At its largest hub at Hartsfield-Jackson Atlanta International Airport, the Delta Air Lines central GSE facility is located just outside the AOA, offering a respite from the flurry of operations on the other side of the fence. The 150,000-square-foot facility has all the makings of a GSE shop — but in a much grander scale than most.
The open, spacious shop floor has multiple, neatly organized bays for servicing equipment. The facility also has designated sections needed for maintaining GSE, including areas for painting, rebuilding and an extensive parts inventory. Above the shop inside the offices located at the facility, much of the planning and related activity for GSE is implemented.
As the main GSE shop at the carrier’s largest hub, it has been equipped to support many units — about 2,500 pieces of motorized GSE and 6,000 pieces of non-motorized GSE, which includes PCA and ground power at its 125 bridges. Also under its responsibility have been four baggage sortation systems at the airport, and about 16,000 ULDs.
A STAR Site
Safety has been a paramount goal at the facility — an objective made apparent by the facility’s OSHA Voluntary Protections Program (VPP) certification, which it first received in May 2001. It was recertified in 2004 and 2007.
Referred to as a VPP STAR site, the focus of the facility — based on the components of the VPP program — includes management leadership and employee involvement; worksite analysis, hazard prevention; and control safety and health training.
“VPP is a high-level safety management system and the program goes beyond the minimum compliance expectation,” says Morgan Durrant, spokesman at Delta. “Management commits to operate an effective safety management system. Employees agree to participate in the program and work with management to ensure a safe and healthy workplace. OSHA periodically reevaluates the participant to confirm its continuing qualification for VPP.”
He adds, “STAR sites have injury rates that are below the industry average. When a site implements each element effectively, the result is a safer workplace for our employees.”
Maintenance Capability
Among the employees at the central facility include 104 mechanics that work to maintain equipment. This is in addition to about 120 mechanics at its two other shops located at the airport. Also, about 10 mechanics are on the road to support 25 stations in the surrounding the regions.
The carrier has a structured training program in place for mechanics. With two classifications for personnel, ground maintenance mechanic and ground maintenance technician, new staff members are given a set training regimen.
“Every GMM and GMT when they come through the door has a certain number of courses that they have to take based on their classification,” explains Mike Maier, regional manager of GSE at Delta. “There are also home study courses that they are required to complete, on their own time during the first six months. These courses are basic electrical, hydraulics, pneumatics, refrigeration, and welding.
“Once they complete those courses there is a whole series of different training courses that we teach on the manufacturers’ equipment,” he says, adding that staff are given recurrent training as well.
To keep the equipment on track with preventative maintenance inspections, the staff performs service on an hours-based program. And to make sure that parts are on hand when needed, the facility houses about $1.2 million in parts inventory.
When it comes to rebuilding its GSE, the staff has undertaken some projects, including rebuilding C-6 transmissions on as-needed basis. Joe Fuqua, general manager of GSE at Delta, says the airline is looking into possibly refurbishing some pushback units with obsolete engines.
GSE Planning
In maintaining its entire network of GSE, consisting of more than 100,000 units (which includes motorized and non-motorized GSE, stationary equipment, scales, as well as conveyor sections from baggage systems throughout the world), the facility in Atlanta has played an important role. The top floor of the facility is abuzz as units are tracked and allocated throughout the world.
With so many pieces of GSE throughout its network –—and the added pressures of flight schedule changes at various airport locations — Delta relies, in large part, on a couple separate software systems.
To keep track of its inventory, the carrier uses EBis GSE Express by DatcoMedia, which houses information for the main carrier, Delta Global Services and Regional Elite.
“We can see everything by equipment type within a city,” says Anthony Kloehs, system manager — GSE assets & maintenance programs at Delta. “Basically, it’s a big inventory database.
“From there we are able to create work orders and use it for the maintenance side of the program. And from there we generate preventative maintenance schedules,” he says, relating, “We are watching every single city around the world for their maintenance.”
He adds, “We are getting ready to transition to where we will be buying parts through it, and utilizing the capabilities of that to go out and look at a couple companies, and bring back the parts, estimated delivery times and let the mechanic make that decision on price, delivery, operational requirement. That’s the big step for next year.”
Flight schedules being what they are, the GSE needs of each station around the world can vary as schedules fluctuate. To properly allocate equipment at different stations, Kloehs says the carrier uses software by Sabre Airline Solutions. “We are about three months ahead looking out at the proposed schedule to see if any of their peaks have changed: peak departures, but also within those peaks, the different fleet types also,” he says.
Merger
The merger of Delta with Northwest Airlines introduced many additional pieces of equipment into its network, bringing it to the current estimate of more than 100,000 units system-wide.
“With the merger, we’re at more than 100,000 pieces,” Fuqua says. “Before the merger, we were at approximately 55,000 to 60,000, so we’ve not quite doubled.”
Along with allocating and maintaining the additional equipment, another challenge came in the form of painting the units to reflect the Delta name. “The biggest piece was getting all the equipment together, getting it branded appropriately, which we are still trying to do,” Fuqua says.
“Our next attempt right now is that we’re bringing the Regional Elite airline’s equipment into the fold,” he says. “We’ve got that equipment coming in, and we’re trying to get it painted and branded appropriately, and that’s an ongoing challenge. That will add to the more than 100,000 pieces out there.”
GSE purchasing
Delta has made clear it will continue to purchase new equipment. In what was a sign of an upswing in the industry, the carrier recently announced that it would spend about $50 million for new GSE, with an initial order worth $14.5 million for deicers, which it began accepting in November.
According to Kloehs, the funds will be used to acquire many different types of equipment, including bag tugs, pushback tractors, container loaders, towbarless tractors and cabin service trucks. The total number of units purchased will be about 600, which will include 100 electric units.
When it comes to purchasing by fuel type, the goal is electric, according to Fuqua. “Whenever possible we purchase electric equipment. There are a couple of guidelines around the electric equipment. For instance, the city has to have the infrastructure to support it, if they don’t have sufficient power to run a charger, we can’t put it in there. If they can, that’s our first choice,” he says.
Delta recently completed the conversion of one its container loaders in Atlanta. Fuqua says there is a possibility that the airline will continue to convert more of its units to electric in the future.
About the Author
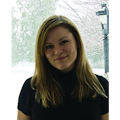