Acquiring Data: Inspecting and Troubleshooting
During routine maintenance it was determined that the thrust reverser installed on the No. 2 engine was not being monitored as it should have been by the digital flight data recorder (DFDR) however, all other aspects of operation appeared to be normal.
Investigation of the system revealed the thrust reverser positions were monitored by a group of dual contact switches. One set supplied information to the control and indication circuit, while the second set would report to the full authority digital engine control (FADEC). Aircraft manufacturer’s documentation was very elusive when it came to identifying the data path to get this information to the DFDR.
When presented with the above dilemma what would be a good approach to troubleshooting the problem? Diagnostic methods and techniques are frequently left up to the discretion of the technician assuming responsibility for resolving the problem.
The fact that a digital flight data recorder and a digital engine control are possible culprits, a logical troubleshooting tool would be a digital volt ohm meter (DVOM), right?
Computerized Systems
To put everything in proper perspective, all computerized systems can be broken down into three groups; input or sensors, data processing, and outputs or loads.
Everybody knows that digital systems involve 1s and 0s. So when I connect my DVOM to a digital circuit how do I know if I am looking at a 1, perhaps a 2, or even a 3?
Avionics suites installed in the aircraft of today have the ability to monitor many inputs, interpret data, and provide appropriate responses to the crew and other aircraft devices or systems. With this sophistication come enhancements for maintenance technicians. Most digital devices include some form of self-diagnostics.
Unfortunately it is the expectation of many that these built-in test equipment (BITE) circuits are all-knowing and will always point to the faulty device. The real purpose of diagnostic systems is to provide troubleshooting data and it is the interpretation of this information coupled with other diagnostic techniques that will most frequently isolate the true problem.
Communication Tool
Many look at electricity as an energy source but fail to consider the application as a communication tool. Three general classifications are used to classify how electrical signals are interpreted: analog, digital, and discrete.
Analog
The analog group includes the variables such as voltage, amperage, and frequency. Almost everyone has heard the phrase “Information out is only as good as information in,” and with many of the computer systems utilized on modern aircraft much of the input data comes from sensors. So what does a sensor look like? It could be the switch that monitors the extension of a main landing gear to determine the ground or flight configuration, it could also be the potentiometer linked to the wing trailing edge flaps that reports position.
There is also the rotary variable differential transducer (RVDT) that sends power lever position to the electronic engine control (EEC) by using variations on an alternating current signal. Even the tachometer generator that supplies wheel velocities to the anti-skid system is a sensor and depending on aircraft type will generate either a frequency or voltage proportional to wheel speed. Troubleshooting analog circuits can most often be accomplished using conventional techniques and a multimeter.
Digital
Digital communications also take on many forms. There are the industrywide standards such as Aeronautical Radio Inc. (ARINC) 429 and even proprietary languages utilized by avionics systems manufacturers. Circuits that use digital data have provisions to allow them to interact with digital buses. These paths for digital data are often thought of as wires and it is true that they are in fact made up of at least two wires twisted together and surrounded by a shield. The electrical properties of buses are specifically defined and are impedance critical. That means abnormalities with the shield, high resistance at connections, improper clamping, or even an excessive cable bend may interrupt or at least decrease the efficiency of the data transmission.
Many digital devices share information via busing networks. In addition certain devices such as pitot tubes and static ports are now fully electronic, providing the conversion of pressure to electrical signal within a module contained in the probe. This advancement has led to the elimination of mechanical plumbing and significantly reduced maintenance checks on air data systems.
Many are of the opinion that as many digital circuits have the ability to advise when problems occur that troubleshooting is limited to interpretation of messages or fault codes. This is an unfortunate misconception as a significant amount of the programmed fault detection circuits can not differentiate a faulty sensor from a failed wire or connector. It is true that some diagnostic software can detect and identify a failure of a digital bus, but unfortunately most cannot advise the technician exactly where the problem has occurred. Once again conventional test equipment and methods may need to be employed to recognize and then locate the cause of the malfunction.
Discrete Signals
Discrete signals are often confused with digital signals as the terms 1 and 0 are referenced. It is important to realize that these terms are not a constant but are relative to specific systems. Often circuit cards or devices controlled by a “black box” will have internal power supplies and manufacturers do not always clearly identify the output of these devices. Many components have been removed due to wrong interpretation of input and output signals. Just because a circuit has 28 volts going in does not mean it can not have inputs or outputs that are significantly different. The dilemma with thrust reverser mentioned earlier is a prime example where the thrust reverser control unit operates on 28v DC but contains an internal voltage regulator set at either 12 or 15 volts and this is the potential that is observed to determine reverser position. When switches are in the open position 12 volts is present. When specific switches close a ground is supplied to the detection circuit and the voltage drops to zero. Due to controlling resistors installed on the monitoring circuit card, the current flow in this detection circuit is limited to milliamps.
Another example involves the Honeywell Epic where in certain installations the input/output (IO) circuit cards use a 14 volt potential for the evaluation of a discrete. When the monitored device is in an open state the monitored voltage is 11 to 14 volts. When the observed component switches ON then a ground is supplied and the potential will drop into a range of 0 to 3 volts. The IO circuit card is programmed to look for either something less than 3 volts or something higher than 11 volts. In the event of a signal in the range of 3 to 11 volts the system has no way of recognizing the condition of the monitored device and may then generate a message to a central maintenance computer. In this case, a minor amount of corrosion in the ground circuit could easily restrict the milliamp current flow and cause an elevated discrete where an improper operating condition would occur.
Component Surveillance or DAU
Digital flight decks require vast amounts of information and on many current generation aircraft, almost every component that has a wire going to it can be monitored and in turn impact the operation of the system. As many avionics suites are designed with the intent to fit a wide array of aircraft, the means of providing surveillance for significant airframe components has to be conceived. An appropriate name for such a device is a data acquisition unit or DAU for short; there are other terms that describe the function of liaison between avionics and airframe such as IO circuits.
Most avionics manufacturers have created proprietary digital languages enabling communications between all of their components that require interaction. In certain cases avionics-related devices may have the need to provide data for other airframe-related computers. This is another situation where an IO circuit or DAU may play a significant role. There are numerous situations where digital interpretation has to take place and a different language is used for the output command. An example of this would be where an air data signal relating to current aircraft rate of climb is transmitted in a Honeywell language and is then sent to an IO card which translates the input and converts it to an ARINC 429 output which can then be used by the aircraft pressurization system computer to regulate the passenger cabin altitude and to a second device that will control the amount of bleed air extracted from the engines.
Blending Information
Another function often associated with a DAU is the blending of information. This involves the use of often complex logic circuits that are often described using formulas based on Boolean logic. Caution and warning functions on many aircraft are the result of the DAU sensing the real need of bringing attention to a certain condition. In the “good old days” an engine “low oil pressure” light would be illuminated anytime oil pressure was below a critical low value. Which means the entire time the aircraft is in for maintenance and has electrical power applied the warning circuit is active. With the ability to blend data, a DAU sensing the low oil pressure switch can also observe the engine cutoff switch. This means that when the engine is not operating the oil pressure warning circuit is not active.
Avionics systems that use an internal maintenance computer can often provide maintenance technicians with a valuable tool for problem recognition as well as direction for resolution. Memories dedicated to storing flight faults can help associate a fault with a specific circumstance and may help bring to light anomalies that could be the gremlin in that ever elusive flight fault. Some diagnostic systems provide a means of observing or even interacting with numerous systems while all the time being seated in the flight deck. Being able to see the condition of many components during operation can be a tremendous asset in solving problems.
Certification
An important fact in dealing with a DAU is its place in the aircraft with regard to certification. U.S. Federal Air Regulation (FAR) 25.1431 provides guidance to manufacturers regarding interaction of electronic components and required operating power supplies. One excerpt states that “radio and electronic equipment, controls and wiring must be installed such that it does not cause essential loads to become inoperative as a result of electrical power supply transients.” This statement has been the cause of many a “Gotcha”. As a result of this design constraint some manufacturers install backup power sources to data acquisition devices and often they are not clearly identified. In some cases while performing operational or functional checks, lack of knowledge about redundant power supplies may be the difference between an “on-time departure” or a delayed and possibly cancelled flight.
Many digital flight data acquisition units (DFDAU) have become required in early generation aircraft to allow compliance with regulatory agencies’ mandates for flight data recorders. Often these devices can supply secondary benefits such as provide limited amounts of trend monitoring for airframe and engines and in some cases the ability to generate reports that can assist with problem solving.
Simply by the nature of what they do, DAUs can be a true friend to the aircraft technician. By their nature they supply a common point where many systems come together and provide a point of access for troubleshooting.
The best approach to understanding the ins and outs of the DAU is knowledge. Manufacturers’ educational programs are often the best way to begin the learning process and visits from knowledgeable field technical representatives can also be very enlightening, especially when they show up at the beginning of the lunch hour equipped with their company credit card.
Additional ReSources
ARINC
www.arinc.com
Honeywell
www.honeywell.com
Rockwell Collins
www.rockwellcollins.com
About the Author
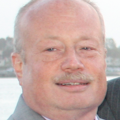
Jim Sparks
Jim Sparks has been maintaining aircraft for almost 40 years with the majority of the time involving Business Aviation activities. Jim’s endeavors have placed him on six of the seven continents contending with numerous situations from routine flight dispatch to critical AOGs. His career includes maintainer, avionics/electrician, educator, tech rep, and director of aircraft maintenance. In addition to other activities he is engaged with ASTM assisting in the global development of criteria defining the Next Tech for NEXTGEN. You can reach him at [email protected].