When many aircraft operators hear the word “Retrofit” it is often accompanied by an undeniable $$ KACHING $$ (sound of a cash register). When taken in the appropriate context, the word makes perfect sense: “To provide with parts, devices, or equipment not in existence or available at the time of original manufacture.” Of course, implementing any of those words in an aircraft always sounds expensive. A significant percentage of aircraft used in business and commercial aviation were manufactured prior to the turn of the century; with technology advancing at warp speed, it all too often becomes necessary to evaluate the capability of the equipment to fulfill present and future missions.
There are all kinds of reasons for upgrading business aircraft avionics: whether the change is mandated, or to take advantage of the latest technology that revolutionizes safety, communications, situational awareness or operational capability. In some cases, adding an electronic flight bag (EFB) may deliver many of the desired upgrades without the expense and downtime associated with complete retrofits.
Determining the criteria
So, what are the criteria to determine whether to renew, replace, or retire present equipment? Numerous factors should be considered, first of which is continued supportability of the airframe. A Hansa Jet for example, was considered by some to be a business jet that was ahead of its time when introduced into service in 1964. Production was limited to around 40 aircraft with fewer than a dozen in flyable condition today. A recent Airworthiness Directive limits the life of the aircraft to 15,000 flights or flight hours. Designing, engineering, and installing a new digital avionics suite and automatic flight control system for such an aircraft would be a sign the perpetrator has more dollars than sense.
It should also be understood that some aircraft and subsequent components have design life limitations. A few models, through ongoing evaluation, have been allowed to exceed the proposed life limits of their designers. Operators of those aircraft still have to contend with a little known factor called Commercial Life. The concept of producing and supporting components for as long as profit exists is a big part of a free enterprise system; as time goes by the spares inventories tend to evaporate, making the technician’s life more challenging. Some equipment manufacturers are willing to share their perspective regarding equipment life and this information should be solicited as part of project planning.
Recent or current production airframes, where at least several hundred have been produced, are often good candidates for upgrades and if the manufacturer can be involved in the process added value is almost certain. As most airframe manufacturers are in business to sell aircraft, it is often contrary for them to support refurbishment of out-of-production products. It will at least be advantageous to find out to what degree the airframe manufacturer will continue to support the machine once the retrofit is accomplished.
One question that is usually worth asking during the equipment selection process is: Has this been done before? And if so, in how many other aircraft of my type? Ingenuity is often a good thing but having a one-off type of aircraft can be another cause for elevated blood pressure in maintenance technicians when it comes to support and continued airworthiness.
Research and preplanning will be the key to success in any avionics refurbishment.
Project input should be solicited regarding the primary mission of the aircraft, along with an estimation of how much time the aircraft will be performing other than primary functions. That is, will the aircraft be used primarily for short trips within a specific geographic region and do a periodic overseas flight?
Estimated completion time including certification is another factor that could have a significant impact on what actually gets accomplished. Autopilot compatibility with newer generation flight systems is one thing that can cause a price estimate to quickly add numbers between the dollar sign and the decimal point (along with an extension to downtime) and may require a series of flight tests before certification is complete.
Last but not least is consideration of the financial contribution the aircraft owner is willing to make, along with determination of aircraft value after the project has been completed.
Choosing a manufacturer
Once it has been decided what features are to be added, it is worthwhile to make inquiries about which avionics manufacturers can accommodate the need. Some additional questions should be asked including the manufacturer’s ability to maintain the system once it is in service, as some use dealer networks to get their product distributed and supported. It will be worth knowing who will be the point of contact for service, operating hours, and typical lead time to deliver parts to customers.
If international borders separate equipment manufacturers from customers, then shipments will require a customs clearance. This has been known to add days to an AOG situation.
It is also worth inquiring about a loaner equipment pool. Manufacturers have different policies in the event of component malfunction during the warranty period. In some cases a new replacement will be issued, while in other situations a repaired or overhauled device may be supplied as a replacement. Consideration should be given that obtaining a device with similar time in service may not be easily achievable. It is also worth the time to verify that the specific equipment planned for installation is not unique to only one aircraft. That will definitely hamper possibilities of obtaining a timely replacement.
Interfacing with existing systems
A determination should be made regarding what equipment will remain. In some cases, the cost of interfacing existing devices with new technology may come close to or even exceed the price of a replacement. Often components such as coax cables and wiring are planned for continued use and if that is the case it should be predicated on their being thoroughly tested. Antenna coax does tend to degrade with age and replacing radios without changing the transmission line can result in less than desirable operation of the new device. Existing wire routing should also be analyzed. In some cases co-locating certain types of wire can result in electromagnetic interference (EMI).
In addition, adhering new wires along with existing bundles may present unwanted situations as excessive tightening of wire clamps, or tie wraps can compress insulation and alter the impedance of circuits. Existing splices and terminal connections should be inspected for security and general condition. A minor amount of dirt or corrosion in an electrical connection can have a significant impact to a circuit that may now be expected to carry milli-amp current flow. In the event low power digital weather radar is planned, it may well be worth the expense of having the radome either overhauled or tested to verify it will not hamper radar transmission.
Weight and balance should be considered along with a pre-installation calculation prior to finalizing a retrofit sales agreement. A recent situation occurred where a non-aviation savvy individual procured a helicopter and contracted a local shop to outfit it with all the latest equipment. Once completed, it was discovered that when fully fueled, the ship could carry the pilot and one-half a passenger with no luggage.
This may be acceptable if the aircraft is intended to carry only a few passengers short distances. Unfortunately, that wasn’t the case.
Consider impact of changes
Technology upgrades tend to supply many advantages. Newer equipment is frequently lighter in weight, consumes less electrical power, and produces less heat than predecessors. The above statement is not categorically true and does point out several factors.
A preview of the Electrical Load Analysis is a good starting point. Size and weight of components will influence location and structural attachment to the airframe. When determining the site for a new device, maintenance accessibility is an important factor. Equipment with a known high reliability may not require a position in the most convenient location, but if their planned installation does impede access to other devices, further consideration may be in order.
Just because new flight displays that produce less heat than the equipment they replace are installed in the instrument panel does not always mean the overall panel will be cooler.
Often new equipment does not have the same dimensions as previously removed equipment and the change could alter the normal airflow to other instruments. In one such case, new electronic flight displays were installed in a Falcon 20 business jet and during the test flight it was noted that an oscillation occurred with the cabin pressurization. Troubleshooting did not reveal any smoking gun.
To try to keep the aircraft on the promised delivery schedule the maintenance repair organization (MRO) employed the shotgun method of troubleshooting and replaced all suspect components. The next test flight verified that the problem had not been corrected.
Further testing revealed that when the circuit breaker for the newly installed instrument panel cooling fans was disengaged, the pressurization problem disappeared. As the aircraft pressurization controller was an electronic device, it was decided the culprit must be related to EMI. Both fans were replaced as a precaution and the wiring was changed to a shielded type. On the next flight, the pressurization discrepancy was still present. Finally the pressurization controller was wrapped in aluminum foil and then flown. Success! This gave the technicians added assurance the problem was in fact EMI and rigorous testing and improved shielding techniques were incorporated but the next test flight revealed the problem persisted.
The pressurization controller was removed from the panel and an inline test box with wire extension was installed to find out exactly when and where the EMI was present. A technician riding in the jump seat held the controller and planned to record the readings from the test equipment. Unfortunately, on this flight, the problem did not occur. Once on the ground the test equipment was removed and while the controller was being secured in the panel the technician noted a slight whistling noise . The technician then realized that one of the newly installed cooling fans was blowing air directly across the cabin pressure sensing port on the controller, causing a venturi effect. By relocating the fan they solved the problem.
What’s included?
What exactly can be included in a retrofit or upgrade project? When you talk with a salesman, it sounds like just about anything! Some of the more popular items include new flight displays. Liquid crystal displays (LCD) do provide significant improvement over the phosphorescence of older electronic flight instrument systems (EFIS). Much more information can be made available to the flight crew to enhance situational awareness. Enhanced vision systems (EVS) can fabricate an image by disseminating data from an infrared sensor,helping the pilots reduce possibilities of runway incursions. Digital satellite weather can be portrayed on an area map, including important specifics regarding en route and destination forecasts.
Electronic charts containing route of flight and navigation data can be portrayed with an aircraft position overlay based on information from global positioning systems (GPS). In some cases aircraft operating documents can be loaded and displayed on flight deck displays and include checklists, minimum equipment list (MEL), and even the maintenance manual. Many new technology avionics suites include an internal maintenance computer allowing storage of certain faults, ability to run operation checks on components or systems, and can provide diagnostic assistance for timely problem resolution.
Documentation
Many major MROs have an on-staff airworthiness representative who can assist in the return to service authorizations. In many cases aircraft retrofits are accomplished by Supplemental Type Certificate (STC) with accompanying Flight Manual Supplements.
Once the project is completed, the accompanying documentation is often filed away with other aircraft historic records. Many STCs include a section addressing Inspection Checks for Airworthiness (ICA). It is here that items such as structural inspections for antenna installations and bulkhead feed through fittings are noted along with recommended component testing, servicing, or overhaul intervals. These documents should be closely scrutinized and the new checks included in the aircraft inspection program.
Followup training
Most installations are accompanied by piles of wiring diagrams and installation manuals and, if you’re lucky, one of the installers might show you how to turn the thing on. An often neglected part of the successful flight deck upgrade is the crew educational process. Indoctrination with the company president en route for a trip is probably not the best time to let the flight crew find out the instrumentation and displays are not quite as they remembered. Most of the commercial training providers do not have the resources to address all possible flight deck retrofits during pilot training. Manufacturer-provided pilot handbooks can be a good source of operating instruction but adequate time spent with someone knowledgeable of the installation may be worth including in the sales contract and should be provided for maintenance personnel as well.
I recently had a salesman visit at my day job attempting to sell a new plug and play navigation display. My last dealings with plug and play equipment involved rewiring most of the plugs and playing around with the bloody thing for days before I could get it to work.
My advice when a question arises whether to retrofit, refurbish, or retire; get the biggest bottle of Tylenol and start doing your homework. Of course, retirement does present some interesting options. AMT
Jim Sparks has been in aviation for 30 years and is a licensed A&P. He is the manager of aviation maintenance for a private company with a fleet of light single engine aircraft, helicopters, and several types of business jets.
About the Author
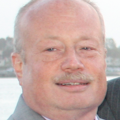
Jim Sparks
Jim Sparks has been maintaining aircraft for almost 40 years with the majority of the time involving Business Aviation activities. Jim’s endeavors have placed him on six of the seven continents contending with numerous situations from routine flight dispatch to critical AOGs. His career includes maintainer, avionics/electrician, educator, tech rep, and director of aircraft maintenance. In addition to other activities he is engaged with ASTM assisting in the global development of criteria defining the Next Tech for NEXTGEN. You can reach him at [email protected].