Corrosion is an age old enemy of the aviation industry. As the worldwide fleet of commercial and private aircraft matures, it is up to those of us in the support field to ensure continued airworthiness. Most learn early on that the effects of exposure of bare metal to the elements results in some form of degeneration. This fact has stimulated many different programs addressing inspection of aging aircraft and countering the effects of metal fatigue and corrosion.
Well, what about the effects of time and elements on avionics equipment? A common misconception is that “black boxes” are most often sealed and therefore don’t require the surveillance and scrutiny associated with aircraft structural components. Many technicians are familiar with the U.S. Federal Aviation Administration Advisory Circular (AC) 43 – 4 which addresses inspection and corrosion in aging aircraft. There does not currently appear to be the same familiarity with AC 43 – 206 which is titled “Inspection, Prevention, Control, and Repair of Corrosion on Avionics Equipment.”
Corrosion control
The proper care of avionics equipment requires a thorough understanding of aircraft electrical/electronic systems corrosion control. This knowledge includes the definitions and descriptions of the situations that cause problems in avionics equipment. Corrosion is the natural process of materials returning to their natural state. A good explanation of this process is where a chemical or electrochemical deterioration of a material, usually a metal, occurs because of a reaction with its environment. This deterioration can be complex and needs to be investigated prior to applying any remedy. The nature of the different individual types of corrosion, simultaneous attack by several types of corrosion, and the design characteristics and maintenance factors that make avionics systems susceptible to molecular deterioration require specific resolution.
Corrosion can cause intermittent malfunctions, undesirable changes in electrical characteristics, or complete equipment failures. Avionics equipment does not have to be installed, operated, or located in a particularly harsh environment to be affected by corrosion. Some forms of corrosion will be active in near ideal environments. Avionics maintenance personnel should recognize that corrosion never sleeps and once started, will continue to attack 24 hours a day, 365 days a year. Inadequate prevention and control will ultimately affect the equipment in cost, downtime and overall system reliability.
Most aircraft electrical/electronic equipment should be opened and inspected for evidence of internal moisture and corrosion on a scheduled basis. When anomalies are detected, prompt corrective action is required and should include cleaning, removal, treatment, application of protective finish, and preservation where required. Maintenance personnel should always use the mildest method of cleaning and removal.
Design compromises
There are many design decisions and compromises to be made in the course of developing avionics equipment. The design specifications leave room for a wide range of engineering practices to meet not only the performance, cost, and schedule, but also the reliability and maintainability requirements. Each piece of avionics equipment is designed to withstand its intended operational environment. However, some design compromises have to be made to provide the unique electrical, mechanical, and thermal characteristics of the equipment. These compromises can cause the equipment to be vulnerable to corrosion, especially during inoperative periods. According to AC 43-206 good design practices include:
Shoe box type lid construction. When access to the equipment is from the top, use a shoe box type lid construction. Fasteners securing the shoe box lid should be from the sides and not through the top.
Limited openings in the equipment housing. To reduce moisture intrusion, keep the number of penetrations into the equipment to a minimum. When penetration is required, use “O” rings and gaskets for sealing. For wiring entry, use “L” type electrical connectors and mount them horizontally (through the vertical sides), and well above the bottom of the housing.
Proper electrical connector mounting. Electrical and coaxial connectors should be mounted horizontally (through the vertical sides). When electrical and coaxial connectors are mounted on the top of the equipment, there should be a raised area on the upper side where the connector is mounted and an “L” type should be used. Electrical wiring should incorporate a drip loop into the wiring harness so the wiring is leading up to the connector.
Proper printed circuit board mounting. Printed circuit board (PCB) should be mounted vertically with the electrical connection also in a vertical position.
Low point drains. Low point drains should be incorporated so that any moisture will drain from the equipment when the aircraft is in normal flight and when it is parked on the ground.
Eliminating moisture traps. Avoid moisture traps or “bathtub” areas on the interior areas of the equipment. Identify drain paths to the low point drains. Avoid moisture traps in electrical wire bundles where anti-chaffing material or boots are incorporated.
Cooling air systems. Cooling air systems should incorporate a means to remove moisture and particulate matter from the conditioned air. This is especially important when the air is forced directly toward active electronic elements.
Proper bonding and grounding. Electrical bonding and grounding should be accomplished using straps rather than “sliding housing-to-rack” or tapered pin on housing-to-rack electrical contacts. Straps should be located for ease of maintenance and properly sealed because of the dissimilar metal (galvanic) couple.
Proper equipment mounting. Avionics equipment should be mounted in such a manner that will allow sufficient airflow and should be kept at least 1/2 inch above the compartment floor.
Proper material selection
Proper material selection is critical for protecting avionics equipment against the environment. Many types of corrosion that occur in electronic devices also occur in the airframe structure. However, the range of material called out in avionics equipment is usually greater than in the airframe. Several new types of degenerative symptoms are unique to avionics equipment. The following indicate the uses of different materials in the construction of various electrical and electronic components:
Copper and copper based alloys are generally used in avionics systems as contacts, springs, leads, connectors, printed circuit boards (PCB), conductors, and wire. Iron and steel are used as component leads, magnetic shields, transformer cores, brackets, racks, and general hardware. Magnesium alloys are used extensively throughout avionics systems as antenna structures, chassis, supports, and frames (radar). Nickel and tin plating are used for protective coatings and for material compatibility purposes. Tin is also one of the components of solder. Tin plating is used on radio frequency (RF) shields, filters, and automatic switching devices. Silver is used as a protective plating material over copper in wave guides, miniature and micro-miniature circuit boards, tank circuits, and RF shielding. Aluminum and aluminum alloys are widely chosen, because of their light weight, in equipment housings, chassis, mounting racks, supports, and electrical connector shells. Cadmium is used as a sacrificial coating on ferrous hardware, such as bolts, nuts, washers, and screws. Ion vapor deposition (IVD) of aluminum is also used as a sacrificial coating on hardware and is a nonhazardous replacement for cadmium. Gold is commonly used on electrical connectors, contacts, and edge connectors where the lowest electrical resistance is required.
Due to the complexity of the material process used in modern electronic assemblies, it is sometimes difficult to predict if potential problems will be created by the reaction between two or more nonmetallic materials in a circuit assembly. Incompatibility of materials can result in the release of chemicals or gases that will react with other circuit components. In some cases, the incompatibility of cleaning solutions will cause reactions in substances that are corrosive to associated circuitry. The following list contains several of the potential problems:
- The heating of some protective coatings may cause gassing that can be corrosive to metal components.
- Some commercial coating strippers contain acids that attack PCB laminates, and discolor or corrode copper.
- Certain silicone sealants contain acetic acid that is highly corrosive to metal components in avionics circuits.
- Some potting compounds revert to a liquid form under certain conditions. This reversion process reduces moisture protection in electrical connectors.
- Degradation of polyvinyl chloride gives off acetic fumes which are corrosive to most metals used in avionics equipment.
- Shrinkable elastomers (heat shrink) tubing, although not a problem directly, can cause damage to adjacent circuitry when heat guns are applied to shrink the tubing.
- . Some dry film lubricants contain graphite, which is an excellent lubricant, but graphite is also corrosive. Graphite, in the presence of moisture, promotes galvanic corrosion. Other dry film lubricants contain molybdenum disulfide which when combined with moisture and heat can form a corrosive sulfuric acid.
- Certain oils, especially silicones and greases, tend to migrate as temperature changes, which may result in contamination of coatings, attraction of dust, and the possibility of holding moisture.
Perspiration and other factors
Often overlooked causes of corrosion are the salts and oil found in human perspiration. Wearing protective gloves may result in electrostatic discharge (ESD) damage so situational awareness is an important factor when handling sensitive components.
Avionics components are subject to dust and lint accumulation. This condition is generally evident when the equipment has been installed for long periods of time and can become more severe with forced cooling air. In addition to the dust and lint accumulation from the movement of air, dust and lint can be attracted by magnetic fields from electric currents surrounding wiring and equipment. Dust can also accumulate on both the external and internal surfaces of components when ventilating holes and louvers are incorporated. The problem with accumulation of dust and lint is it will trap and hold moisture which can provide the electrolyte for corrosion and fungus growth, plus dust and lint can degrade avionics equipment by being a conductor or an insulator. When dust and lint act as a conductor in the presence of moisture, they can provide a path for a current flow to either ground as a short or an unwanted circuit path between components. When dust and lint act as an insulator the avionics equipment can overheat causing premature failure. This can be compounded as excessive lint accumulation on air inlet screens or filters will significantly reduce cooling air flow.
Antenna systems are exposed to severe environmental situations. Without adequate corrosion protection numerous failures including shorts, open circuits, loss of dielectric strength, signal attenuation, poor bonding, or electromagnetic interference (EMI) may be experienced. Structural damage to the aircraft can also result. Antennas mounted on the fuselage require openings in the aircraft skin to route the various cables to the antenna plus provide structural attachment. The area around the antenna mounting is susceptible to moisture intrusion from rain, de-icing fluids/materials, condensation, aircraft wash, and internal fluids (i.e., fuel, oil, lavatory and galley products, etc.). Antennas mounted on the lower fuselage are particularly susceptible.
It should go without saying that we are working in a field where there is frequent exposure to hazardous chemicals and processes. Anyone involved with an unfamiliar chemical or product should always investigate what types of personal protective equipment need to be employed. It is important to remember that corrosion is a material in the process of returning to its natural state and inhaling or even absorbing through the skin may have some disastrous effects to a person’s health.
Corrosion and environmental conditions are natural phenomena that adversely affect avionics equipment. Although they can never be totally eliminated, the problems these phenomena cause can be minimized so that they are more manageable. This can be achieved only by understanding the equipment failure mechanisms, implementing a preventive maintenance program, and using corrosion control techniques and materials.
Jim Sparks has been in aviation for 30 years and is a licensed A&P. His career began in general aviation as a mechanic, electrician, and avionics technician. In addition to extensive hands on, Jim created and delivered educational programs for several training organizations, and served as a technical representative for a manufacturer of business jets. Currently when not writing for AMT, he is the manager of aviation maintenance for a private company with a fleet including light single engine aircraft, helicopters and several types of business jets.
About the Author
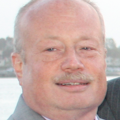
Jim Sparks
Jim Sparks has been maintaining aircraft for almost 40 years with the majority of the time involving Business Aviation activities. Jim’s endeavors have placed him on six of the seven continents contending with numerous situations from routine flight dispatch to critical AOGs. His career includes maintainer, avionics/electrician, educator, tech rep, and director of aircraft maintenance. In addition to other activities he is engaged with ASTM assisting in the global development of criteria defining the Next Tech for NEXTGEN. You can reach him at [email protected].