SAN DIEGO — As San Diego International Airport (SAN) embarks upon the largest improvement project in its 80-plus year history, AIRPORT BUSINESS sits with Green Build vice president of development Bryan Enarson to discuss the role sustainability and technology will play in the new terminal facility, and the extensive customer service enhancements that will result from the development. Facilitating the movement of some 17 million passengers in 2009, a figure that is expected to increase to some 30 million by 2030, Enarson relates that the new terminal and the addition of ten new gates at SAN is a much-needed improvement.
Having worked for San Diego hometown carrier Pacific Southwest Airlines beginning in 1970, Enarson is no stranger to this West Coast airport setting. He worked in the field for 12 years at different stations throughout California and landed at San Diego’s Lindbergh Field for good in 1981.
After going to work for the Port District (San Diego Airport operator at the time) in 1997, Enarson began as director of operations at the airport and moved on as director of the airport real estate group; he also took positions in marketing, public relations, facilities development, facilities maintenance, and now as VP of development for the airport’s Green Build project. SAN is currently owned and operated by the San Diego County Regional Airport Authority.
With a particular focus on sustainability, this development project includes the addition of ten new gates, a ‘Smart Curb’ curbside check-in, a dual-level roadway in front of the terminal, a doubling of security lanes to 12, and an expanded concessions area. All in all, the project will cost $1 billion ($865 million for the project and the remainder in financing costs) and will incorporate state-of-the-art baggage technology, open-space terminal design elements, and increased common-use functionality.
Remarks Enarson, “The economy will come back and San Diego will be positioned well because we’ll have the new facilities in place.
“The downtime is a good time to make improvements — so when the good times return, you’re ready for it. Overall it’s going to be a much better experience for the passenger.”
Sustainability, Technology
Environmentally, a big concern is traffic and the airport’s hydrocarbon footprint, says Enarson. The airport is moving to a single bus system, which will shorten the traffic distance for rental cars, and instead of individual buses for each rental car company, “We’ll have a single bus system going back and forth nonstop to the terminals,” he relates.
“That is something that is happening all around the country, and it’s happening because it’s more efficient and environmentally it’s the right thing to do.”
The airport is targeting LEED (Leadership in Energy and Environmental Design) Silver certification, comments Enarson. Project plans for incorporating sustainability into the new 445,000-square foot terminal complex are to employ the use of natural light, photovoltaic technology, landscaping measures, water conservation, electrical efficiency measures, and the use of reusable and sustainable materials in the building process.
“We are hitting the sustainability aspect from a lot of different directions,” says Enarson. “LEED has the criteria and gives us a good roadmap to follow.”
Other measures include regulating the type of contractor construction equipment by mandating filters on certain vehicles to mitigate emissions, and the utilization of electric vehicles.
Design plans call for the terminal entrance to be set back from the terminal curb, a dual level roadway to relieve curb-front traffic by separating arriving and departing passengers. Setting the structure back from the building will allow the airport to take full advantage of the terminal window wall, resulting in a great amount of natural daylighting, relates Enarson.
“The dual level roadway is long overdue here,” he says. “Separating the arrival and departure traffic is not only a customer service issue, but a safety issue as well. When you combine those two operations, at peak times you have a real suicide squeeze going on at the curb. This really allows us to separate that traffic and make for a much nicer experience for the customer.”
A ‘Smart Curb’ has been designed into the project that will allow customers to perform full check-in functionality before they enter the facility, including baggage.
“It cost another $120 million to provide the second-level roadway and the Smart Curb; it did add cost to the project, but at the end of the day it’s safer, more efficient, and improves the experience.”
Curbside baggage check will be facilitated by the automated movement of baggage from the curb underground to the baggage check and makeup, and out to the aircraft.
“We are totally in-line now, but you learn a lot,” comments Enarson. Enhancements to the airport’s baggage technology involve the kind of pushers used to sort bags. “There are ones that work better than others,” he says. “The pushers that push up and down don’t work as well; the original design on the new building was to use those pushers. We said we want side-to-side; we redesigned the system to accommodate side-to-side push-sorting.”
From an energy standpoint, electric motors in the back soak up great amounts of electricity, remarks Enarson, so the airport is installing high-efficiency motors. “A lot of these enhancements we are doing with the new system really cut costs and are more reliable,” he adds.
The new terminal will also incorporate common use passenger processing technology (CUPPS) at the ticket counters and gates.
“That allows us to have the kiosks for self-check in to be all common use,” explains Enarson. “That’s probably the most advanced feature for us because it’s going to give a lot of flexibility to the building. It’s nice to have these check-in modules everywhere, but if every airline has its proprietary system, it gets to be a jungle.
“When the airport provides the common-use system, we can locate kiosks in places where airlines wouldn’t be able to, and not have as many units.
“Having common-use functionality is a long-term gain for the carriers because it puts off when you have to build new facilities; you get a longer life out of the building.
“We are putting in a common backbone infrastructure that will be able to serve the other terminals as well,” he continues, “ ... because our goal is to gradually convert the rest of the buildings to common use.”
Facility Architecture
Comments Enarson, “The fact that we are expanding the big building [existing Terminal 2 West] and continuing with the more spacious look that is more comfortable for the customer, the security checkpoint is going to be twice as big as the one we have now.
“That’s huge for passengers; our goal is to keep the average security wait time down to ten or 11 minutes.”
Emulating the existing architecture of Terminal 2 (T2), the airport will employ large amounts of glass and open space. Wind, sand, and sea is the design element theme in terms of colors; “We carried those design elements into the new building with the same architectural approach,” adds Enarson.
“The covers above the smart curb emulate what the convention center here has — that’s part of the San Diego experience. If anything, we are enhancing what we feel was done well with T2.”
With regard to concessions, the airport will grow from 75,000 square feet of retail and concession space to more than 149,000 square feet.
Relates Enarson, “The concession hall will be the signature piece of the expansion, and will be identified as Sunset Cove,” a 300-foot long and two and a half story high, all-glass area looking out to the west. “It will be very impressive, and a neat place for people to go and relax,” he adds.
In terms of concessions location, “We still have quite a bit of pre-security concessions,” he says. “A lot of meeter and greeters come here; however the majority of that development will be located post security.”
Design/Build Contracting
“Design/build gives you the ability to shorten the timeframe up a bit, and allows you to design and build at the same time,” explains Enarson. “With design/bid/build, you design everything 100 percent, then bid and start building. If you find you have to make changes, speed up the schedule, or modify the design, the process can affect the schedule, and the budget.”
Enarson says the airport is taking full advantage of the bidding market, and that everything is coming in 20 and 30 percent below estimates due to a very competitive market place. “It is a good time for us to develop this project; it’s the best time to build,” he adds. “We are getting the biggest bang for our buck right now.”
The Green Build program is divided into two joint venture packages:
• Contract 1 work (led by Turner/PCL/Flatiron) will include ten new jet gates, expanded dining and shopping options, as well as terminal and airfield improvements.
• Contract 2 work (led by Kiewit/Sundt) will include construction of roadways, parking lots, elevated departure curbs (Smart Curb), and buildings and bridges.
With regard to concession contracting, the airport is moving to a contracting model that utilizes multiple primes in individual units, going away from the single retail/concession prime contractor. The Green Build also incorporates more of a local flavor with regard to the concessionaires, relates Enarson.
“Our board made a commitment to keep as much of the project as local as we can,” he says. “Not only is it an advantage in the program to be in the marketplace right now because construction costs are more competitive, but it’s also a time when the region needs the jobs. We will be up to 1,000 jobs at the midpoint of construction for this project [2011/2012].
“Instead of letting out a single contract for pieces of work, we’re breaking it down so we give opportunity to the smaller local contractors who can’t bid on a large dollar piece.
“ ... And we are not only just breaking it down, we are actively reaching out to local contractors. We go out and meet with the different contracting agencies, and have been hosting open-house events so they can better understand how to do business with us.
“We also have a bonding program where a small contractor who couldn’t get the necessary bond to work here — we would underwrite that bond. We are a supporter and underwriter of the Turner School of Construction Management. That brings in small contractors and helps them understand the construction process.”
Selling the stakeholders
“Airlines spend a lot of time in airports telling them not to build anything because of where the economy is,” remarks Enarson. “One of the things that was happening before the downturn was we were totally full; our 41 gates were occupied and we’d have anywhere from 14 and 16 planes per night that couldn’t get a gate.
“Carriers knew we needed the facility, and they know San Diego is a strong market — they are running more than an 85 percent load factor here. They support the development and support moving forward with the additional ten gates.”
Enarson says the airport did something that is fairly unique in the industry, at least to this degree, with regard to stakeholder outreach.
“We began programmatic design for the terminal almost four years ago — during that we spent a year where we brought in all of the stakeholders ... airlines, concessionaires, internal and external stakeholders that use the airport ... and got their take on what they wanted to see, and what they didn’t want to see,” explains Enarson.
“Do we always agree, no — but do we keep open communication, yes.”
SAN provides a residual lease structure on the airfield and compensatory on the terminal .
“We are going to more of a commercial compensatory,” says Enarson. “We basically get all of the revenues and the airlines only pay for the space that they use, then we make up the difference by paying for the other space.”
The cost per enplaned passenger here is currently $6.50/$6.60. When the terminal is complete, that rate will rise to somewhere between $10 and $11, he adds.
The lease term length here is usually five years, or no agreement at all, relates Enarson. “If your market is really strong the airport can say we don’t need an agreement … because if a carrier leaves, another will come in,” he says.
“For the bond market, having a five-year commitment from the airlines makes the finance people feel better.
“In San Diego we have a very diverse carrier base; we have a five-year common-use agreement. It keeps the airport stable, and in our market we can get away with that.”
Funding; Future
The Green Build will be paid for with airport revenues, passenger facility charges, grants from the federal government and elsewhere, and bonds, according to Enarson. “We are out on the market right now to borrow,” he says. “Airports are having a tough time with that right now because the economy is not real good. We were fortunate and had our ratings redone, and we pretty much stayed where we were — stable. We will see what interest rate we are able to get; we are targeting 6 percent, but I think we will probably do better than that.”’
In terms of future challenges, Enarson says the airport’s biggest problem is going to be, as time goes on and as the airport gets busier, having no room to grow. The airport is located on 660 acres and is landlocked by the bay on one side, the Pacific Highway on another, the U.S. Marines to the north, and city development on the West.
“We have pretty much all the land available to us under our control,” comments Enarson. “So the challenge is really going to be long-term in how we’re going to be able to deal with growth.
“This airport was originally a 100-year solution in 1928; there will need to be a new 100-year solution soon.”
FAST FACTS
San Diego International Airport/ Lindbergh Field (SAN)
Acres: 660 (Landlocked)
Single Runway: 9,401 feet in length and 200 feet in width.
• Congestion anticipated when annual aircraft operations reach between 260,000 to 300,000 (30 percent above current levels).
Passengers: 16.9 million annually (2009); 27 to 33 million expected by 2030.
• 1,605,790 passengers (August 2010).
Employees: Some 4,900.
Carriers: 17 passenger and four cargo; 90 percent origin and destination market.
• Market share leader in terms of passengers is Southwest Airlines (37.3 percent).
Cost per enplaned passenger: $6.50/$6.60.
Load factor: Some 85 percent.
Facility: 41 gates in two terminals; commuter terminal provides four gates.
Fixed base operator: Landmark Aviation
The San Diego Airport Authority has developed a public art master plan which will be implemented in three phases over seven years. The plan will result in a collection of artworks that blend with building design and infrastructure
throughout The Green Build process.
Policies provide for two percent of the budget for eligible construction projects to be allocated for public art; artistic elements will be added to both existing airport facilities and future construction projects such as terminals, roadways, and connecting green spaces.
The Green Build includes three significant public art projects:
• The Multisensory Journey: Charges the artist with creating a multisensory experience that extends the entire length of the new terminal expansion and functions as an intuitive way-finding element.
• The Suspended Artwork: Under this project, the artist will create an artistic statement that will hover over and integrate into the concessions area. The suspended artwork will span multiple levels and be visually accessible from numerous perspectives.
• The Terminal Elevators: The terminal includes a set of two glass-enclosed elevators in the concessions area. As an integral component of The Green Build, the opportunity charges the artist with creating an experience and way-finding element that serves as a beacon ascending multiple levels — arrivals, departures, and concessions.
Green Build Timeline
2009 — Construction began on apron improvements, additional aircraft parking, and new United Service Organization (USO) facilities.
2010 — Terminal and dual-level roadway construction began; portion of Terminal 2 parking relocated; Terminal 2 East and West pedestrian bridges removed; frequent shuttles transport passengers to terminal.
2011 — All of Terminal 2 parking relocated.
2012 — Terminal and dual-level roadway construction continues.
Early 2013 — New gates, facilities, and roadway improvements open to the public.
* * *
• The new USO center will be the largest airport USO center in the nation; some 100,000 service members and their families travel through SAN each year.
About the Author
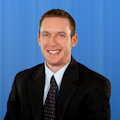