JANESVILLE, WI — After ten years of solid steady business at the Southern Wisconsin Regional Airport, Helicopter Specialties doubles its space and prepares to move into a new $1.65 million facility. Comments president Jim Freeman, “The success of our company has come from building trust with our customers by consistently delivering a quality product.”
A self-described entrepreneur who started with nothing more than his tools, a wirestamper, and a computer, Helicopter Specialties president Jim Freeman has built a stable helicopter maintenance and completion business that has outgrown it’s current 38-year old facility at the Southern Wisconsin Regional Airport.
Currently utilizing some 14,000 square feet, the new facility will double the company’s work and storage space to some 28,000 square feet. With 23 employees, 15 of which are licensed technicians, Helicopter Specialties is the largest employer on the field.
Services offered here include helicopter maintenance and inspections; custom completions and medical interiors; custom painting; avionics and airframe electrical installations; laser wire marking; structural repair; field support services; and helicopter parts sales.
A Diverse Customer Base
According to Freeman, the company’s customer base is varied, which plays a large role in the success of the business. Helicopter specialities serves a niche market that was once supported by Omniflight Helicopters, which moved its operations to Texas in 1993.
“I worked out of my home for Omniflight for another six years, explains Freeman.
“In the spring of 2000, I bid on a completion for a Pittsburgh company that included paint, interior, and avionics; I was previously just doing daily maintenance on its aircraft.”
That company accepted the bid, says Freeman, and he received the aircraft that June. He then went to work on it in a rented Quonset hut at the southern Wisconsin airport with a workforce of seven. “We started out with a small crew, and some weekend help,” remarks Freeman.
“By and large we did that first aircraft in six months; the Pittsburgh company was happy and gave us a second helicopter and ten months worth of work.”
Milwaukee Flight for Life owned the aircraft, says Freeman, and its operating vendor out of Pittsburgh started hiring Freeman for intermediate and heavy maintenance, and some refurbishment work.
“We quickly ran out of space in the Quonset hut and rented part of the old Omniflight facility,” relates Freeman.
Flight for Life, an emergency transport system that helps augment health care delivery systems on a local and regional level, is now one of the company’s primary customers.
“They have an operating vendor out of Denver that supplies the pilots and mechanics; we are part of their support package,” says Freeman.
The company also does work for Air Methods Corporation, based in Denver. Air Methods provides aircraft, pilots, mechanics, and support to hospitals nationwide, and it operates some 350 aircraft. Additionally, Helicopter Specialties services government customers out of Chicago, police and fire departments, the FBI, the DEA, and several private and corporate customers.
“Our customer base is varied; we are pretty diverse,” says Freeman. “Almost all of our business comes from referrals based on the quality of the work we do.”
Moving forward
“We work on the four major airframe manufacturers: Eurocopter, Bell; Engstrom; and Robinson; and we also work on McDonnel Douglas and Agusta helicopters,” says Freeman.
“We are getting ready to add a Turbomeca engine service center; a French engine.
“We also do a lot of custom fabricating. We’ve installed camera systems and built-from-scratch incubator systems for medical helicopters; as long as we can get it approved, we will custom build it.”
The new facility, which the company broke ground on last fall, came in at a cost of some $1.65 million, relates Freeman.
“We ordered the building last September; our contractor told us since last fall the price of steel has gone up five or six times,” he says.
“We built this building when we should have; the timing was right.”
Regarding the airport, Freeman comments, “It’s easy for customers to find; it is protected and secure; it is a nice airport aesthetically with two instrument approaches; and it’s located between two good-sized towns right off the highway.
“From a geographical standpoint, this is a nice place; and the land lease here, from what I understand, is one of the most affordable in the state.”
Freeman says his annual revenues are at some $3.5 million. “We are kind of a one stop shop, so if we grab a paint job, it could have some major maintenance with it, maybe some repair, then they may also want some avionics upgrades,” he explains.
“Between maintenance, repair, and avionics ... each profit center probably represents a third of the total business that comes in here.”
The new 28,125-square foot facility features a large expanse of skylighting, in-floor heat, and a 10,000 lb. bridge crane. Freeman expects to be in the facility in August.
With regard to possible future exploits for the company, Freeman remarks, “Brokerage would be nice; that’s a highly competitive and hard-to get-into business.
“Our goals are to keep our customer base diversified, expand our parts sales, possibly introduce some higher level flight training, and maybe some brokering, he says.”
Freeman relates that the company will continue custom manufacturing for aircraft, and pursuing STCs (supplemental type certificates) for its custom fabricating efforts.
Some solutions from Helicopter Specialties ...
• Stryker Stretcher with Custom Designed Isolette
The Need: Hospitals need to transport their tiniest patients safely in EMS helicopters.
The Solution: Helicopter Specialties designed a platform that mounts an Isolette and related life support systems to a Stryker Stretcher. The company worked closely with NICU (neonatal intensive care unit) personnel to custom-design the system.
* * *
• Custom-Made EMS Medwall with IV Warmer
The Need: A well-designed interior layout in an EMS helicopter is critical to the mission. A Bell 222 EMS helicopter needed a better way to utilize space for its equipment.
The Solution: The company designed a compact medical wall that combined provisions for: IV warmer, Oxygen, Air, Vacuum, Medical A/C, Drawer Storage, and ProPac monitor.
* * *
• Custom Floor Latch Mounts for Stryker Stretcher
The Need: The Stryker Stretcher needs to be latched down for use in an EMS Helicopter.
The Solution: A quick release latching mechanism that securely locks the rugged stretcher to the aircraft floor.
About the Author
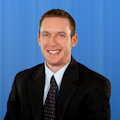