is that a momentary lapse of judgment in the handling of a circuit card could place the device in jeopardy. Even the storage and shipping of electronic circuits require constant vigilance. Electrostatic discharge (ESD) awareness is critical.
The digital buses in use here are often impedance critical. This means that improper installation or even the incorrect installation of wire clamps could impact the ability of the bus to carry data. Manufacturers’ techniques and standard practices should always be consulted prior to doing anything that could impact the integrity of the buses.
The air data computer (ADC), global position system (GPS) sensor, and inertial reference system (IRS) or attitude/heading reference system (AHRS) in use today have been replaced by the integrated sensor suite (ISS), a complete primary sensor system. Each ISS function consists of three sensor components, which include the small line-replaceable inertial measurement unit (IMU), air data module (ADM), and GPS sensor module. Raw information from the sensors is processed by the system to provide all the inertial, positional, and air data information used by all other functions within the avionics system.
A digital remote mounted radio system includes the standard navigation and communications functions, including VOR, ADF, DME, ILS, VHF Communication and Mode S Transponder modules. The radio system uses LRUs from the Honeywell Primus II integrated radio system, housed in dual remote mounted radio cabinets.
This level of integration brings new challenges to the maintenance technician. Testing of the air data system is a prime example. It used to be cut and dry. Every two years the air data computer or altimeter was either removed and sent out or tested and certified while installed in the aircraft. In systems such as Epic there is no dedicated air data computer. Instead an air data module (ADM) will process the pitot and static pressures and then deliver the information via a digital bus to an I/O card. Here the information is received and then distributed to the rest of the system where air data corrections can be made prior to delivery of the data to the flight deck display.
Testing and diagnostics
So when it is time to perform the required testing and certification of the air data system what do we do? In addition there are requirements that anytime the flow of air data information is interrupted a check for correspondence error must be accomplished. What this means in a system heavily dependent on component integration, something as simple as swapping circuit cards for testing purposes, may place the aircraft in direct violation of airworthiness regulations. Airframe manufacturers are therefore obliged to create maintenance procedures that will appropriately direct technicians in required maintenance tests that are associated with specific component changes. In addition the integration of a central maintenance computer (CMC) will often provide technicians the information needed to make decisions on the integrity of the various system components and alleviate swapping or shot gunning of parts.
The aircraft diagnostic and maintenance system (ADMS) is in some installations an aircraft-wide interface where maintenance technicians can interact to initiate and observe system testing, retrieve faults stored by the system that may be used to enhance troubleshooting, and even determine dispatchability of the aircraft. The capability exists for the system to transfer fault information and maintenance data to ground stations even while the aircraft is flying so technicians can be prepared to tackle problems even before they are reported by the flight crew. In addition to viewing many of the maintenance functions in the flight deck, provisions can be made where remote computer terminals are installed to provide a second level of diagnostics. They do, of course, have the ability to download or even print reports containing information about engine trend monitoring or system performance and fault analysis plus enable technicians to view system data while not in the flight compartment.
Some airframe manufacturers will include minimum equipment list (MEL) information in the system. This capability will enable flight crews to make decisions regarding continued safe operation of the aircraft. MEL operation is predicated on aircraft certification and authorization of the governing Airworthiness Authority.
Wow, a system that can help us rig flight controls, troubleshoot various airframe and engine systems, and report specific faults when they occur. And it can tell us if the aircraft is in an airworthy condition and even provide a location where we can have access to electronic maintenance and support documentation. New technology makes a big difference in the way we maintain this new generation of aircraft. Enhancing the man-machine interface has taken on an entirely new role and it actually involves technicians and not just pilots.
About the Author
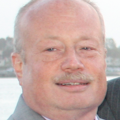
Jim Sparks
Jim Sparks has been maintaining aircraft for almost 40 years with the majority of the time involving Business Aviation activities. Jim’s endeavors have placed him on six of the seven continents contending with numerous situations from routine flight dispatch to critical AOGs. His career includes maintainer, avionics/electrician, educator, tech rep, and director of aircraft maintenance. In addition to other activities he is engaged with ASTM assisting in the global development of criteria defining the Next Tech for NEXTGEN. You can reach him at [email protected].