Industry Viewpoint: Corrosion Detection in GA Aircraft
Soaring fuel prices and a tanked economy have unfortunately grounded more and more general aviation aircraft for longer and longer periods of time. For GA pilots, this has meant a sad curtailing of a favorite pastime. For the mechanics who maintain these aircraft, time not flown means greater challenges in corrosion detection.
As many of you know, the longer these aircraft spend on the ground, the more vulnerable they are to the effects of humid and coastal climates. The damp, wet air is a perfect “breeding” ground for corrosion; the salty air common in coastal areas is even more corrosive. Spend enough time on the ground in these locations (where the heat of the day and the cool of night results in condensation) and corrosion springs up in unexpected places and its effects become more pronounced. Usually corrosion is found where water tends to settle or close to the ground. But constant exposure to optimal conditions and corrosion can wind up in unusual places. And it’s not just GA; major airlines are not immune. Back in the '70s, I recall a brand-new aircraft USAir leased to Hawaiian Airlines ended up with corrosion above the overhead luggage bins after just one year of island hopping in the Pacific. Up until then, no one I worked with had ever found corrosion in that location.
Because GA aircraft are spending more time on the ground, the jobs of mechanics conducting annual inspections has been made that much more difficult – and critical. The effects of corrosion on safety are well known. The metal breaks down and loses its structural integrity. Loss of integrity can and has led to loss of structural strength with catastrophic results.
Aircraft skin corrosion is particularly insidious because it tends to start in areas that are difficult to see, such as lap joints where it can grow unobserved between layers of metal and crevices, which are any areas where moisture can collect. But corrosion or rust is frequently observed on other parts, even stainless steel will corrode under the right conditions.
The good news for aircraft owners is that corrosion caught early can be relatively inexpensive to fix. But wait too long and repair and replacement costs escalate rapidly. While minor corrosion can be ground out or sanded, more extensive corrosion will require skin or part replacement. The best mechanics, of course, are the ones who find corrosion early and are able to mitigate its impacts before costly repairs are needed.
My experience has been that the best way to do a thorough corrosion inspection is to develop a routine so that you have a consistent approach and methodology to your inspection. Some suggestions: 1. familiarize yourself with corrosion indicators – such as bubbling paint; 2. conduct the inspection as a separate item on your annual inspection checklist; 3. plan ahead with the proper tools, including picks and scrapers; 4. establish beforehand appropriate start and stop points; and 5. always remember to look at the hard-to-reach areas, that’s where corrosion tends to hide.
About the Author
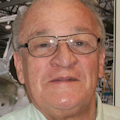
John Goglia
John Goglia has 40+ years experience in the aviation industry. He was the first NTSB member to hold an FAA aircraft mechanic's certificate. He can be reached at [email protected].
John Goglia is an independent aviation safety consultant and Adjunct Professor at Vaughn College of Aeronautics and Technology and regular monthly columnist for four aviation trade publications. He was an airline mechanic for more than 30 years. He has co-authored two text books (Safety Management Systems in Aviation, Ashgate Publishing 2009 and Implementation of Safety Management Systems in Aviation, Ashgate Publishing 2011).