G&T Conveyor Company, based in Tavares, FL (45 minutes north of Orlando International Airport), is the only privately-held American-owned and operated baggage handling solutions company in the U.S. Specializing in sortation and in-line EDS (explosive detection system) integration, G&T engineers, manufactures, and installs baggage handling systems (BHS) primarily for airports in the U.S., although the company has worked on projects in the Caribbean, Dominican Republic, Mexico, and South America.
Explains G&T's Martin Ineichen, who has been in the baggage handling business for some 20 years, "We have our own manufacturing plant; we actually manufacture all of our equipment ourselves. We buy raw material and turn it into conveyor sections; we assemble everything in-house, we test everything in-house, and we have our own development group."
The baggage industry has been changing rapidly since 9/11; airports want to get more bags through the system, meaning a higher throughput and faster, more accurate machines - that creates some challenges," he adds.
FLL Project Scope
G&T was selected to engineer, manufacture, and install the BHS for the Ft Lauderdale-Hollywood International Airport (FLL). Project demands included installing 7,100-linear feet of conveyor, 685 drives, five new make up units, ten G&T Vertical Sorters, and 22 G&T Power Face Diverters. Additionally, G&T integrated the BHS with eight L3 6600 EDS machines.
Comments Ineichen, project manager for the FLL install, "The process for winning a bid is very similar on each project … systems get designed by a consultant and are put on the street for competitive bid.
"An advantage that we bring to the table is that we are very close geographically to the airport … less than three and a half hours away. That makes delivery of our equipment ‘just-in-time’; we can react to changes much faster because our engineering staff is nearby."
G&T put in a system at Fort Lauderdale in the same terminal some ten years ago, so the airport is familiar with the company's equipment, relates Ineichen. After winning the bid, the next step was to review the design drawings to see if there were any enhancements, adjustments, or reductions that could be made. "We did make some recommendations; it’s not as though we scrutinize the designs … we are just looking at it in a ‘what makes sense’ kind of way."
For this particular project (Terminal 1), the previous system installation process was very simple - there was a baggage input at the ticket counter that went down to a baggage make-up unit, he remarks.
"Today, there are mezzanines; there are platforms; there are four layers of conveyor belts," says Ineichen. "The ceiling height is 35-foot, and all of that is being taken up by the new system.
"It is really a system unlike anything I have seen; it’s one of the most impressive systems I have been involved with."
With regard to the contract holder, sometimes it's the airport direct and sometimes it’s the construction consultant, relates Ineichen. In this case, Southwest Airlines (end-user) was the construction manager; G&T's contract was with Southwest.G&T was asked by Southwest some six months into the project to take over as the engineer of record.
"The airlines and the end-user have all of the vested interest in working with baggage handling contractors in a situation like this," comments Ineichen.
Challenges; solutions
Southwest utilizes the majority of Terminal 1. Recently, Air Tran's ticket counters have come over to the terminal. On the other side of the facility is Allegiant, Virgin America, Continental, and various charter operators.
On a weekend, when all of the cruise lines come in, the aiport experiences a tremendous amount of passengers checking in bags between 8 a.m. to 2 p.m. The entire ticket counter floor area is wall to wall people during this time … and that happens every weekend, says Ineichen.
"What is so different about this system is there is a total of 7,100-linear feet of conveyor and 685 motors," he relates.
"At this particular airport, the architecture of the bag room created some big challenges because a typical system is connected to the bag room ceiling. At FLL, the framing was not able to hold the weight of the system, so an entire sub-grid had to be installed throughout.
"On top of that, the spans were so big that we had to come up with something very unique. That’s why there are huge hanging platforms in the bag room [9,330-square feet of platform space]. They are supported with massive columns that are connected to the grid pattern."
Despite some 7,000-feet of conveyor, there is nearly unlimited physical access to any part of the system, says Ineichen. "People can walk upright anywhere in this system; from a maintenance standpoint, that is a tremendous advantage."
From a control standpoint, Ineichen explains that the entire system is DeviceNet (a network system used in the automation industry to interconnect control devices for data exchange), which is something the industry moving more and more to.
"It is very maintenance friendly, easy to control, and easy to troubleshoot," comments Ineichen. "Even from an installation point-of-view, nearly everything in the system is quick-disconnect; from a maintenance point-of-view, it is very easy service the system."
Another challenge was installing the system in a live operating airport environment.
Says Ineichen, "Terminal 1 is an operating terminal, so there was only a short period of time each day when there was no activity going on; that's when we had full-access." The system was installed, certified, and activated in a 20-month period.
Throughput, lifecycle
The system was divided into the east and west side of the terminal; each side has four L-3 6600 explosive detection machines, and each machine can process 450 bags per hour.
Currently during peak hours, the airport is processing 1,300 to 1,800 bags per hour on each side of the terminal. The system is designed so that if in the future a faster screening machine is developed, the system can integrate the new units easily, says Ineichen.
"Everything in a tracked zone is VFD (variable-frequency drive) controlled, which allows for an increase in speeds. This allows for flexibility; we try to design into a system as much flexibility as possible."
In terms of the ongoing maintenance, since Broward County has its own maintenance department, it has taken over the operational and maintenance contract of the system; the technicians have been trained by G&T and Brock Solution, the controls contractor, relates Ineichen.
With regard to system lifecycle, "If you’re looking at how the industry evolves, the lifecycle of an x-ray screening machine is anywhere from five to ten years, he says. "On the baggage handling portion, we have seen some of our systems last as long as 25 years.
"That all depends on how the maintenance is being performed; if recommendations are followed and the system is maintained well, it can last 20 years easily."
The future of BHS
Baggage handling systems (BHS) prior to 9/11 were entirely different because pre 9/11, there was no screening requirement, says G&T's Ineichen. The key at that time was providing the shortest route for a bag from the input point to a make-up device.
"Now, you have this new requirement; if you break it down, there are three elements: the x-ray machine every bag must go through; TSA has to make a decision on any bag that is suspect, meaning a human intervention; and you have a reconciliation room, meaning if secondary screening cannot determine what is alarming about a particular bag … the bag stays qualified as suspect and goes to the reconciliation room.
"Once a bag is cleared, it then goes to a make-up unit. A minimum of 5-10 minutes per bag has been added to each bag's travel time through the airport; that affects everybody in the operations chain."
Point to point transfer of baggage; higher throughput
If an airport is designed with the intent of taking bags from the curbside or ticket counter directly to the gate and the real estate is available, it can be done. However, the majority of the airports in the U.S. are small, and the cost to upgrade them to allow a point-to-point transfer of a bag is not reasonable for most, relates Ineichen.
As far as the future is concerned, "There are x-ray screening machines being tested currently that allow a baggage throughput of anywhere from 700 to 1,000 bags per hour, which means the conveyor system on both the front and back ends has to be a lot faster," says Ineichen.
"This also means you need more real estate; for some of the airports today where there is a retrofitting of the BHS, the space is just not there.
"How does a system of the future be adapted to allow for a high-throughput machine? The designs could become more complex, because if you have a higher throughput on one end, you will need more resources on the other , including TSA, airline bag handling ops, etc. It will be interesting to see how it will evolve."
About the Author
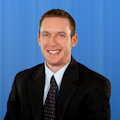