Wireless fleet optimization technology has emerged with the promise of many benefits for managers — more efficient and cost-effective operations, enhanced user accountability, safer and more secure ramp operations — to name a few. Ground Support Worldwide takes a look at the basics of the technology and speaks to customers who have made the investment in their ramp operations.
The Technology: Key Features
The systems are generally comprised of a vehicle tracking unit installed on each vehicle and a central data server. Manufacturers claim the features of the system — which users can largely customize to fit a specific operation — can lead to overall cost-cutting and more efficient operations in some key areas:
Fleet utilization: GPS enables real-time visibility of equipment locations; two-way text messaging capabilities allow for instant communication between ramp employees and managers; additional features can allow for dispatch of work assignments; real-time vehicle reporting can communicate fluid levels, driver behavior and engine status.
Maintenance: reports on equipment usage can help schedule preventative maintenance inspections on vehicles.
Safety and security: features allow for restricted access to only authorized users through badge-screening or login technology; “geo-fencing” features allow vehicles to be used only in designated areas; safety checklists prompt users to fill out the condition of a unit before it’s used.
Customer Expectation
These key benefits are what interested Air Canada Cargo in a wireless fleet optimization system. It has decided to try the fleet optimization program iRamp, developed by Katlyn International Inc., for its operations in Toronto. It has recently installed the system on six tractors to run a trial for six months.
For Air Canada Cargo, the ability to track the location of a vehicle, according to Peter Ayearst, GSE manager, cargo, North America at Air Canada Cargo, was a major attraction. “It’s hard to know exactly where your equipment is at all times,” he says. “Not only that, but also who is driving the vehicle. Sometimes we have damage on our vehicles, and we don’t know how it happened or who had it last.”
Another major draw to the technology was the automatic data collection of vehicle usage. “Now it’s a manual task to grab those and manually input it. [iRamp] offers automatic collection that would get data at the end of the day or every time the vehicle comes through the building. So we’ll take that information and schedule our PMI inspections based on the hour meters.”
Ayearst continues, “You also have positive feedback for the driver for daily inspections. We have our daily inspections listed in the iRamp module.
“You can also look at your fleet utilization — do you have the right numbers, the right mix? Whether you have too many vehicles or not enough, it certainly would help make your case, depending which way you’re going,” he says.
With the ability to communicate work assignments instantly to employees on the ramp, Ayearst believes it will lead to more efficient operations overall. “It’s one thing having a radio in your vehicle, but to actually have this kind of information on the display screen on the vehicle, it’s almost like taking your warehouse and putting it in the vehicle with your operator. You can see real-time gate changes, which flights have cargo, you can even do work assignments on the go,” he says, adding, “There are long distances involved between the passenger terminals and the cargo facility. If an employee is over there and you want him to turn around and go back to pick up, he can access the task list.”
Ayearst says the six-month trial will determine if and to what extent the iRamp technology will be rolled out into the fleet. “Certainly if it lives up to its promise, there is an awful lot in there in savings,” he says.
And that’s just the reason Katlyn International, a company based in Canada, began developing the iRamp system about two years ago. The system transmits data through cellular communications. With Air Canada Cargo as its first customer of the iRamp system, the company has hoped the technology will catch on throughout the industry.
American Experience
While some airlines have started to test this technology, another airline has implemented a system at one hub location and recently announced plans to expand to a second.
American Eagle installed the AvRamp wireless vehicle management system, by I.D. Systems Inc., at its DFW hub in October on about 100 tractors.
Larry Terrazas, vice president of customer service policy and planning, said he has been able to right-size the GSE fleet at its DFW hub. “There was never a good way of tracking how many pieces are active at any given point in the day and what the peak requirements are,” he says. “We have been able to find that we have surplus equipment in DFW that we’re going to be able to use in future station openings throughout the system in this coming year. So instead of having to go out and buy new equipment, we are just going redeploy what we have as surplus in the hub locations.”
On the maintenance side, Terrazas says that such features as the pre-use safety checklist has driven quicker maintenance on units that need it. “Prior to having the system, we were doing that same type of checklist but it was on a paper basis, so they may identify something — a tire that needs to be checked — but it may be a few days before that paper makes its way from the ground support shop. Then they assign that work to the technician to go out and check that tire. Right in the beginning [with the AvRamp system], it was instantaneous where minor repairs were communicated as people were noting items on all of these vehicles.”
Additional features, such as an engine idling option, have proven significant for operations. “We have an auto-shutdown feature enabled, so if a driver gets off the vehicle after 15 minutes of idle time, it will power off to save that fuel,” he says.
According to Terrazas, the system has been well received overall by employees on the ramp, saying that such features as the security and use-of-the-day checklist have helped create an atmosphere of safety. It has also ensured that employees can lock a vehicle if it isn’t in use. “It was a huge bone of contention. Every day that you would go out and get into a tractor, but when you go into a breakroom to get a new assignment or you take your lunch break, you didn’t know if that tractor would still be there when you came out. You didn’t know if one of your coworkers would jump on the tractor before you returned, so the AvRamp system helped them to lock the vehicle,” he says.
As for the next phase of the technology at the DFW location, Terrazas says the carrier is installing AvRamp on about 20 on-road vehicles, including passenger vans and pickup trucks. It has been coordinating the AvRamp system with its existing preventative maintenance planning product to further utilize the recording of vehicle usage. “Today we do a PM on a tractor every 60 days. We may find in that 60-day period, that tractor was only in motion 70 percent of the time,” he says. “So we really feel we will be able to do a better job of doing our preventative maintenance checks and probably eliminate some of what is being done today on vehicles that really didn’t need it.”
And American Eagle recently announced it would rollout the technology at its Chicago O’Hare hub on about 120 vehicles. The project should begin sometime in March and the airline believes it will reap many of the same benefits that it has experienced at DFW, Terrazas says.
Asked as to whether the system could be rolled out at additional locations, he says there is a possibility at its other hub locations such as LAX and JFK. “It really has its biggest bang for the buck at hub locations where we have large numbers of equipment and dedicated ground support technicians to maintain those,” he says. But for now, the carrier is focused on utilizing the data capabilities to the fullest. “The biggest piece for us right now is to get this wealth of data we’re collecting and making good analytical decisions off of that,” he says.
The AvRamp technology was developed in partnership with the TSA. The product is billed as “Wi-free,” with the transmission of data being sent through small communication nodes installed around the airport. With American Eagle as the company’s first airline customer, I.D. Systems has focused on increasing its North American customer base.
The International Arena
Wireless fleet optimization technology has gained traction in the international market. A number of fleets at European airports have implemented the Airport Visualiser wireless technology by Zebra Enterprise Solutions for its ramp operations, including Munich, Heathrow, Schiphol, and Madrid international airports. It has also been implemented by Abu Dhabi Airport Services and Singapore Airport Terminal Services.
Singapore Airport Terminal Services implemented the Airport Visualiser in 2006 as a pilot on its container loaders at Singapore Changi Airport. The trial showed the company needed seven fewer loaders in operation. In 2007, the company decided to roll out the system on 340 units, including main deck loaders, passenger steps and baggage tractors.
According to Karmjit Singh, consultant to president/CEO at SATS, the system allows for a heightened level of transparency in its resources. “Asset productivity was the main outcome because operations could be as efficiently handled with fewer assets and resources,” he says. “The transparency of ramp/baggage operations improved and the operations controllers are able to make better real time decisions for tactical deployment of [container loaders] and other GSE based on the very dynamic flight changes daily. GSE maintenance benefitted, because real-time monitoring of fleet utilization enabled better scheduling for preventive maintenance instead of maintenance based on fixed schedules.”
Singh also says the employees have come to rely on the technology. “Like all new IT projects, staff are always skeptical initially,” he says, “but through proper education and frequent communication, staff realized the benefits operationally.
“The duty controllers now are so dependant on the system for better quality decision making and timely GSE deployment,” he says, “that they won’t want to go back to the legacy system operating with ‘blind spots.’”
He adds, “hoarding’ of GSE, in preparation especially for peak operations, used to create an artificial shortage of GSE; this is not necessary now because the location of GSE is known and timely deployment is the essence of operations.”
As for the future rollout at additional airport locations, Singh predicts the company’s larger joint-venture partners at separate locations will likely take a cue from the program at Changi Airport. “The larger JVs themselves will make their own decisions and learn from SATS headquarter’s experience — it is a matter of time that the larger JVs may follow suit,” he says.
The Airport Visualiser transmits and receives data either using standard WiFi (802.11 B/G) or standard GPRS data communications via the public network. Additionally, the 24730 standard is supported to send information to a very sparse number of 24730 base stations. The program is being sold worldwide, but Zebra Enterprise Solutions has been focused on increasing its European and Asian customer base.
Fleet Implementation
As with any large-scale installation project, the implementation process does require considerable planning on the part of the customer. For American Eagle’s implementation of the AvRamp system at DFW, the carrier coordinated the rollout with the permission of the airport authority, a process that took a few months.
Zebra Enterprise says that the implementation process can be largely a waiting game. “What we have noticed is there can be a waiting period,” says Frank Kooijman, vice president of equipment fleet management products at Zebra Enterprise Solutions. “Obviously, if it’s an airport, you don’t let planes wait because the equipment is being serviced. That can sometimes create fairly long waiting times that you need to schedule in your plan.”
The Future of Wireless Technology
All three technology companies have expressed a desire to increase the interoperability of their technology with other airport systems. Just how widely used such technology will become, especially in the North American market, remains to be seen. One thing is for certain: Technology will continue to revolutionize the ramp.
About the Author
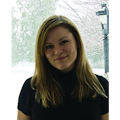