Yesterday was Saturday. Like many Saturdays in corporate aviation, it was simply one of two days between Friday and Monday. My reason for being at work was to assist in the replacement of a part on an aircraft that was scheduled to depart the next day. We discovered the failure during a routine pre-departure check and tried to obtain a replacement from the airframe manufacturer. Unfortunately, the aircraft in question is out of production and the OEM is more inclined to stock parts for currently manufactured airframes. Plan B was to contact reputable vendors likely to stock our required component and have it shipped in for a Saturday delivery.
Some thoughts came to mind while contemplating the whole process. The supply of quality parts is the lifeblood of aviation and includes the accompanying restrictions and debilitating circumstance.
Replacement necessary
Procuring the correct part begins with the technician’s decision that a replacement is necessary. Research is frequently the first step in obtaining a replacement component. What factors are to be considered? If the aircraft is registered in the United States, the Federal Aviation Administration (FAA) has some established guidelines. Although there is no official definition of the word “airworthy” in the Code of Federal Regulations (CFR) Part 14, it is implied that for an aircraft to comply it must: “Conform to its type certificate (TC). A product conforms to its TC when its configuration and the components installed are as described in the drawings, specifications, and other data that are part of the TC, which includes any Supplemental Type Certificates (STC), Airworthiness Directives (AD), and field approved alterations incorporated into the product; and the aircraft (product) must be in a condition for safe operation.”
Note: If one or more of these conditions are not satisfied, the aircraft or product would be considered not airworthy.
Part selection
The type certificate is a good place to begin the quest. It is unlikely that the TC will contain a complete list of parts but it will provide the guidance as to which documents may be used to assist in selecting the appropriate device. In many cases the FAA will not approve all of the supporting documents for a specific aircraft type but will label such things as maintenance manuals, service bulletins, and parts catalogs as “Acceptable Material.” Ascertaining applicability is the next step in the process. Unfortunately, the fact that a part is listed in a parts catalog does not mean it is correct for the aircraft specific configuration.
An Air Data Computer may have several versions; if the aircraft operates in reduced vertical separation minimums (RVSM) conditions, an STC may provide the required part number and may be contradictory to the aircraft parts catalog. The “black boxes” used in avionic suites will sometimes have different modification levels and the part number of a replacement unit may be predicated on other devices in the system. This can often be a dilemma, especially when you are advised that a part number has been superseded.
One recent experience involved replacing one of three integrated avionics computers. Initial contact revealed no availability of the specific part number. Communication ensued with the aircraft manufacturer’s help line and a service bulletin came to light that provided the authorization to utilize a later version of the failed device. The order was placed, the component arrived, and the technician involved in the project fortunately had the foresight to read the applicable service bulletin prior to installing the new computer. The manufacturer was correct in that this new part number could be used, as long as the other two computers were upgraded at the same time. Further telephone contacts located the correct part number and financial ruin was averted.
Other considerations include life limits and calibration dates. If a barometric altimeter with an 18-month-old date of certification is purchased and installed by a licensed airframe technician, the required leak check can be performed and signed off under the authority of the license. The 24-month validation can only be complied with by an entity defined in Federal Air Regulation (FAR) 43 appendix E. This means the altimeter can remain in service for about six months prior to requiring a new certification.
The challenges of shipping parts
Once the component of choice is identified, arrangements can be made to get it from the hands of the parts broker to the aircraft.
Shipment of aviation components can present a unique set of challenges and should not be left to the faint of heart. The FAA has recently created a task force with the mission to ensure aircraft operators are being responsible when it comes to the shipment of materials by air. To date, it has issued a notable number of citations. Those in charge of providing these services do require significant knowledge of Department of Transportation requirements and the International Air Transport Association (IATA) “Transportation of dangerous goods regulations.”
A number of factors need to be considered when selecting a means of transport including: how quickly the part is needed, delivery services available to serve the location, whether the part is considered a hazardous material, the risk of induced damage, and consequence of loss.
Lithium batteries are a common power source for today’s electronics and serve many functions in aviation. However, shipping them can present a problem. Under certain circumstances these batteries can ignite and can be very difficult to extinguish — so shipment in bulk within an aircraft baggage compartment is restricted.
Another hazard associated with electronic equipment is electrostatic discharge (ESD). This phenomenon is the result of objects with different electrical potentials coming within a close proximity and having a spark occur between them. Most technicians realize that certain precautions should be taken when handling components prone to ESD damage.
Transportation Safety Administration (TSA) inspectors involved in looking over counter to counter air shipments may not be aware of the potential damage associated with opening ESD bags under improper conditions. There are many guilty parties when it comes to the improper handling of avionics equipment. This is a problem that seems to worsen as time passes, probably as a result of more and more general aviation aircraft becoming more dependent on equipment and systems driven by software.
Exposure to ESD will not always result in an immediate catastrophic failure. There are situations where latent faults are induced as a result of ESD occurrences. A latent fault is when a component performs as it should during testing but when exposed to certain possibly extreme conditions while in operation, breakdowns will occur. Avionics manufacturers will not often cover ESD-induced damage under the product warranty.
Dead on arrival
Mechanical damage is another factor associated with the moving of aircraft parts from the distribution facility to the end user. This is not always limited to crushed instrument cases and broken glass. Many components employed in the operation of aircraft require specific magnetic properties.
What are the means of negating a permanent magnet? Heat, exposure to an alternating current field, exposure to another magnet, and the application of a mechanical shock (such as falling on the floor) are the most frequent culprits when this type of component is dead on arrival. Once again, proper packaging and adequate labeling is an essential precaution when shipping any magnetized device.
Motion sensing components, otherwise known as inertial units, include extremely sensitive gyroscopes and accelerometers. Many of these units display placards reading “Handle Like Eggs,” which probably does not relate to the handling of rotten eggs when expressing one’s true feelings in regard to some negative situations.
Most gyroscopic equipment does contain internal cages or stabilizing mechanisms to secure the internal moving parts during periods of inactivity. In the event that physical damage is noticed on a shipping container used for inertial equipment it is worthwhile to return the device to an agency for a complete operational assessment prior to installation in an aircraft. It is a common practice to see force sensors included in shipping boxes involving motion sensitive components. These often consist of a delicate glass tube containing a colored fluid, all encased within a small sealed box with a viewing window. In the event of a significant mechanical jarring, the inner glass tube will shatter and release the colored fluid within the box. When the viewing window is checked by the person receiving the part, the colored fluid is observed. This should be a cause for rejecting the component and possibly filing a claim with the shipping agent. Other types of mechanical “G” force sensors are frequently used as well.
The use of shock detectors is not always a standard practice. There are vendors that require specific instructions from the customer to include these telltale devices in parts shipments. Taking into account that gyros and inertial sensors are not always easily accessible once installed, having pre-emptive knowledge that the unit may have been exposed to a damaging circumstance may offset an inflight failure or a mission canceling fault.
Flight deck and cabin displays may also require special attention when shipping is required. Most new technology display monitors are required to meet stringent impact criteria and will frequently survive even the most aggressive delivery person.
One recent event involved a liquid crystal display (LCD) monitor that remained overnight in a nonheated environment with sub-zero outside temperatures. When the technician received the device in the morning and installed it in the aircraft, it would not initially come up when power was applied. After several moments the technician shutdown the aircraft and assumed the received unit was faulty and went to order a replacement. In the mean time, another technician turned on power and within a short time the temperamental display began to operate. This feat did not involve sacrifice or incantations. In fact, the display contained an internal heating network and a temperature sensitive switch that would prevent the device from working until the internal temperature reached 50 F. This bit of information was not readily available at the time, so the technician replaced the suspect faulty display and received an invoice for testing and re-certification of the part from the airframe manufacturer who returned it to service “no fault found.”
No fault found
The above mentioned phrase “no fault found” is the scourge of many technicians when evaluating a replacement part for installation. Component testing for return to service is usually defined by manufacturers and is accomplished in a controlled environment.
Actual operation within the aircraft will present conditions possibly involving temperature extremes, vibrations, and the result of drastic pressure change. When replacing any aircraft component with one that had been either repaired or overhauled, it is worthwhile to investigate the device’s history. In some cases a part may have been returned to the vendor in the past more than once for repair of a specific defect and is deemed serviceable by the repair agent without finding any failures, only for it to have the same anomaly when installed in the next aircraft.
Many technicians who have been bitten by the words “no fault found” will refuse to install these suspect devices. One particular airframe manufacturer reports approximately 60 percent of its warranty parts have been returned to the field “no fault found.” A situation like this may not always mean the repair agent is not doing their job, but could be an indicator the technicians replacing these components do not really have a good understanding of the systems involved.
Customer support
Honeywell has recently introduced a “Three Strikes, You’re Out” policy on certain repaired components. This effective customer support initiative has repair technicians taking into account some of the nonstandard situations that result in intermittent operation. In the event a covered part is returned for repair three consecutive times for a similar fault, it is subsequently removed from service. In any case, it is the job of the technician to provide the component repair agent with details of the fault. Most of us have encountered flight crews that create a write-up that reads “Inop.” Please don’t do the same thing to our allies in the repair centers.
Reputable parts suppliers who understand the nature of our business are a tremendous asset. This is especially true when you have one located in your area willing to meet you at odd hours to deliver an essential component. (Thank you, Al Zito.)
Well, most of my Sunday has evaporated. I wonder what challenges the next seven days will present.
About the Author
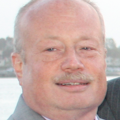
Jim Sparks
Jim Sparks has been maintaining aircraft for almost 40 years with the majority of the time involving Business Aviation activities. Jim’s endeavors have placed him on six of the seven continents contending with numerous situations from routine flight dispatch to critical AOGs. His career includes maintainer, avionics/electrician, educator, tech rep, and director of aircraft maintenance. In addition to other activities he is engaged with ASTM assisting in the global development of criteria defining the Next Tech for NEXTGEN. You can reach him at [email protected].