The Wall Street Heliport New Fuel Farm
The Wall Street or Downtown Manhattan Heliport (JRB) is located on Pier 6 on the East River which separates Manhattan and Queens in New York City. First opened in 1960 and operated by the Port Authority of NY & NJ, it was given back to the New York City Economic Development Corporation (EDC) in 2007. The Aviation Department called for bids from a fixed base operator (FBO) to operate the heliport and a lease was subsequently executed with Saker Aviation. The lease stipulated that the FBO operate the heliport provisioned with a helicopter fueling system.
The configuration of the heliport is indicated in aerial photo Photo #1. The Flight Operations Office is located on Pier 6, approximately 100 feet from the Manhattan shore of the East River.
The two helicopter fueling positions are situated on an attached pier on the north side of Pier 6, approximately 500 feet from shore. Fuel deliveries must be made from South Street, adjacent to FDR Drive. Therefore, the fuel storage tank had to be located on the pier immediately adjacent to South Street, approximately 650 feet from two remote dispensing cabinets further out on the pier at two helicopter fueling positions indicated in Photo #1.
Multi-jurisdictional permits
Eryou Engineering was retained to design, permit, and manage the installation of the new helicopter fueling system at JRB. The permits for the project were multi-jurisdictional, involving the following agencies:
• The NYC Fire Department (FDNY) which performs technical reviews of the proposed fueling system construction documents.
• The Waterfront Business Unit of the NYC Department of Buildings (DOB) which issues the building permit for waterfront properties in NYC.
• The NYC Police Department (NYPD) Anti-Terrorism Unit which approves the tank protection system design.
• The NYC Department of Transportation (NYCDOT) which controls the movement of heavy loads on roads and also crane permits within the city.
• The NY State Department of Environmental Conservation, which oversees the design of fuel storage tanks that can discharge to surface waters (i.e., the East River).
• The Federal Secret Service since Marine One uses JRB during Presidential visits to Manhattan.
• The Federal Environmental Protection Agency, which administers Prevention Countermeasure and Control Plan (SPCC) programs.
• The Federal Aviation Administraioin, which controls potential landing/takeoff obstacles within airports.
• The Air Transport Association of America (ATA) Specification 103 “Standard for Jet Fuel Quality Control at Airports” which governs jet fuel quality for fixed wing aircraft and helicopters.
The city’s fire regulations permit the use of fire-rated UL 2085 listed above ground tanks (ASTs) up to 4,000 gallons capacity for fleet refueling of combustible fuels (diesel or jet fuel) without a variance. Considering the load limitations on Pier 6 and the projected daily fuel consumption at the heliport, a 4,000-gallon fuel tank was adequate for JRB fueling operations.
Design challenges
Design drawings were prepared for a 4,000gallon above ground jet fuel storage tank with a truck unloading pump at the foot of Pier 6, adjacent to South Street, supplying two remote dispensing cabinets which are located approximately 50 feet from the fuel supply tank. The multiple design challenges included the following ...
The FDNY’s tank standards required that the jet fuel storage tank have a UL-specified fire rating, while the NYPD requirements included ballistic and explosion resistance requirements. Due to the marine environment and the FDNY/NYPD requirements, a concrete encased Convault tank meeting UL2085 requirements was selected. The tank is indicated in Photo 868.
The NYPD Anti-Terrorism Unit requires that the AST be protected from vehicular traffic on FDR Drive by a K-rated bollard system. A bollard system anchored into the 30-inch thick reinforced concrete deck of Pier 6 was designed and installed.
Since Marine One lands at JRB, the Secret Service (SS) required that the tank openings be secured with SS seals before the tank itself was put into service. To accommodate these requirements, the tank top openings were modified.
The remote fuel dispensing systems at the helicopter fueling pier had to be overhung from the side of the pier because of FAA regulations which would not allow them to protrude above the 8-inch high curbing on the edge of the heliport.
The cabinets contained final fuel filters, a fuel meter, and an electric wind hose reel for 60 feet of one-inch hose plus a static cable reel. The remote dispenser cabinets were fabricated from marine grade aluminum and connected to the pier by a welded structural framework. The latter was metalized with a zinc coating to minimize corrosion as indicated in Photo #463. The completed dispenser cabinet is shown in Photo # 5.
The 650-foot long supply pipe from the AST to the two dispensing cabinets at the helicopter fueling areas posed a major design challenge. The pipe had to penetrate the deck of Pier 6 adjacent to the AST, travel to the north side of Pier 6, then travel on the north side of Pier 6 and the adjacent pier to reach the remote dispensing cabinets.
Under FDNY requirements, the pipe had to be metallic and fire resistant. The New York State Department of Environmental Conservation requirements necessitated a double-walled fuel pipe. ATA Specification 103 requires that the interior of the pipe be non-corrosive to ensure proper fuel quality. Additionally, it had to be resistant to corrosion by saltwater and to possible damage from floating objects in the East River.
After careful consideration, it was determined that the only product meeting these numerous requirements was a double-walled, flexible, convoluted stainless steel tubing manufactured by Brugg. A 1.5-inch ID Brugg double-wall flexible pipe was installed at the heliport in a single 650-foot continuous length, along with a factory supplied leak detection system.
FDNY stipulated that a horizontal foam standpipe be installed from the sidewalk on FDR Drive to the end of Pier 6. This standpipe was installed to allow fire trucks to supply firefighting foam to five fire hose connections along the standpipe to fight helicopter fueling fires on Pier 6.
The construction phase
Four major tasks during the construction phase posed serious challenges:
• The 650 feet of Brugg double-wall flexible piping arrived in a large roll (Photo #431). The pipe installation under the pier and along the north edge of the pier was done using a modified boom lift as indicated in Photo #426. The installed Brugg pipe is indicated in Photos # 068 and 451.
• Installation of 650 feet of foam standpipe piping along the north edge of the pier. The foam standpipe is indicated in Photos #068 and 868.
• Coordination of the FDNY inspections and tests with the work schedule.
• Installation of the concrete-encased AST, which weighed 20 tons. The NYCDOT was approached for a crane permit to lift the AST from a low-boy trailer on FDR Drive onto Pier 6, but DOT cited concerns regarding the structural capacity of the bulkhead wall at the base of Pier 6. The problem was resolved with the use of a crane-equipped floating barge which picked up the tank at Port Newark in New Jersey, floated it to Pier 6, and then lifted it onto the pier. Photo 040 depicts the barge crane lifting the tank onto Pier 6. Photo #777 indicates the tank and pumping cabinet adjacent to South Street.
Operations
Photo #873 indicates the configuration of the two remote dispensing cabinets which have been fueling helicopters since September 2010. Photos #9 and #10 depict routine helicopter fueling operations with flow rates up to 30 gpm for each helicopter.
Fuel spill prevention
Due to the location of the fueling system, on Pier 6 over the East River, fuel spill avoidance was designed into every aspect of the operation.
The above ground storage tank is equipped with an Omntec tank management system which indicates the amount of fuel in the tank. Loads are not ordered until there is enough ullage in the tank to accept the incoming load.
The tank is equipped with an overfill alarm system and a float actuated hydraulic overfill valve to preclude spills from tank overfilling.
A spill pan is incorporated into the pump/filter unit and both remote dispensing cabinets. Fuel detection sensors located in these spill pans are tied into the Omntec tank management system, which was programmed to sound an alarm if a spill is detected.
The 650 foot long supply pipe from the AST to the remote dispensing cabinets is a Brugg double-wall stainless steel pipe, equipped with a continuous leak detection monitoring system.
Fuel spill control
In the unlikely event of a spill at the truck unloading area on the north side of the AST, a fuel spill barrier has been installed with integral fuel-absorbing filters located adjacent to the scupper drain locations to keep spilled fuel from draining into the East River.
A similar fuel-absorbing filter is installed in the deck storm drains adjacent to the helicopter fueling positions. In addition, a Spill Prevention, Containment and Countermeasure Plan (SPCC Plan) was prepared and it requires that a spill kit, including booms, be kept on site and that a marine spill recovery firm be retained.
About the Author
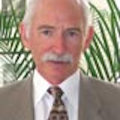