COLUMBUS, OH - Situated in the Ohio Valley, Rickenbacker International Airport (LCK) is within a ten-hour truck drive to more than 50 percent of the U.S. and Canadian population and some 61 percent of the U.S. manufacturing capacity.
The airport's location has made it an attractive place to do business for many importers, exporters, and logistics providers. Key companies with established warehouses and distribution centers in the area include Abercrombie & Fitch, Bath & Body Works, Eddie Bauer, Gap, Limited Brands, Rolls-Royce, Target, Whirlpool, and Xerox just to name a few.
Area logistics providers include Atlas Air, DHL, FedEx, Forward Air Corporation, and UPS.
The airport is also located adjecent to two major national rail lines that ship goods from the East Coast to the Midwest, where they are then distributed from here throughout middle-America.
Already a cargo-dedicated airport, the idea is to position Rickenbacker as a mutlimodal logistics hub by collaboriating with its base of air, road, and rail transport companies - supported by a mix of freight forwarders, consolidators, Customs brokers, and third-party logistics providers - and transforming the airport into an international logistics center aimed at enhancing economic growth for the region. Along the way, the airport will become something it has never been - self-sustaining.
Remarks Elaine Roberts, Columbus Regional Airport Authority president and CEO, "The projection is that we will have more than 100 million square feet of distribution space, coupled with our location, a rail-truck intermodal terminal, the cargo airport … we will have a true inland port that will help spin off more and more of this growth and development.”
The Rickenbacker opportunity
When Roberts came here in 2000, the Columbus Airport Authority did not have responsibility for operating LCK. Within six months of her arrival, the suggestion was made to look at a merger study for the two port authorities; Rickenbacker was operated by its own airport authority.
"We took over Rickenbacker in 2003," relates Roberts. "Columbus has always been talked about as an inland port because we have the high-grade highway access and location for distribution, logistics facilities, and a large dedicated cargo airport in Rickenbacker.
"The challenge with the authority merger for anybody operating Rickenbacker was, how do you make it self-sufficient?" The airport had been heavily subsidized by the county, says Roberts.
The county was losing some $5 million per year on LCK. When the merger study was done, the conclusion was without merging, LCK would cost the county some $56 million for ten more years; with the merger, that loss would be cut down to about $43 million, with the assumption that there will be a strategy put in place to eliminate any further loss.
"The county pays us $4.3 million per year … we’ve paid off all of the debt and lowered the operating deficit to about $250,000 per year," comments Roberts. "The biggest challenge in the future will continue to be capital ... you’ve got old military facilities; you’ve got two huge runways.
"Rickenbacker will never break even on just cargo activity because FedEx, UPS, DHL … those guys all have their own hubs, and they are shrinking their hub networks. So we are more of a regional spoke into those major hubs; FedEx is our biggest at some 75 percent of our cargo activity."
Developing a strategy
Benefits of Rickenbacker include more than 200,000 square feet of cargo facility space, 130 acres of uncongested cargo ramp, two parallel 12,000-foot runways, on site U.S. CBP, and the regional hubs of FedEx Air, FedEx Ground, and UPS. Major rail providers, Norfolk Southern and CSX, connect to all major East and West Coast ports. LCK also home to national raod feeder hubs of major trucking companies such as CEVA Ground, Town Air Frieght, and Team Worldwide.
"The first thing we had to do after the merger was figure out how we were going to turn this thing around," relates Roberts.
"Our best approach for making Rickenbacker self-sufficient is to do some non-traditional development ... so we partnered with the railroad to build a rail-truck intermodal terminal on airport property, and that along with the runways and highway access, is going to make this a really attractive place for development.
"The railroad needs more intermodal capacity here in Columbus because the demand is there for it. More importantly, we wanted to be a part of a bigger project called the Heartland Corridor."
The Heartland Corridor
Instead of having to bring goods from off the ships at Norfolk up through Pennsylvania and across northern Ohio, by creating the Heartland Corridor, the railroad can take a couple days off the shipping time, says Roberts.
The Heartland Corridor already existed, but it’s a single-stack rail line that is forced to take longer routes ... the Corridor project was to spend some $250 million raising bridges and lowering track so that trains could operate double-stacked. The Corridor goes across Virginia, through southern West Virginia, and north through the LCK Intermodal Terminal to Chicago; the project was completed a year ago.
The $68.5 million Intermodal Terminal occupies some 175 acres and has the capacity to handle more than 250,000 containters and trailers annually. Six trains daily - four between LCK and Chicago and two between LCK and Norfolk, VA - serve the terminal, which is considered one of the largest integrated logistics complexes in the U.S.
The airport was able to get some $30 million in Federal funds for the terminal; the railroad matched the other half and managed the construction. The project was completed in 2008.
A related project is scheduled to occur in 2014 - the Panama Canal Project. The canal will be widened and deepened so that large container ships out of Asia can come through the Panama Canal up to the East Coast of the U.S., and not have to stop in the West Coast as they do now.
"So 2014 will be another significant milestone for us … the Corridor is now opened double-stacked, the rail intermodal facility is built on-airport, the collective leadership in our business community and our regional planning commission is in place, and we’ve all been working together to improve major roadways around the airport," explains Roberts.
A multi-modal solution
"The thing that many of us on the airport side didn’t appreciate or understand … you do not usually see cargo moving between an airplane and a train," relates Roberts. "So when we talk about multi-modal and having an intermodal facility … it’s having all of these capabilities in one location.
"We got 1,000-acres of land approved from FAA for release … that is the seed to start a development called the Rickenbacker Global Logistics Park, the brand name for our industrial development."
The arrangement with the airport developer is like a joint-venture, she adds. "We brought the land to the table, they develop it and market it, and then we sell it off.
"Most airport managers may tell you that you don’t want to sell off your land - from an industrial development standpoint, the buildings never had a higher value than when they are first completed and have 100 percent tax abatement, etc … so by selling them off, we get our land money up front, the developer gets its cost of building, and then we have a provision to get 30 percent of what’s left.
"That money goes into kind of a savings account … we are going to put that money into this endowment and invest it, and use that money to help build things that will be self-supporting for the airport."
The intermodal terminal was the key piece that differentiates the airport from any other airport that can handle air cargo, remarks Roberts. "Our geographic location, the state of Ohio, is ideal for logistics and distribution … then you put a rail-truck facility adjacent to major highways and two main rail lines … and now we have double-stack clearance to the deepest seaport on the East Coast."
In terms of community engagement in the initiative, "The role is very big now … initially we helped drive it because it was on our land and we were the catalyst to get it started," says Roberts. "There was an economic impact study done that said roughly 30,000 jobs would be created over 20 years; getting community support, both local and Federal, was critical.
Lease arrangements
The airport authority negotiated a long-term lease with the Norfolk Southern Railroad that is a little complicated because the airport owned about half of the land and the rail line owned the other, says Roberts. "The rail really needed the land adjacent to the tracks … so we’ve done some land swapping. We get ground rent from them, and we get a commission based on the volume of containers going through there.
"Then we, at the same time, started looking at the access land … so the railroad’s involvement in the rent and the fees coming from the intermodal industrial development – those were the big pieces of our strategy to say this is how we make this airport self-sufficient."
Right now, because of current market conditions, central-Ohio has a high vacancy rate of some 15-18 percent in the industrial market, explains Roberts.
"Our development partner is a joint-venture between Duke Reality, headquartered in Indianapolis, and Capital Square based here in Columbus. There is a master development agreement with the airport authority - our land, their development expertise and marketing; our land has been valued and is in the deal at various costs per-acre.
"The land will probably take another 15-20 years to be developed completely, but our long-term projection is $75-100 million would be the airport share if all of this is developed. That’s the money that is going to help us maintain, build, and take care of the airport."
About the Author
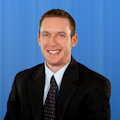